Annealing is a heat treatment process that fundamentally alters the microstructure of a material, leading to changes in its mechanical and electrical properties. The process involves heating the material to a specific temperature, holding it at that temperature for a set duration, and then cooling it in a controlled manner. This process reduces hardness, increases ductility, relieves internal stresses, and improves workability. The key changes during annealing occur at the crystalline level, where defects are repaired, and a more uniform, homogeneous structure is formed. The slow cooling phase ensures the development of a ductile crystalline structure, making the material more suitable for further processing or use.
Key Points Explained:
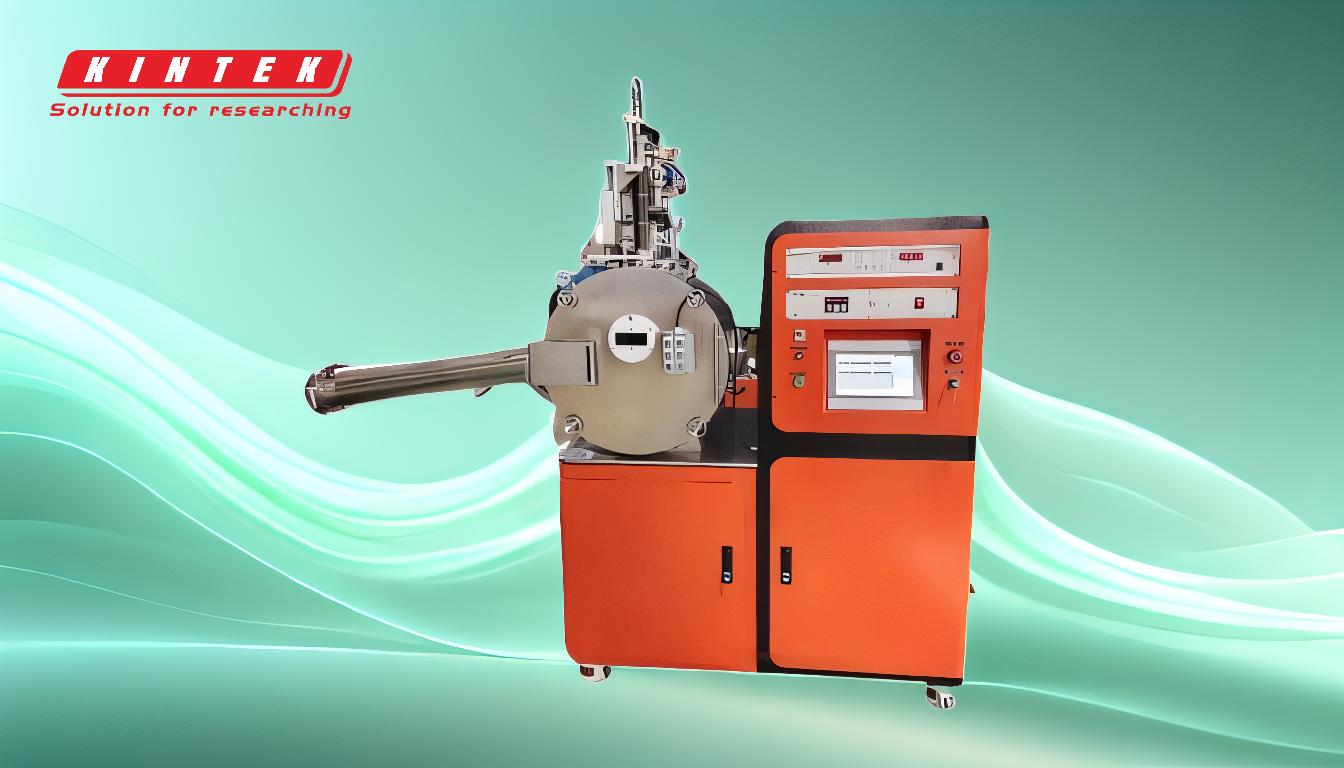
-
Microstructural Changes:
- Crystalline Structure: During annealing, the material is heated to a temperature where its crystalline structure becomes fluid-like, but the material remains solid. This allows for the rearrangement of atoms, repairing defects and creating a more uniform microstructure.
- Grain Refinement: The process can lead to the refinement of grain structures, which enhances the material's mechanical properties, such as toughness and fatigue resistance.
-
Mechanical Property Changes:
- Reduced Hardness: Annealing reduces the hardness of the material, making it less brittle and more malleable. This is particularly useful in metals like steel, where excessive hardness can lead to cracking under stress.
- Increased Ductility: By relieving internal stresses and allowing the material to cool slowly, annealing increases ductility. This makes the material easier to shape, bend, or stretch without breaking.
- Improved Workability: The overall workability of the material is enhanced, making it easier to machine, forge, or form into desired shapes.
-
Internal Stress Relief:
- Stress Reduction: Internal stresses, which can accumulate during manufacturing processes like casting, welding, or cold working, are relieved during annealing. This reduces the risk of material failure in service.
- Homogeneous Structure: The process promotes a more uniform internal structure, which is crucial for materials that need to perform consistently under various conditions.
-
Electrical Property Changes:
- Conductivity: In some materials, annealing can improve electrical conductivity by reducing defects and impurities in the crystalline structure. This is particularly important in materials used in electrical applications.
- Magnetic Properties: For magnetic materials, annealing can enhance magnetic properties by aligning the crystalline structure in a way that improves magnetic permeability.
-
Process Parameters:
- Temperature Control: The temperature at which annealing occurs is critical. It must be above the material's recrystallization temperature but below its melting point to ensure proper microstructural changes.
- Time at Temperature: The duration the material is held at the annealing temperature is also important. It must be sufficient to allow for the desired microstructural changes but not so long as to cause excessive grain growth or other undesirable effects.
- Cooling Rate: The cooling rate is carefully controlled to ensure that the material develops the desired properties. Slow cooling is typically used to promote ductility and reduce internal stresses.
-
Applications of Annealing:
- Steel Industry: Annealing is widely used in the steel industry to improve the machinability and formability of steel products. It is also used to prepare steel for further heat treatments.
- Electronics: In the electronics industry, annealing is used to improve the electrical properties of materials used in semiconductors and other electronic components.
- Manufacturing: Annealing is employed in various manufacturing processes to enhance the properties of metals and alloys, making them more suitable for specific applications.
In summary, the annealing process brings about significant changes in the material's microstructure, mechanical properties, and electrical properties. By carefully controlling the temperature, time, and cooling rate, the process can be tailored to achieve specific desired outcomes, making it a versatile and essential heat treatment method in various industries.
Summary Table:
Key Aspect | Description |
---|---|
Microstructural Changes | Repairs defects, refines grain structure, and creates a uniform microstructure. |
Mechanical Properties | Reduces hardness, increases ductility, and improves workability. |
Internal Stress Relief | Relieves internal stresses and promotes a homogeneous structure. |
Electrical Properties | Enhances conductivity and magnetic properties in certain materials. |
Process Parameters | Controlled temperature, time, and cooling rate ensure desired outcomes. |
Applications | Widely used in steel, electronics, and manufacturing industries. |
Discover how annealing can optimize your materials—contact our experts today!