Chemical vapor deposition (CVD) is a widely used method for depositing thin films on substrates through chemical reactions in the vapor phase. The process involves several key steps, including precursor injection, gas-phase reactions, and film deposition on the substrate. CVD is used in various industries, particularly in microelectronics, due to its ability to produce high-quality, uniform coatings. The method can be enhanced using techniques like plasma-enhanced chemical vapor deposition (PECVD), which lowers the deposition temperature and energy consumption. Below, the steps of the CVD process are explained in detail, along with their significance.
Key Points Explained:
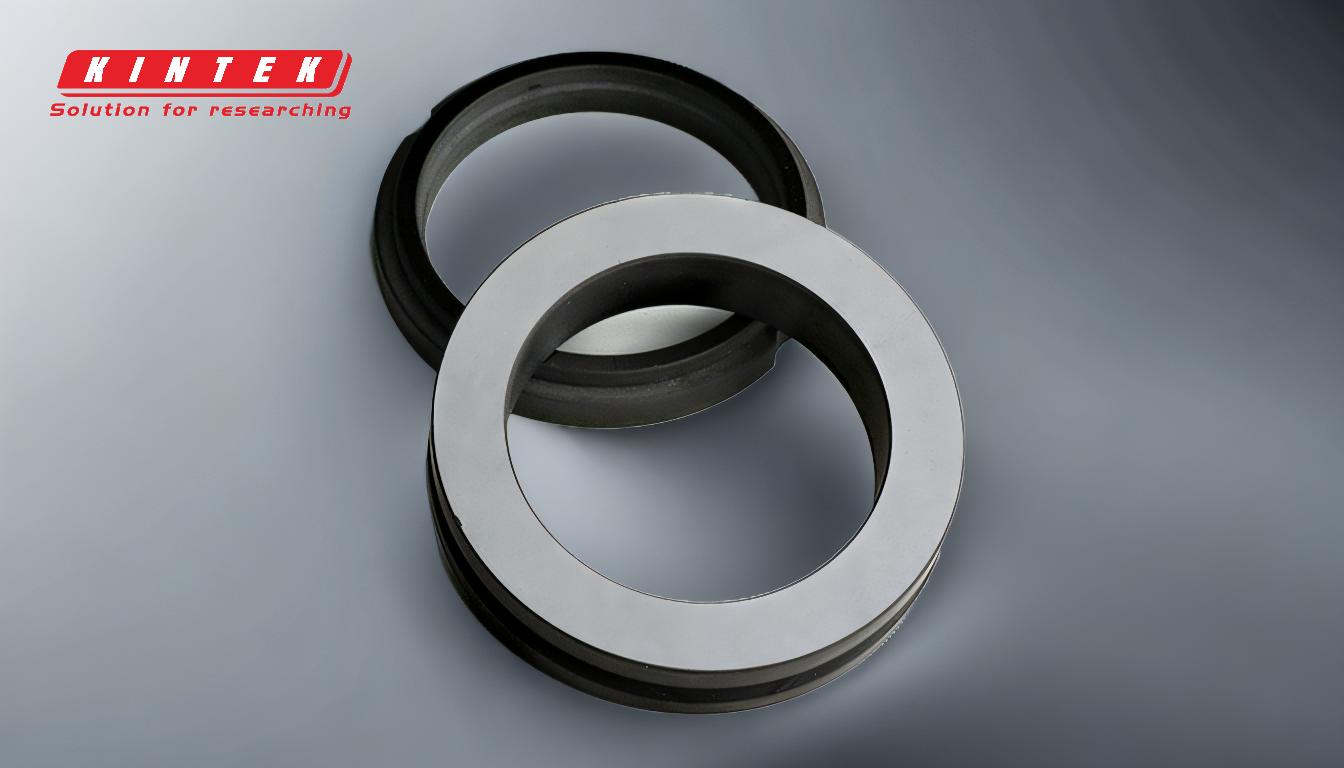
-
Precursor Injection
- The CVD process begins with the introduction of a volatile precursor gas into a reaction chamber. This precursor is typically a gas or vaporized liquid/solid that contains the elements required for the desired coating.
- The precursor is chosen based on the material to be deposited. Common precursors include silane, organometallic compounds, or metal coordination complexes.
- The precursor is injected into the chamber under controlled conditions, often with a carrier gas to ensure uniform distribution.
-
Gas Transport and Heating
- Once injected, the precursor gas is transported to the substrate surface. This is often done under vacuum or low-pressure conditions to enhance gas flow and reduce contamination.
- The substrate is heated to a specific reaction temperature, which is critical for initiating the chemical reactions. The temperature depends on the precursor and the desired film properties.
- Heating can be achieved using resistive heating, induction heating, or other methods, depending on the setup.
-
Chemical Reaction and Decomposition
- At the reaction temperature, the precursor gas undergoes thermal decomposition or reacts with other gases in the chamber. This step is crucial for breaking down the precursor into its constituent elements or molecules.
- The chemical reactions occur either on the substrate surface (heterogeneous reactions) or in the gas phase (homogeneous reactions).
- For example, in the case of silicon deposition, silane (SiH₄) decomposes into silicon and hydrogen gas.
-
Film Deposition
- The decomposed or reacted species then deposit onto the substrate surface, forming a thin film. The deposition process is influenced by factors such as temperature, pressure, and precursor concentration.
- The film can be crystalline, amorphous, or a combination of both, depending on the deposition conditions.
- The deposition continues until the desired film thickness is achieved.
-
Byproduct Removal
- During the chemical reactions, byproducts such as gases or volatile compounds are generated. These byproducts must be removed from the chamber to prevent contamination and ensure the purity of the deposited film.
- The byproducts are typically exhausted through a vacuum system or scrubbed using appropriate filters.
-
Cooling and Post-Processing
- After deposition, the substrate is cooled to room temperature. This step is critical to prevent thermal stress or cracking in the deposited film.
- Post-processing steps, such as annealing or surface treatment, may be performed to enhance the film's properties, such as adhesion, density, or crystallinity.
-
Advancements in CVD Techniques
- Plasma-Enhanced Chemical Vapor Deposition (PECVD): This technique uses plasma to excite the precursor gas, allowing deposition at lower temperatures. PECVD is particularly useful for temperature-sensitive substrates.
- Atomic Layer Deposition (ALD): A variant of CVD that allows for precise control of film thickness at the atomic level by alternating precursor pulses.
- Low-Pressure CVD (LPCVD) and Atmospheric Pressure CVD (APCVD): These methods differ in the pressure conditions used during deposition, affecting film quality and deposition rate.
By following these steps, the CVD process enables the production of high-quality thin films with excellent uniformity and adhesion. Its versatility and scalability make it a cornerstone technology in industries such as semiconductors, optics, and coatings.
Summary Table:
Step | Description |
---|---|
1. Precursor Injection | Introduction of volatile precursor gas into the reaction chamber. |
2. Gas Transport and Heating | Transport of precursor gas to the substrate under controlled heating conditions. |
3. Chemical Reaction | Thermal decomposition or reaction of precursor gas to form deposition species. |
4. Film Deposition | Deposition of decomposed species onto the substrate to form a thin film. |
5. Byproduct Removal | Removal of byproducts to ensure film purity and prevent contamination. |
6. Cooling and Post-Processing | Cooling the substrate and enhancing film properties through post-processing. |
7. Advancements in CVD | Techniques like PECVD, ALD, LPCVD, and APCVD for improved performance. |
Discover how CVD can revolutionize your thin film production—contact our experts today!