Induction heating is a highly efficient and rapid method of heating conductive materials by generating heat internally through electromagnetic induction. The process requires two fundamental components: a changing magnetic field and an electrically conductive material. Beyond these basics, the design and efficiency of an induction heating system depend on several factors, including the material's properties, the system's power supply, the inductor coil design, and the specific application requirements. This method is versatile, allowing heating in various environments without direct contact, making it ideal for applications where contamination is a concern.
Key Points Explained:
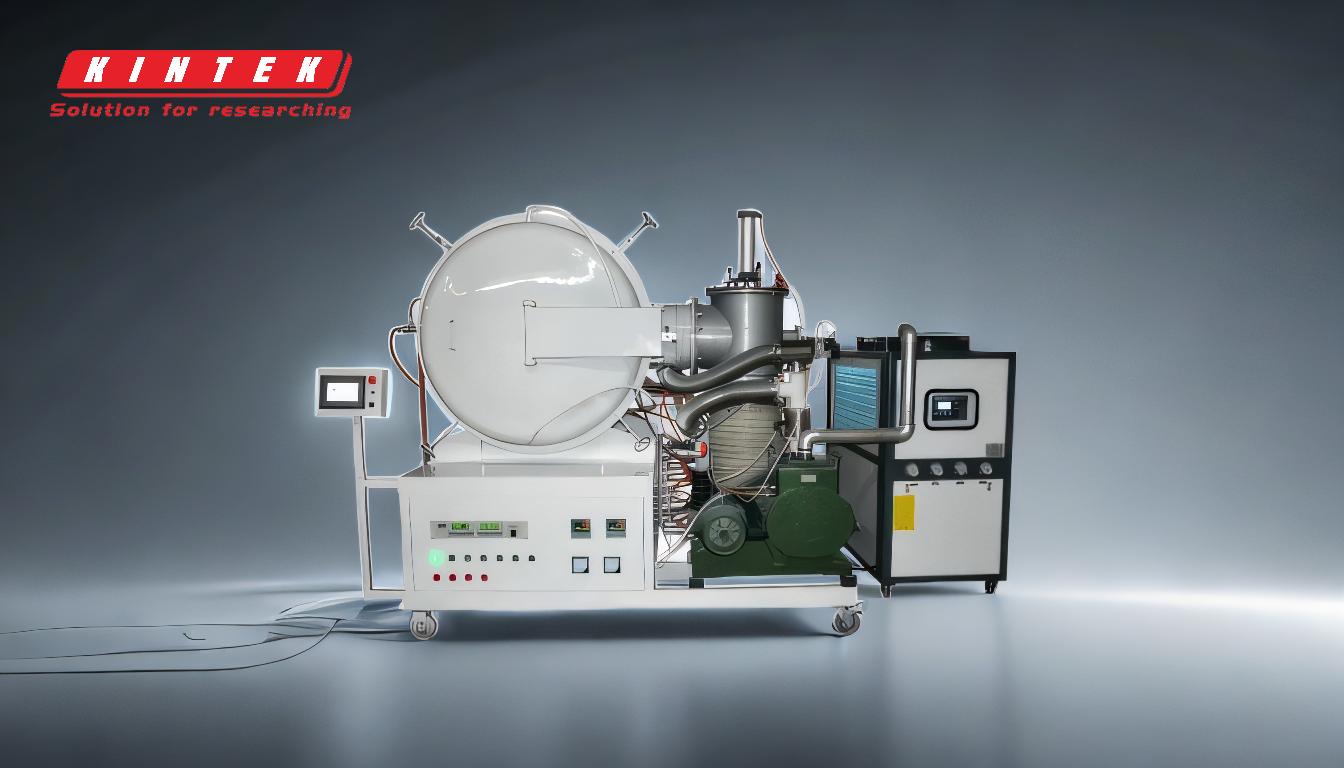
-
Basic Requirements for Induction Heating:
- Changing Magnetic Field: A key requirement is the presence of a changing magnetic field, typically created by an alternating current (AC) passing through an inductor coil. This magnetic field induces eddy currents in the conductive material.
- Electrically Conductive Material: The material to be heated must be electrically conductive. Metals like steel, copper, and aluminum are commonly used. The induced eddy currents generate heat due to the material's electrical resistance.
-
Material Considerations:
- Type of Material: Induction heating is most effective with metals and other conductive materials. The material's resistivity plays a significant role; higher resistivity materials heat faster due to greater resistance to the induced currents.
- Size and Thickness: Smaller and thinner materials heat more quickly than larger or thicker ones. This is because the induced currents can penetrate more effectively, and the heat generated is concentrated in a smaller volume.
-
Frequency of Alternating Current:
- Heating Depth: The frequency of the AC used in the inductor coil affects the depth of heating. Higher frequencies result in shallower heating depths, which is ideal for surface heating applications. Lower frequencies are better suited for deeper penetration in thicker materials.
-
Inductor Coil Design:
- Coil Configuration: The design of the inductor coil is crucial for efficient heating. The coil must be shaped and positioned to ensure optimal magnetic field distribution around the material. Custom coil designs are often required for specific applications.
- Efficiency: The efficiency of the induction heating system is influenced by the inductor design. Proper coil design minimizes energy loss and ensures uniform heating.
-
Power Supply Capacity:
- Energy Requirements: The power supply must be capable of delivering sufficient energy to achieve the desired temperature rise. This depends on the material's specific heat, mass, and the required temperature change.
- Heat Loss Considerations: The power supply must also account for heat loss due to conduction, convection, and radiation. Insulating the material or the heating environment can help minimize these losses.
-
Environmental Considerations:
- Versatility: Induction heating can be performed in various environments, including liquids, gases, or even a vacuum. This versatility makes it suitable for applications where contamination or direct contact with a heat source is a concern.
- Isolation: The material can be covered by an isolating substance or submerged in a liquid without affecting the heating process, as there is no direct contact with the heat source.
-
Efficiency and Application-Specific Requirements:
- Temperature Variation: The efficiency of induction heating depends on the degree of temperature variation required. Applications requiring a wide range of temperature changes may need more power to achieve the desired results.
- System Efficiency: Overall system efficiency is influenced by the characteristics of the material, the inductor design, and the power supply capacity. Optimizing these factors ensures effective and energy-efficient heating.
In conclusion, induction heating is a versatile and efficient method for heating conductive materials, with specific requirements and considerations that must be addressed to achieve optimal results. By understanding and carefully designing the system around the material properties, power supply, and environmental factors, induction heating can be effectively utilized in a wide range of industrial and manufacturing applications.
Summary Table:
Key Aspect | Details |
---|---|
Basic Requirements | Changing magnetic field, electrically conductive material |
Material Considerations | Type, resistivity, size, and thickness of the material |
Frequency of AC | Higher frequencies for shallow heating; lower frequencies for deeper heating |
Inductor Coil Design | Custom designs for optimal magnetic field distribution and efficiency |
Power Supply Capacity | Sufficient energy to achieve desired temperature rise, accounting for heat loss |
Environmental Considerations | Versatile environments (liquids, gases, vacuum), isolation options |
Efficiency Factors | Material properties, inductor design, power supply, and temperature range |
Discover how induction heating can optimize your processes—contact our experts today!