CVD coating stands for Chemical Vapor Deposition coating, a surface treatment process that involves the deposition of thin films onto various materials through thermally induced chemical reactions. This process occurs in a controlled environment, typically a vacuum chamber, where reactive gases are introduced and react or break down at elevated temperatures to form a durable and high-performance coating that bonds to the substrate's surface. CVD coatings are widely used in applications requiring high durability, such as machine tools, analytical flow path components, wear components, and instrumentation. The process is environmentally friendly and known for producing coatings with excellent adhesion and uniformity.
Key Points Explained:
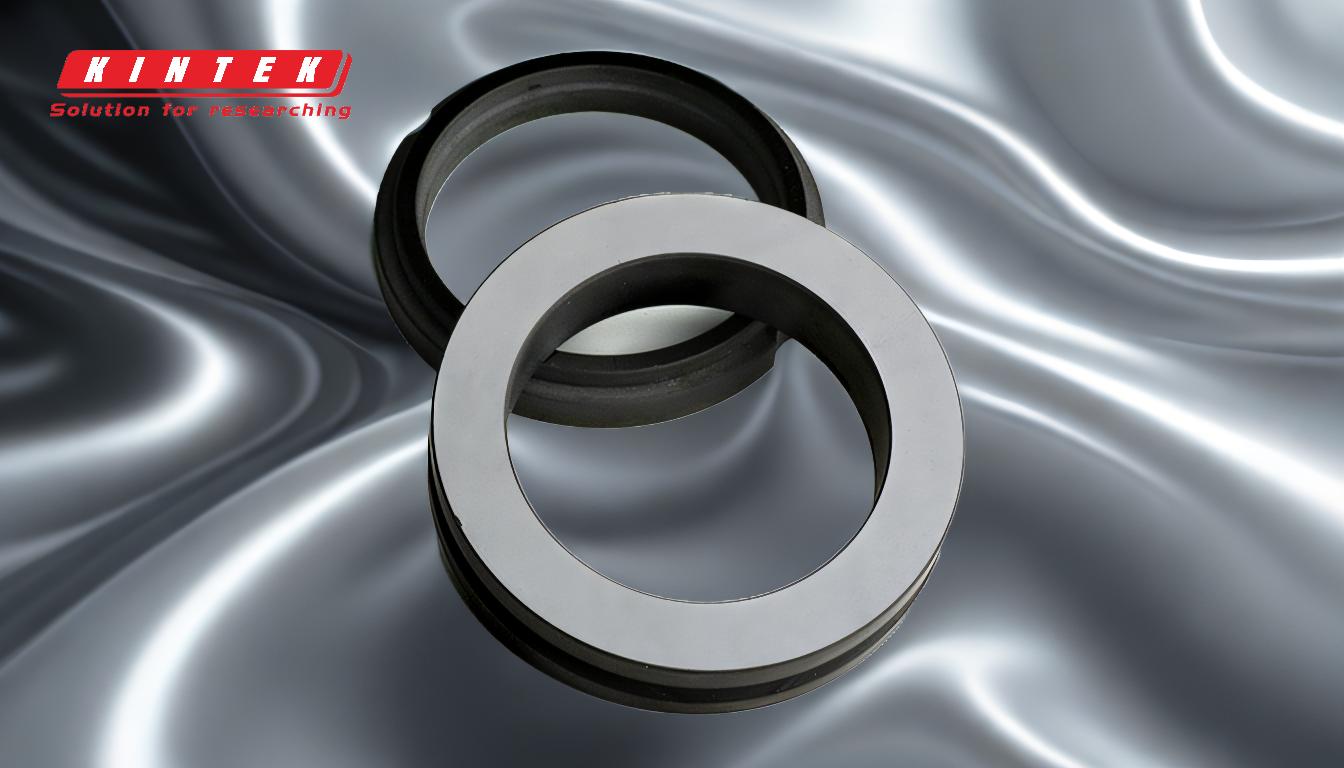
-
Definition of CVD Coating
- CVD stands for Chemical Vapor Deposition, a process used to apply thin films or coatings to surfaces.
- It involves chemical reactions in a controlled environment, typically a vacuum chamber, where reactive gases are introduced and react or decompose at high temperatures to form a coating.
-
Process Mechanism
- The process begins with the introduction of a volatile precursor gas into a chamber.
- The substrate (material to be coated) is heated to a specific reaction temperature.
- The precursor gas reacts or breaks down, depositing a thin film onto the substrate's surface.
- The coating bonds to the substrate, forming a durable and uniform layer.
-
Key Characteristics of CVD Coatings
- Durability: CVD coatings are known for their high resistance to wear, corrosion, and other forms of degradation.
- Adhesion: The coatings bond strongly to the substrate, ensuring long-lasting performance.
- Uniformity: The process allows for precise control over the thickness and composition of the coating.
- Environmental Friendliness: CVD is a clean process that produces minimal waste, making it environmentally sustainable.
-
Applications of CVD Coatings
- Machine Tools: Used to enhance the durability and performance of cutting and forming tools.
- Analytical Flow Path Components: Applied to components in analytical instruments to improve resistance to chemical corrosion and wear.
- Wear Components: Used in industries where components are subjected to high friction and wear, such as automotive and aerospace.
- Instrumentation: Applied to improve the performance and lifespan of precision instruments.
-
Advantages of CVD Coatings
- High Performance: Suitable for demanding applications due to their durability and resistance to harsh conditions.
- Versatility: Can be applied to a wide range of materials, including metals, ceramics, and composites.
- Precision: Allows for the deposition of coatings with precise thickness and composition.
- Sustainability: Environmentally friendly process with minimal waste generation.
-
Comparison with Other Coating Methods
- Physical Vapor Deposition (PVD): Unlike PVD, which involves physical processes like sputtering or evaporation, CVD relies on chemical reactions, resulting in better adhesion and uniformity.
- Electroplating: CVD does not require an electrolyte solution, making it cleaner and more suitable for complex geometries.
- Thermal Spraying: CVD produces thinner and more uniform coatings compared to thermal spraying, which can result in thicker and less precise layers.
-
Considerations for Equipment and Consumable Purchasers
- Compatibility: Ensure the CVD process is compatible with the substrate material and intended application.
- Cost: Evaluate the cost-effectiveness of CVD compared to other coating methods, considering factors like durability and performance.
- Environmental Impact: Consider the sustainability of the process and its alignment with environmental regulations.
- Supplier Expertise: Choose suppliers with proven expertise in CVD technology to ensure high-quality coatings and reliable service.
By understanding the principles, advantages, and applications of CVD coatings, purchasers can make informed decisions about selecting the right coating method for their specific needs.
Summary Table:
Aspect | Details |
---|---|
Definition | Chemical Vapor Deposition (CVD) applies thin films via chemical reactions. |
Process | Reactive gases deposit coatings in a vacuum chamber at high temperatures. |
Key Characteristics | Durable, strong adhesion, uniform, and environmentally friendly. |
Applications | Machine tools, analytical components, wear parts, and precision instruments. |
Advantages | High performance, versatility, precision, and sustainability. |
Comparison | Better adhesion and uniformity than PVD; cleaner than electroplating. |
Considerations | Compatibility, cost, environmental impact, and supplier expertise. |
Ready to enhance your materials with CVD coatings? Contact us today for expert guidance!