Quenching is a critical heat treatment process used to alter the microstructure of materials, such as metals and fine ceramics, to achieve desired mechanical properties like hardness, strength, and toughness. The two primary types of quenching are direct quenching and time quenching. Direct quenching involves rapidly cooling a material from a high temperature to room temperature, typically using mediums like water, oil, or air. Time quenching, on the other hand, involves cooling the material to a specific temperature and holding it there for a predetermined time before further cooling. Both methods are essential in fine ceramics and metallurgy to achieve specific material properties.
Key Points Explained:
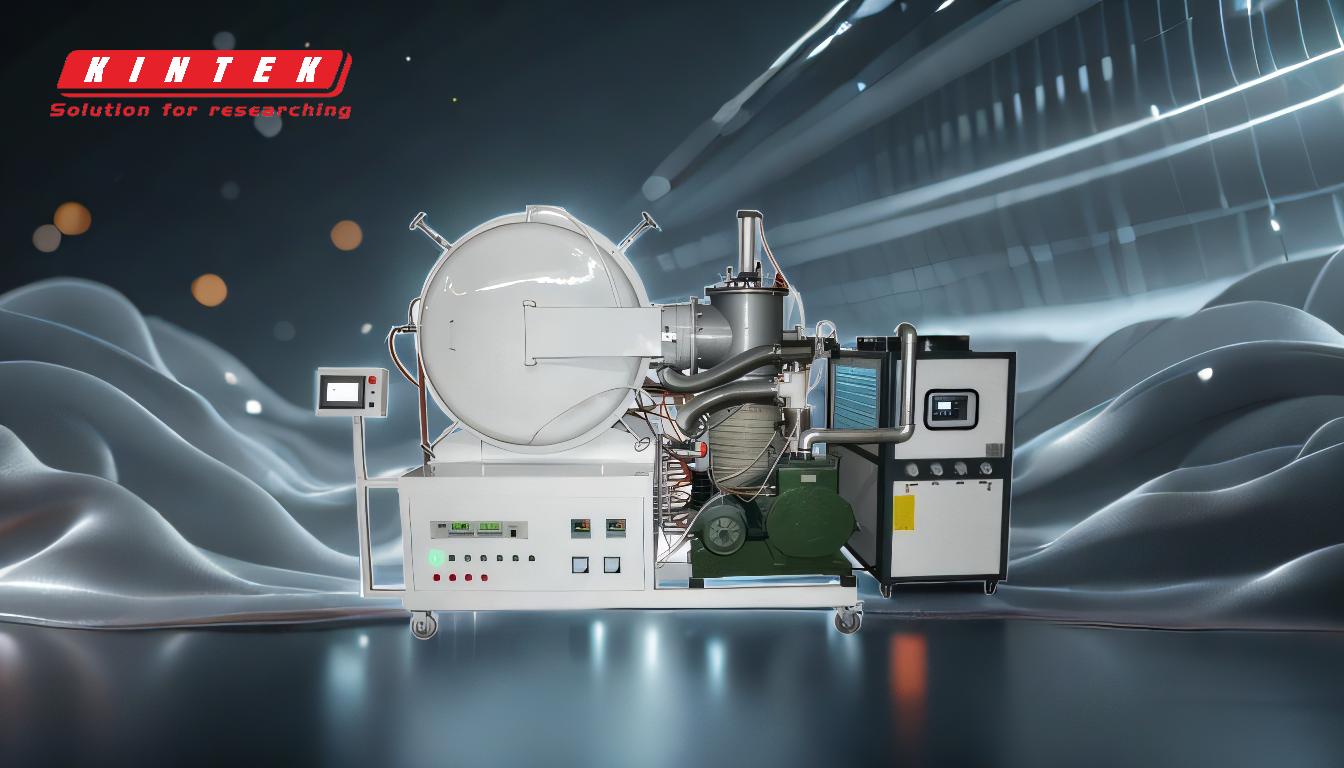
-
Direct Quenching:
- Definition: Direct quenching involves rapidly cooling a material from its austenitizing temperature (typically above 900°C for steel) to room temperature using a quenching medium.
- Quenching Mediums: Common mediums include water, oil, and air. Water provides the fastest cooling rate, while oil offers a slower, more controlled cooling process, reducing the risk of cracking or distortion.
- Applications: Direct quenching is widely used in industries requiring high hardness and wear resistance, such as tool steel manufacturing and fine ceramics processing.
- Advantages: It is a straightforward and efficient method to achieve high hardness and strength in materials.
- Challenges: Rapid cooling can lead to internal stresses, distortion, or cracking, especially in complex geometries or brittle materials like fine ceramics.
-
Time Quenching:
- Definition: Time quenching, also known as interrupted quenching or martempering, involves cooling the material to a specific intermediate temperature (above the martensite start temperature) and holding it there for a set period before further cooling.
-
Process Steps:
- Rapidly cool the material to the intermediate temperature.
- Hold at this temperature to allow uniform temperature distribution.
- Continue cooling to room temperature.
- Applications: This method is particularly useful for materials requiring a balance of hardness and toughness, such as gears, springs, and fine ceramics.
- Advantages: Reduces thermal stresses and minimizes the risk of cracking or distortion, making it suitable for complex shapes and brittle materials.
- Challenges: Requires precise control of temperature and timing, which can increase process complexity and cost.
-
Comparison of Direct and Time Quenching:
- Cooling Rate: Direct quenching has a faster cooling rate, while time quenching allows for controlled cooling at critical stages.
- Material Properties: Direct quenching maximizes hardness but may compromise toughness, whereas time quenching balances hardness and toughness.
- Risk of Defects: Direct quenching has a higher risk of cracking and distortion, while time quenching minimizes these risks.
- Complexity: Time quenching is more complex and requires precise control, making it less suitable for high-volume production compared to direct quenching.
-
Relevance to Fine Ceramics:
- Fine ceramics often undergo quenching to enhance their mechanical properties, such as hardness and fracture toughness. The choice between direct and time quenching depends on the specific application and desired properties. For example, fine ceramics used in cutting tools may benefit from direct quenching to achieve maximum hardness, while those used in structural components may require time quenching to balance hardness and toughness.
By understanding the differences between direct and time quenching, manufacturers can select the appropriate method to achieve the desired material properties for their specific applications, including fine ceramics.
Summary Table:
Aspect | Direct Quenching | Time Quenching |
---|---|---|
Definition | Rapid cooling to room temperature | Cooling to an intermediate temperature, then holding before further cooling |
Cooling Rate | Fast | Controlled |
Applications | Tool steel, fine ceramics (high hardness) | Gears, springs, fine ceramics (balance of hardness & toughness) |
Advantages | High hardness and strength | Reduces cracking and distortion |
Challenges | Risk of cracking and distortion | Requires precise temperature and timing control |
Complexity | Simple | More complex |
Need help choosing the right quenching method for your materials? Contact our experts today!