Sintering is a critical process in materials science and manufacturing, used to create solid structures from powdered materials by applying heat and sometimes pressure. The two primary types of sintering are solid phase sintering and liquid phase sintering. Solid phase sintering involves heating powdered materials just below their melting point to bond particles through atomic diffusion, resulting in a solid-state structure. Liquid phase sintering, on the other hand, introduces a liquid phase during the process to enhance densification and bonding, which is later removed by heating. These two types of sintering are fundamental to various industrial applications, including ceramics, metals, and advanced manufacturing techniques like 3D printing.
Key Points Explained:
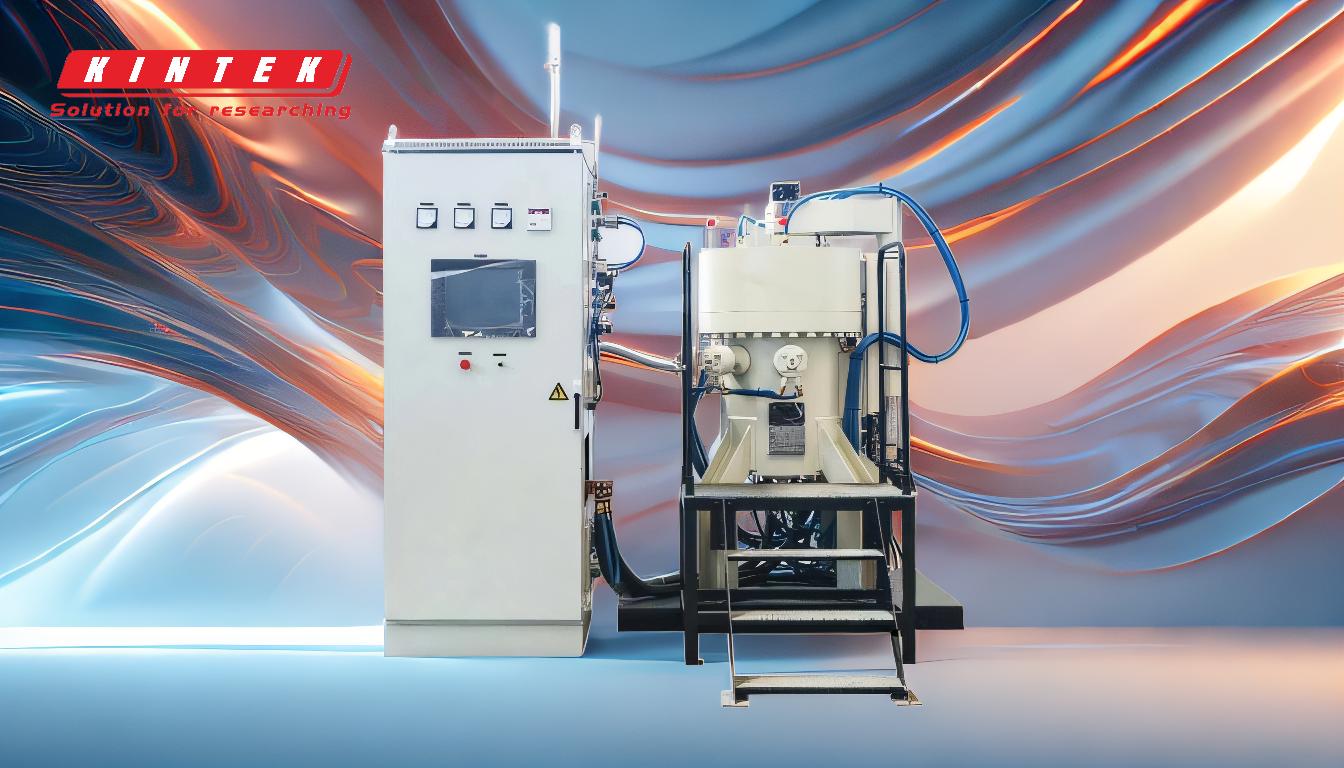
-
Solid Phase Sintering:
- Definition: Solid phase sintering occurs when powdered materials are heated to a temperature just below their melting point, causing particles to bond through atomic diffusion without the presence of a liquid phase.
- Process: The process involves the compaction of powdered materials into a desired shape, followed by heating. The heat causes the particles to diffuse and bond, reducing porosity and increasing density.
- Applications: This type of sintering is commonly used in the production of ceramics, metals, and other materials where high strength and low porosity are required. It is particularly useful in manufacturing components like gears, bearings, and structural parts.
- Advantages: Solid phase sintering produces materials with high mechanical strength and thermal stability. It is also relatively simple and cost-effective compared to other sintering methods.
-
Liquid Phase Sintering:
- Definition: Liquid phase sintering involves the introduction of a liquid phase during the sintering process, which enhances densification and bonding between particles. The liquid phase is typically a solvent or binder that is later driven off by heating.
- Process: The powdered material is mixed with a liquid phase, which helps to fill the gaps between particles and promote bonding. Upon heating, the liquid phase facilitates the movement of particles, leading to densification. The liquid is eventually evaporated or otherwise removed, leaving behind a solid, dense material.
- Applications: This method is widely used in the production of advanced ceramics, cemented carbides, and certain metal alloys. It is particularly effective for materials that are difficult to sinter using solid phase methods due to high melting points or poor diffusion properties.
- Advantages: Liquid phase sintering allows for the production of materials with very low porosity and high density. It also enables the sintering of materials that would otherwise be difficult to process, such as tungsten carbide and other hard metals.
-
Comparison of Solid Phase and Liquid Phase Sintering:
- Temperature Requirements: Solid phase sintering typically requires lower temperatures compared to liquid phase sintering, as it does not involve the melting of a secondary phase.
- Material Suitability: Solid phase sintering is more suitable for materials that can achieve sufficient diffusion at lower temperatures, while liquid phase sintering is better for materials that require additional assistance in densification.
- End Product Properties: Solid phase sintering generally produces materials with higher mechanical strength, while liquid phase sintering can achieve higher densities and better bonding in certain materials.
-
Other Sintering Techniques:
- Reactive Sintering: This involves a chemical reaction between the powder particles during the sintering process, which can enhance bonding and densification.
- Microwave Sintering: This method uses microwave energy to heat the material, allowing for faster and more uniform heating compared to conventional methods.
- Spark Plasma Sintering (SPS): SPS uses an electric current and physical compression to rapidly sinter materials, making it suitable for advanced materials and complex shapes. Learn more about spark plasma sintering furnace.
- Hot Isostatic Pressing (HIP): HIP applies high pressure and temperature simultaneously to achieve full densification and improved material properties.
In summary, the two main types of sintering, solid phase and liquid phase, are essential for creating dense, strong materials from powdered precursors. Each method has its own advantages and is suited to different materials and applications, making sintering a versatile and widely used process in materials science and manufacturing.
Summary Table:
Aspect | Solid Phase Sintering | Liquid Phase Sintering |
---|---|---|
Definition | Bonding particles through atomic diffusion without a liquid phase. | Introduces a liquid phase to enhance densification and bonding. |
Process | Compaction and heating below melting point. | Mixing with a liquid phase, heating, and removing the liquid. |
Applications | Ceramics, metals, gears, bearings, structural parts. | Advanced ceramics, cemented carbides, hard metals. |
Advantages | High mechanical strength, thermal stability, cost-effective. | Very low porosity, high density, suitable for hard-to-sinter materials. |
Temperature | Lower temperatures. | Higher temperatures due to liquid phase. |
End Product | Higher mechanical strength. | Higher density and better bonding. |
Learn more about sintering techniques and how they can benefit your projects—contact our experts today!