Forging is a high-risk industrial process that involves shaping metal using localized compressive forces, often at high temperatures. Safety precautions are critical to prevent injuries, equipment damage, and workplace hazards. Key safety measures include wearing appropriate personal protective equipment (PPE), ensuring proper training for operators, maintaining equipment, and adhering to safe operating procedures. Additionally, environmental controls, such as ventilation and fire safety measures, are essential to mitigate risks associated with heat, sparks, and fumes. By following these precautions, workplaces can ensure a safer forging environment.
Key Points Explained:
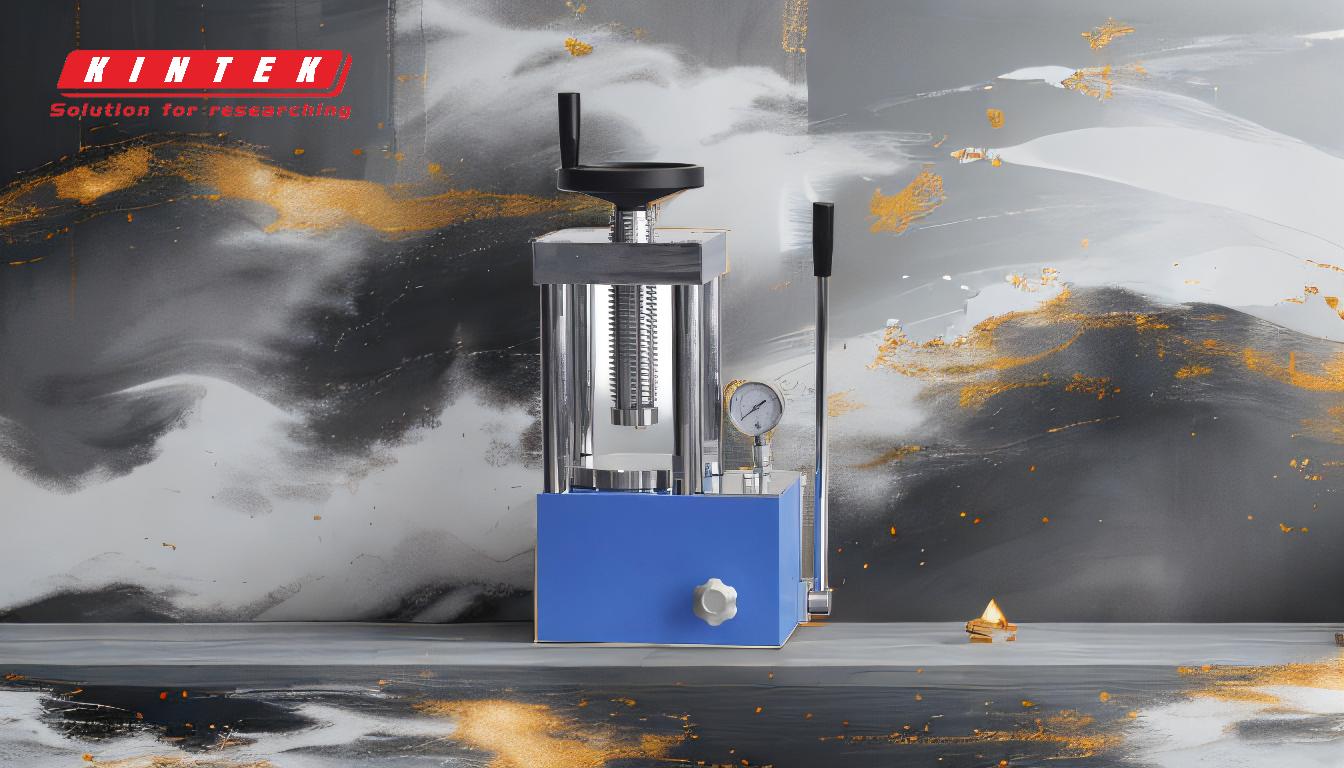
-
Personal Protective Equipment (PPE):
- Heat-resistant gloves: Protect hands from burns caused by hot metal and equipment.
- Safety goggles or face shields: Shield eyes from sparks, flying debris, and intense light.
- Fire-resistant clothing: Minimize the risk of burns from hot materials or accidental fires.
- Steel-toed boots: Protect feet from heavy objects and accidental drops.
- Ear protection: Reduce noise exposure from forging hammers and machinery.
-
Training and Awareness:
- Operator training: Ensure all personnel are trained in safe forging practices, including handling tools, operating machinery, and emergency procedures.
- Hazard recognition: Educate workers on identifying potential risks, such as overheating equipment, improper tool usage, or unsafe material handling.
- Emergency response: Train staff on first aid, fire extinguisher use, and evacuation protocols.
-
Equipment Maintenance and Inspection:
- Regular maintenance: Inspect and service forging equipment, such as hammers, presses, and furnaces, to prevent malfunctions.
- Tool integrity: Check tools for wear, cracks, or damage before use to avoid accidents.
- Temperature controls: Monitor and maintain proper heating levels to prevent overheating or underheating of materials.
-
Safe Operating Procedures:
- Material handling: Use proper lifting techniques and equipment to move heavy materials safely.
- Work area organization: Keep the forging area clean and free of clutter to reduce tripping hazards.
- Controlled heating: Avoid overheating metals, which can lead to splattering or explosions.
- Machine guarding: Ensure all machinery has appropriate guards to prevent contact with moving parts.
-
Environmental Controls:
- Ventilation: Install proper ventilation systems to remove fumes, dust, and gases generated during forging.
- Fire safety: Keep fire extinguishers, sand buckets, or other fire suppression tools readily available.
- Noise reduction: Implement soundproofing measures or provide ear protection to minimize noise-related health risks.
-
Emergency Preparedness:
- First aid stations: Ensure easy access to first aid kits and trained personnel.
- Fire drills: Conduct regular fire drills to prepare workers for emergencies.
- Clear signage: Post safety instructions, hazard warnings, and emergency exit routes prominently.
By adhering to these safety precautions, forging operations can significantly reduce the risk of accidents and create a safer workplace for all personnel involved.
Summary Table:
Category | Key Safety Measures |
---|---|
Personal Protective Equipment (PPE) | - Heat-resistant gloves - Safety goggles/face shields - Fire-resistant clothing - Steel-toed boots - Ear protection |
Training and Awareness | - Operator training - Hazard recognition - Emergency response protocols |
Equipment Maintenance | - Regular maintenance - Tool integrity checks - Temperature controls |
Safe Operating Procedures | - Proper material handling - Work area organization - Controlled heating - Machine guarding |
Environmental Controls | - Ventilation systems - Fire safety tools - Noise reduction measures |
Emergency Preparedness | - First aid stations - Fire drills - Clear signage and exit routes |
Ensure a safer forging environment—contact our experts today for tailored safety solutions!