Heat treatment of steel is a critical process used to alter the physical and sometimes chemical properties of the material to achieve desired characteristics such as hardness, toughness, ductility, and strength. The equipment used for heat treatment varies depending on the specific process and the scale of operation. Common equipment includes furnaces, quenching systems, and tempering units. Each type of equipment is designed to control temperature, heating rate, and cooling rate precisely to ensure the steel achieves the desired properties. Below, we will explore the key equipment used in the heat treatment of steel, their functions, and how they contribute to the overall process.
Key Points Explained:
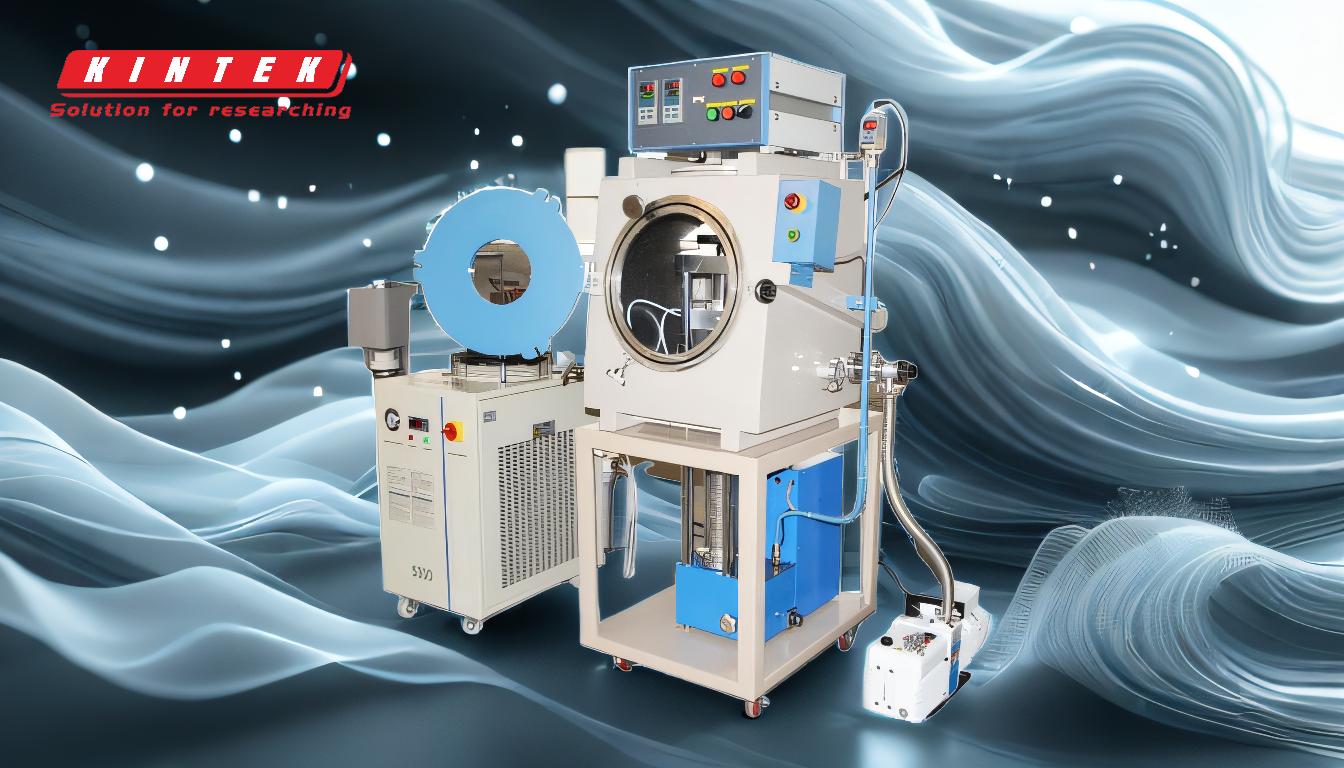
-
Furnaces:
- Types: The most common types of furnaces used in steel heat treatment include box furnaces, pit furnaces, and continuous furnaces.
- Function: Furnaces are used to heat the steel to a specific temperature where the desired metallurgical transformations can occur. The temperature and heating rate are carefully controlled to ensure uniformity and prevent defects.
- Applications: Box furnaces are typically used for batch processing, while continuous furnaces are used for high-volume production. Pit furnaces are often used for large or heavy components.
-
Quenching Systems:
- Types: Quenching can be done using oil, water, polymer solutions, or air, depending on the required cooling rate and the type of steel.
- Function: Quenching rapidly cools the steel to lock in the desired microstructure, such as martensite, which is crucial for achieving high hardness.
- Equipment: Quenching tanks, spray systems, and air blowers are commonly used. The choice of quenching medium and equipment depends on the steel grade and the required properties.
-
Tempering Equipment:
- Types: Tempering is often done in furnaces similar to those used for heating, but at lower temperatures.
- Function: Tempering reduces the brittleness of the steel after quenching by allowing some of the martensite to transform into softer phases like tempered martensite.
- Temperature Control: Precise temperature control is essential during tempering to achieve the desired balance between hardness and toughness.
-
Atmosphere Control Systems:
- Types: These systems include gas purging, vacuum furnaces, and controlled atmosphere furnaces.
- Function: Atmosphere control prevents oxidation and decarburization of the steel surface during heating. This is particularly important for high-quality steel products.
- Applications: Vacuum furnaces are used for high-precision components, while controlled atmosphere furnaces are common in general heat treatment processes.
-
Annealing Equipment:
- Types: Batch and continuous annealing furnaces.
- Function: Annealing is used to soften the steel, improve machinability, and relieve internal stresses. The process involves heating the steel to a specific temperature and then cooling it slowly.
- Cooling Methods: Slow cooling can be achieved in the furnace itself or by transferring the steel to an insulated chamber.
-
Induction Heating Systems:
- Types: Induction heaters can be designed for localized or bulk heating.
- Function: Induction heating is used for surface hardening or selective heat treatment. It heats the steel quickly and precisely using electromagnetic induction.
- Advantages: This method is energy-efficient and allows for precise control over the heated area, making it ideal for complex geometries.
-
Cooling Systems:
- Types: Air cooling, water cooling, and oil cooling systems.
- Function: Cooling systems are used after heating or quenching to control the cooling rate and achieve the desired microstructure.
- Importance: The cooling rate is critical in determining the final properties of the steel, such as hardness and toughness.
-
Temperature Monitoring and Control Systems:
- Types: Thermocouples, pyrometers, and digital controllers.
- Function: These systems ensure that the steel is heated and cooled at the correct rates and to the precise temperatures required for the specific heat treatment process.
- Importance: Accurate temperature control is essential to avoid defects such as warping, cracking, or uneven hardness.
Each piece of equipment plays a vital role in the heat treatment process, and the choice of equipment depends on the specific requirements of the steel being treated, the desired properties, and the scale of production. Understanding the function and application of each type of equipment is crucial for achieving consistent and high-quality results in steel heat treatment.
Summary Table:
Equipment | Types | Function |
---|---|---|
Furnaces | Box, Pit, Continuous | Heat steel to specific temperatures for metallurgical transformations. |
Quenching Systems | Oil, Water, Polymer, Air | Rapidly cool steel to lock in desired microstructures like martensite. |
Tempering Equipment | Low-temperature furnaces | Reduce brittleness after quenching by transforming martensite into softer phases. |
Atmosphere Control | Gas purging, Vacuum, Controlled atmosphere furnaces | Prevent oxidation and decarburization during heating. |
Annealing Equipment | Batch, Continuous furnaces | Soften steel, improve machinability, and relieve internal stresses. |
Induction Heating | Localized or bulk heating systems | Surface hardening or selective heat treatment using electromagnetic induction. |
Cooling Systems | Air, Water, Oil cooling | Control cooling rate to achieve desired microstructure. |
Temperature Monitoring | Thermocouples, Pyrometers, Digital controllers | Ensure precise heating and cooling rates for consistent results. |
Ready to optimize your steel heat treatment process? Contact our experts today for tailored solutions!