When a ceramic material is sintered, it undergoes a transformative process where the powder particles are heated to high temperatures below their melting point, causing them to bond and densify. This process reduces porosity, enhances mechanical properties like strength and durability, and often alters the material's crystalline structure. Sintering can also improve resistance to environmental factors such as extreme temperatures, water, and UV rays. Advanced methods like microwave sintering further optimize the process by enabling rapid, low-temperature sintering, resulting in denser and more uniform microstructures. However, challenges like warping or sagging can occur, potentially leading to defects in the final product.
Key Points Explained:
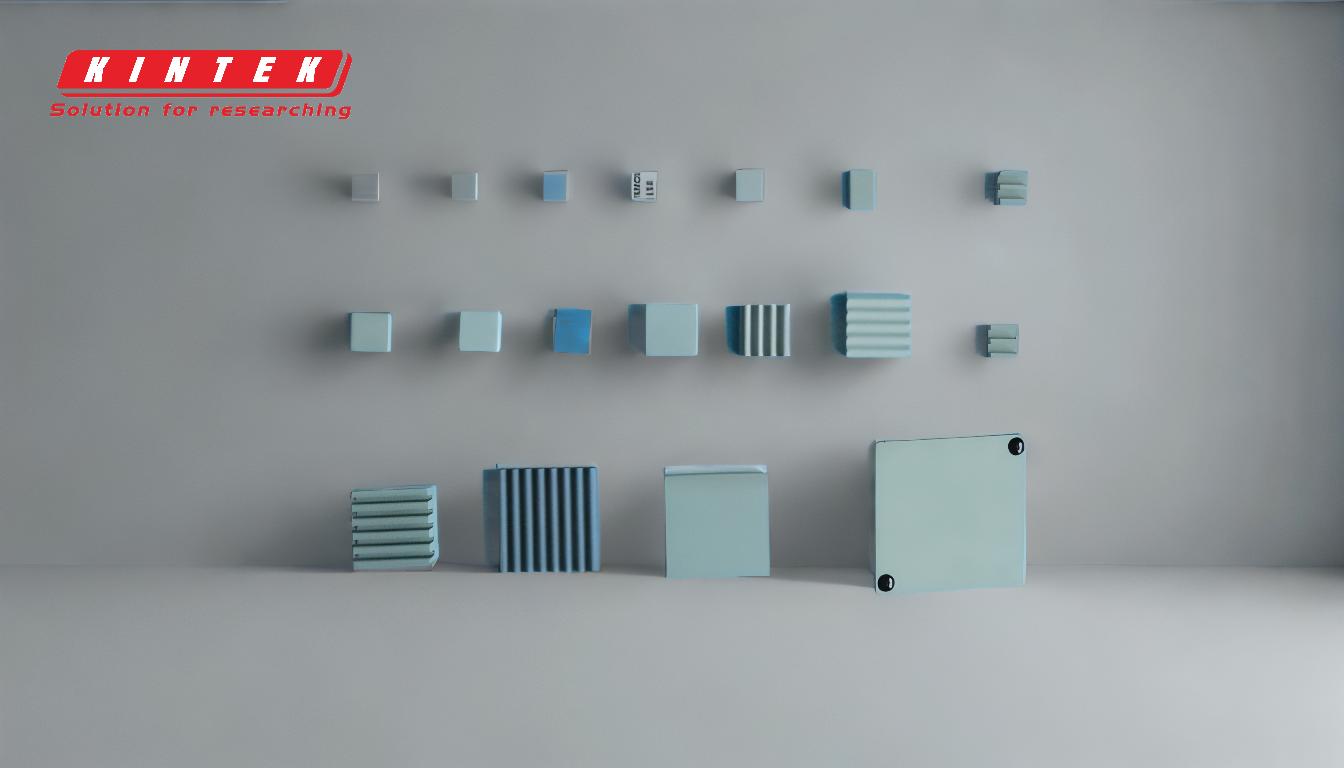
-
Definition and Purpose of Sintering:
- Sintering, also known as firing, involves heating ceramic powder particles to a high temperature below their melting point. This process consolidates the particles, reducing porosity and increasing density, which enhances the material's mechanical and functional properties.
-
Material Transformation:
- During sintering, material from individual particles diffuses to neighboring particles, leading to bonding and densification. For example, zirconia transforms from a monoclinic to a polytetragonal crystalline structure, becoming extremely hard and dense.
-
Porosity Reduction and Densification:
- The pores in the "green compact" (the initial molded ceramic part) diminish or close up during sintering. This densification improves the material's strength, durability, and resistance to environmental factors like water, stains, and UV rays.
-
Enhanced Properties:
- Sintered ceramics are highly durable, scratch-resistant, and capable of withstanding extreme temperatures and weather conditions. They are also waterproof, graffiti-proof, and resistant to high-traffic abrasion.
-
Advanced Sintering Techniques:
- Microwave sintering is an advanced method that allows for low-temperature and rapid sintering. This technique reduces grain growth and residual pores, resulting in denser and more uniform microstructures, which further enhance the material's strength and durability.
-
Challenges in Sintering:
- Issues such as warping due to gravity or friction, and sagging of parts, can occur during sintering. These defects can compromise the final product's quality, necessitating careful control of the sintering process.
-
Application in Ceramic Heating Elements:
- Sintering is particularly important for ceramic heating elements, as it enhances their thermal and mechanical properties, making them suitable for high-temperature applications.
-
Environmental and Industrial Applications:
- The durability and resistance of sintered ceramics make them ideal for use in harsh environments, including industrial settings, construction, and outdoor applications where exposure to extreme conditions is common.
By understanding these key points, a purchaser of ceramic materials or equipment can make informed decisions about the suitability of sintered ceramics for their specific needs, ensuring optimal performance and longevity.
Summary Table:
Aspect | Details |
---|---|
Definition | Heating ceramic particles below melting point to bond and densify. |
Porosity Reduction | Pores diminish, increasing density and strength. |
Enhanced Properties | Scratch-resistant, waterproof, and durable under extreme conditions. |
Advanced Techniques | Microwave sintering enables rapid, low-temperature densification. |
Challenges | Warping or sagging may occur, requiring precise process control. |
Applications | Ideal for industrial, construction, and high-temperature environments. |
Interested in sintered ceramics for your applications? Contact us today to learn more!