Brazing is a metal-joining process that involves melting a filler metal into a joint to create a strong bond between two or more metal parts. The process is widely used in various industries due to its ability to join dissimilar metals and create durable, leak-proof joints. Three primary types of brazing are torch brazing, furnace brazing, and induction brazing. Each method has its unique advantages, applications, and considerations, making them suitable for different industrial needs. Below, we explore these three types in detail, highlighting their processes, benefits, and typical use cases.
Key Points Explained:
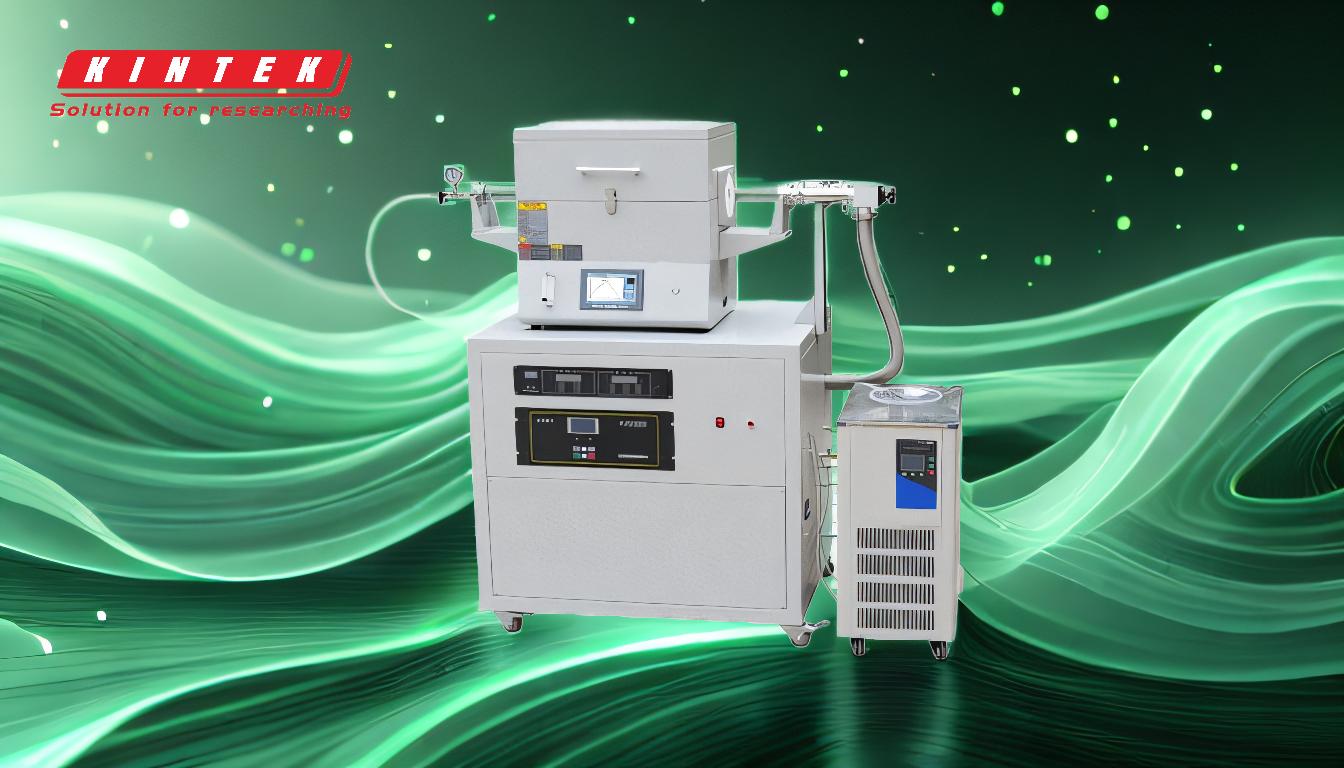
-
Torch Brazing
- Process: Torch brazing involves using a gas-fueled torch to heat the filler metal and the base metals until the filler metal melts and flows into the joint. The heat is applied directly to the workpiece, and the process can be manual or automated.
-
Advantages:
- Highly versatile and portable, making it suitable for on-site repairs and small-scale production.
- Allows precise control over the heat application, which is ideal for complex or delicate parts.
- Cost-effective for low-volume or custom jobs.
- Applications: Commonly used in HVAC systems, plumbing, automotive repairs, and jewelry making.
- Considerations: Requires skilled operators to avoid overheating or uneven heating, which can weaken the joint.
-
Furnace Brazing
- Process: Furnace brazing involves placing the assembled parts and filler metal into a furnace, where the entire assembly is heated to the brazing temperature. The furnace provides uniform heat distribution, ensuring consistent results.
-
Advantages:
- Ideal for high-volume production due to its ability to handle multiple parts simultaneously.
- Provides excellent control over the heating environment, reducing the risk of oxidation and contamination.
- Suitable for joining complex assemblies with multiple joints.
- Applications: Widely used in aerospace, automotive, and electronics industries for components like heat exchangers, sensors, and circuit boards.
- Considerations: Requires specialized equipment and a controlled atmosphere (e.g., vacuum or inert gas) to prevent oxidation.
-
Induction Brazing
- Process: Induction brazing uses electromagnetic induction to generate heat directly within the workpiece. The filler metal is pre-placed in the joint, and an induction coil creates localized heating, melting the filler metal without significantly heating the surrounding areas.
-
Advantages:
- Extremely fast and energy-efficient, as heat is generated only where needed.
- Provides precise control over the heating process, reducing the risk of thermal distortion.
- Suitable for joining small or delicate parts.
- Applications: Commonly used in the electronics, medical device, and automotive industries for components like connectors, valves, and sensors.
- Considerations: Requires specialized equipment and may not be cost-effective for large or complex assemblies.
In summary, torch brazing, furnace brazing, and induction brazing are three distinct methods of brazing, each with its own set of advantages and applications. Torch brazing is ideal for flexibility and small-scale jobs, furnace brazing excels in high-volume production with uniform heating, and induction brazing offers precision and efficiency for specialized applications. Understanding these methods allows equipment and consumable purchasers to select the most appropriate brazing technique for their specific needs.
Summary Table:
Brazing Method | Process | Advantages | Applications | Considerations |
---|---|---|---|---|
Torch Brazing | Uses a gas-fueled torch to heat filler metal and base metals. | Versatile, portable, precise heat control, cost-effective for small-scale jobs. | HVAC, plumbing, automotive repairs, jewelry making. | Requires skilled operators to avoid overheating or uneven heating. |
Furnace Brazing | Heats assembled parts and filler metal in a furnace for uniform heating. | High-volume production, controlled heating environment, suitable for complex assemblies. | Aerospace, automotive, electronics (e.g., heat exchangers, sensors, circuit boards). | Requires specialized equipment and controlled atmosphere (e.g., vacuum or inert gas). |
Induction Brazing | Uses electromagnetic induction to generate localized heat in the workpiece. | Fast, energy-efficient, precise control, ideal for small or delicate parts. | Electronics, medical devices, automotive (e.g., connectors, valves, sensors). | Requires specialized equipment; less cost-effective for large or complex assemblies. |
Need help choosing the right brazing method for your application? Contact our experts today for personalized advice!