After sintering, the material undergoes significant microstructural changes that directly influence its physical and mechanical properties. The process results in the fusion of particles, reduction of porosity, and formation of a dense, solid structure. These changes enhance properties such as strength, durability, thermal conductivity, and electrical conductivity. The final product may also exhibit improved translucency, depending on the material and sintering conditions. The outcome is a material with tailored properties suitable for specific applications, achieved through careful control of the sintering process parameters.
Key Points Explained:
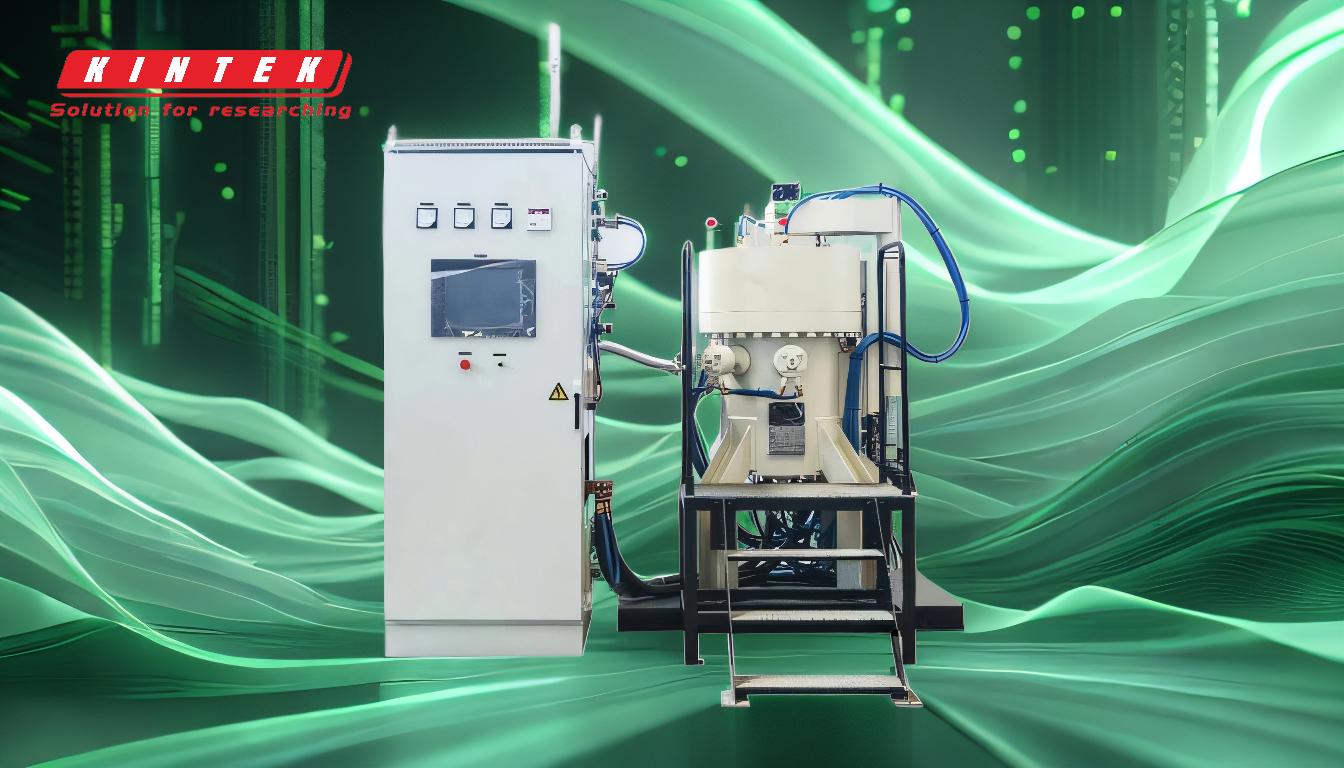
-
Microstructural Changes:
- Grain Size and Growth: Sintering leads to the growth of grains within the material. As particles fuse together, the boundaries between them disappear, leading to larger grain sizes. This grain growth can affect the material's mechanical properties, such as strength and toughness.
- Pore Size and Distribution: The sintering process reduces the porosity of the material by closing pores and eliminating voids. This densification improves the material's density and can enhance properties like strength and thermal conductivity.
- Grain Boundary Shape and Distribution: The shape and distribution of grain boundaries are altered during sintering. These changes can influence the material's resistance to deformation and its overall durability.
-
Physical and Chemical Changes:
- Evaporation of Volatile Components: During sintering, any water, organic matter, or adsorbed gases are removed from the material. This purification process is crucial for achieving a dense and homogeneous final product.
- Reduction of Surface Oxides: Surface oxides on powder particles are reduced, which facilitates better bonding between particles and improves the material's overall integrity.
- Material Migration and Recrystallization: Atoms migrate across particle boundaries, leading to recrystallization and the formation of new crystalline structures. This process contributes to the material's densification and strength.
-
Enhancement of Material Properties:
- Strength and Durability: The reduction in porosity and the formation of a dense microstructure significantly enhance the material's strength and durability. This makes the sintered material suitable for applications requiring high mechanical performance.
- Thermal and Electrical Conductivity: The densification process improves the material's thermal and electrical conductivity by reducing the number of insulating voids and enhancing the connectivity between grains.
- Translucency: In some materials, sintering can lead to increased translucency, which is desirable in applications such as dental ceramics or optical components.
-
Final Stage of Sintering:
- Binding of Remaining Pores: In the final stage of sintering, any remaining open cracks or pores are filled with liquid or binder additives. This ensures that the material is fully dense and free from defects, resulting in a high-quality final product.
- Formation of a Solid Mass: The material becomes mostly solid, with a uniform microstructure that exhibits the desired properties for its intended application.
-
Applications and Implications:
- Tailored Material Properties: By controlling the sintering process parameters, manufacturers can tailor the properties of the material to meet specific application requirements. This includes adjusting the temperature, pressure, and duration of sintering to achieve the desired microstructure and properties.
- Versatility in Applications: Sintered materials are used in a wide range of industries, including automotive, aerospace, electronics, and medical devices. The enhanced properties achieved through sintering make these materials ideal for high-performance applications.
In summary, the post-sintering phase is characterized by significant microstructural changes that enhance the material's physical and mechanical properties. The process results in a dense, solid structure with improved strength, durability, and conductivity, making it suitable for a variety of high-performance applications.
Summary Table:
Key Changes | Impact on Material Properties |
---|---|
Grain Size and Growth | Larger grains improve strength and toughness. |
Pore Size and Distribution | Reduced porosity enhances density, strength, and thermal/electrical conductivity. |
Grain Boundary Changes | Altered boundaries improve durability and resistance to deformation. |
Evaporation of Volatiles | Removes impurities, ensuring a dense and homogeneous structure. |
Recrystallization | Forms new crystalline structures, boosting densification and strength. |
Translucency | Increases in some materials, ideal for dental ceramics or optical components. |
Final Densification | Binds remaining pores, creating a defect-free, solid mass with tailored properties. |
Unlock the potential of sintered materials for your applications—contact our experts today!