Biomass pyrolysis is a thermochemical process that converts biomass into bio-oil, syngas, and biochar. Catalysts play a crucial role in enhancing the efficiency and selectivity of this process, improving the yield and quality of valuable products such as biofuels and chemicals. Various catalysts, including biochar-based catalysts, zeolites, clay minerals, titanium compounds, and metal nitrides, are used depending on the type of biomass, desired end products, and process conditions. These catalysts promote desirable chemical reactions, reduce impurities, and enhance the production of specific hydrocarbons and compounds like furfural.
Key Points Explained:
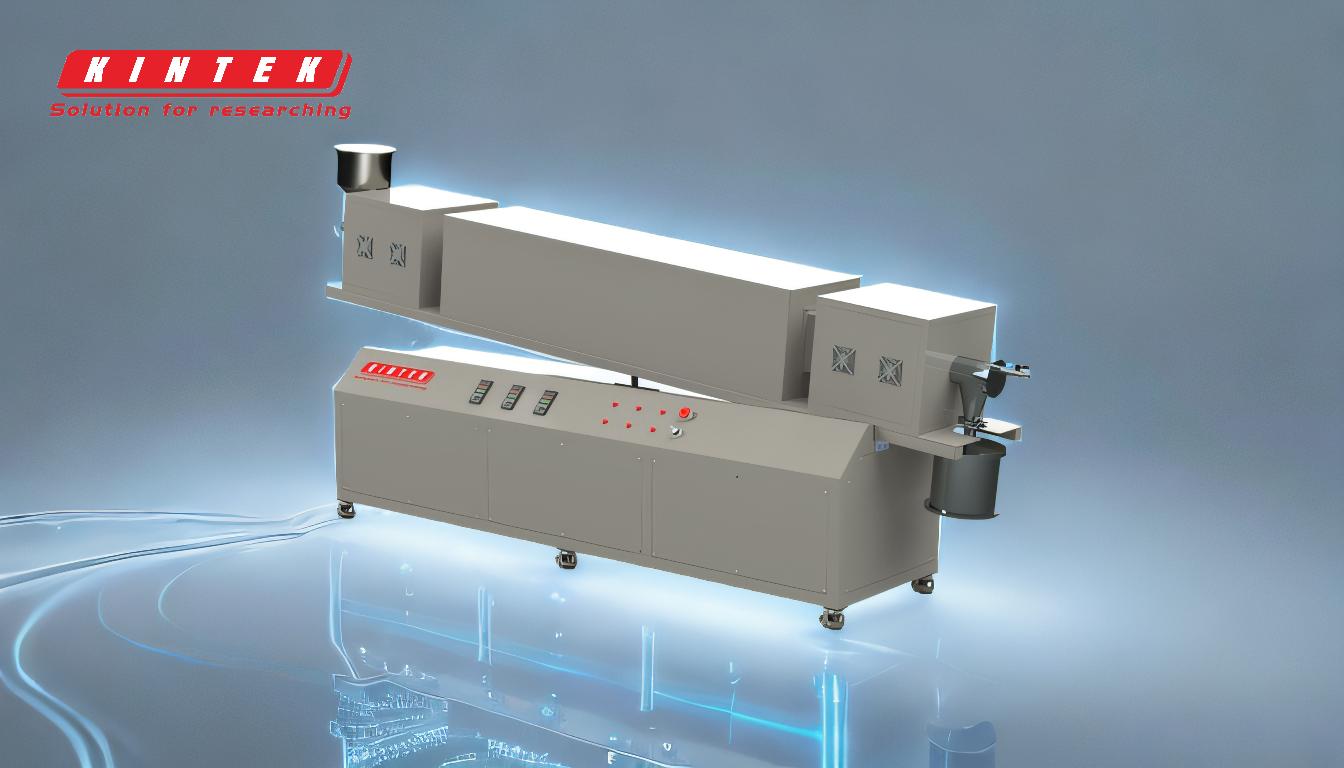
-
Biochar-Based Catalysts:
- Function: Promote desirable chemical reactions during pyrolysis, improving the yield of biofuels and chemicals.
- Benefits: Enhance the quality of bio-oil by reducing oxygenates, acids, and other impurities.
- Application: Suitable for a wide range of biomass types and process conditions.
-
Zeolites:
- Composition: Porous materials composed of aluminum and silicon oxides.
- Function: Selectively crack heavy hydrocarbons and condense light hydrocarbons.
- Benefits: Improve the yield of C1, C2, and C3 hydrocarbons.
- Application: Effective for producing specific hydrocarbons from biomass, depending on the desired end products and process conditions.
-
Clay Minerals (e.g., Kaolin):
- Function: Similar to zeolites, they selectively crack heavy hydrocarbons and condense light hydrocarbons.
- Benefits: Enhance the production of C1, C2, and C3 hydrocarbons.
- Application: Used in conjunction with or as an alternative to zeolites, depending on the biomass type and process requirements.
-
Titanium Compounds and Metal Nitrides (e.g., TiN, GaN):
- Function: Promote the production of furfural compounds during fast pyrolysis.
- Benefits: Specifically noted for enhancing furfural production, a valuable chemical intermediate.
- Application: Used in biomass fast pyrolysis processes aimed at furfural production.
-
Factors Influencing Catalyst Choice:
- Type of Biomass: Different biomass feedstocks may require different catalysts to optimize yield and product quality.
- Desired End Products: The choice of catalyst is influenced by the specific hydrocarbons or chemicals desired from the pyrolysis process.
- Process Conditions: Temperature, pressure, and reaction time can affect the performance of different catalysts, necessitating careful selection based on these parameters.
In summary, the selection of catalysts in biomass pyrolysis is critical for optimizing the process to produce high-quality biofuels and chemicals. Biochar-based catalysts, zeolites, clay minerals, and titanium compounds each offer unique benefits and are chosen based on the specific requirements of the biomass and desired end products. Understanding these catalysts and their applications can significantly enhance the efficiency and output of biomass pyrolysis processes.
Summary Table:
Catalyst Type | Function | Benefits | Application |
---|---|---|---|
Biochar-Based | Promotes desirable chemical reactions during pyrolysis | Enhances bio-oil quality by reducing impurities | Suitable for various biomass types and process conditions |
Zeolites | Selectively cracks heavy hydrocarbons and condenses light hydrocarbons | Improves yield of C1, C2, and C3 hydrocarbons | Effective for specific hydrocarbon production |
Clay Minerals (e.g., Kaolin) | Similar to zeolites, cracks heavy hydrocarbons and condenses light hydrocarbons | Enhances production of C1, C2, and C3 hydrocarbons | Used alongside or as an alternative to zeolites |
Titanium Compounds (e.g., TiN, GaN) | Promotes furfural production during fast pyrolysis | Specifically enhances furfural production | Ideal for fast pyrolysis processes targeting furfural |
Factors Influencing Choice | Depends on biomass type, desired end products, and process conditions | Optimizes yield and product quality based on specific requirements | Tailored to biomass feedstock and process parameters |
Ready to optimize your biomass pyrolysis process? Contact our experts today for tailored catalyst solutions!