Sintering metals is a process that involves compacting and bonding metal powders into a solid mass using heat and pressure without reaching the melting point of the material. This method is widely used in manufacturing to create strong, durable components with precise shapes and properties. The process typically involves blending metal powders, pressing them into a desired shape, and then heating them in a controlled environment to fuse the particles together. The result is a dense, cohesive material with improved mechanical properties. Sintering is particularly useful for materials with high melting points, such as tungsten and molybdenum, and is a key step in powder metallurgy.
Key Points Explained:
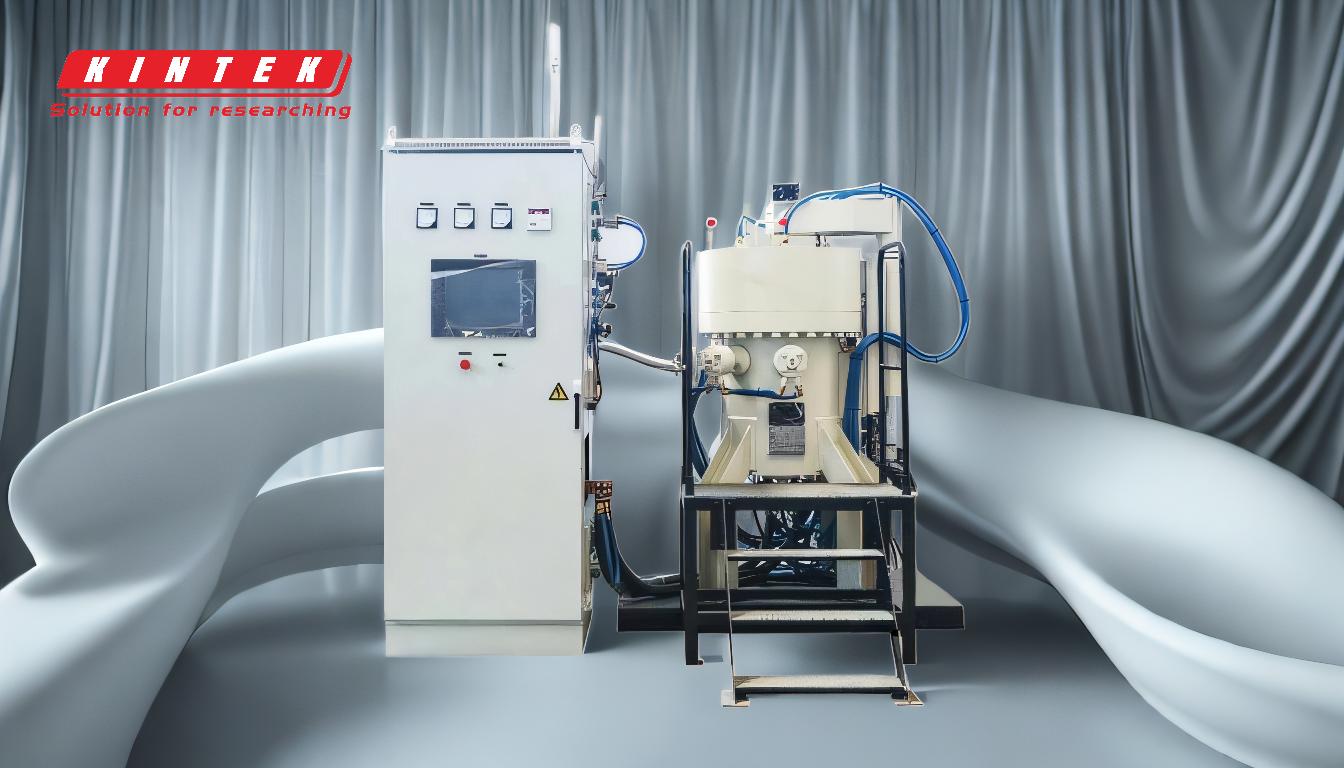
-
Definition of Sintering:
- Sintering is a process that bonds particles together into a solid mass using heat and/or pressure without melting the material. It is commonly used for metals, ceramics, and plastics.
- The process involves the diffusion of atoms across particle boundaries, which fuses the particles together, reducing porosity and creating a dense, solid structure.
-
Stages of the Sintering Process:
- Blending: Metal powders are mixed with a bonding agent (such as water, wax, or polymer) to form a uniform mixture. This mixture is then pressed into the desired shape.
- Debinding: The shaped part, known as the "green part," is heated to remove the bonding agent, which evaporates or burns away.
- Sintering: The temperature is increased to a point where the metal particles begin to fuse at their surfaces. This stage may involve the use of an intermediate bonding agent, such as bronze, which melts and bonds the particles without altering the primary metal powder.
-
Applications in Metal Manufacturing:
- In steel production, sintering is used to create lumps of iron from powdered iron ore mixed with coke. These lumps are then used in blast furnaces to produce steel.
- The process is also used in powder metallurgy to manufacture complex metal parts with high precision and strength.
-
Role of the Sintering Furnace:
- A sintering furnace is essential for the sintering process. It provides the controlled environment needed to apply heat and pressure to the metal powders.
- The furnace typically consists of a heating element, a pressure system, and a vacuum or controlled atmosphere to prevent oxidation and ensure proper bonding of the particles.
-
Microstructural Changes:
- Sintering directly affects the microstructure of the material, including grain size, pore size, and grain boundary distribution. These changes influence the material's mechanical properties, such as strength, durability, and resistance to wear.
-
Advantages of Sintering:
- Cost-Effective: Sintering allows for the production of complex shapes with minimal material waste.
- Material Efficiency: The process can utilize metal powders that might otherwise be difficult to work with using traditional methods.
- Enhanced Properties: Sintered materials often exhibit improved mechanical properties, such as higher strength and better wear resistance, due to the controlled microstructure.
-
Challenges and Considerations:
- Temperature Control: Precise temperature control is crucial to avoid melting the material while ensuring proper bonding.
- Atmosphere Control: Maintaining a controlled atmosphere (e.g., vacuum or inert gas) is necessary to prevent oxidation and contamination.
- Post-Processing: Some sintered parts may require additional processing, such as machining or heat treatment, to achieve the desired final properties.
By understanding these key points, one can appreciate the complexity and importance of the sintering process in modern manufacturing, particularly in the production of high-performance metal components.
Summary Table:
Aspect | Details |
---|---|
Definition | Bonds metal powders into a solid mass using heat/pressure without melting. |
Stages | Blending, debinding, and sintering. |
Applications | Steel production, powder metallurgy, and high-precision metal parts. |
Key Equipment | Sintering furnace with controlled atmosphere and heating elements. |
Advantages | Cost-effective, material-efficient, and enhances mechanical properties. |
Challenges | Precise temperature control, atmosphere control, and post-processing needs. |
Discover how sintering can optimize your manufacturing process—contact our experts today!