Brazing is a versatile and widely used metal-joining technique that involves melting a filler metal (typically brass) between adjacent surfaces of metal parts to create a strong, durable bond. This process requires high temperatures, often referred to as "red heat," and the use of flux to prevent oxidation of the metal surfaces. Brazing is employed in various industries due to its ability to join dissimilar metals, create leak-proof seals, and produce robust connections without significantly altering the base materials. Common applications include metal housings, electromechanical components, pipe fittings, automotive engine components, and HVAC system components.
Key Points Explained:
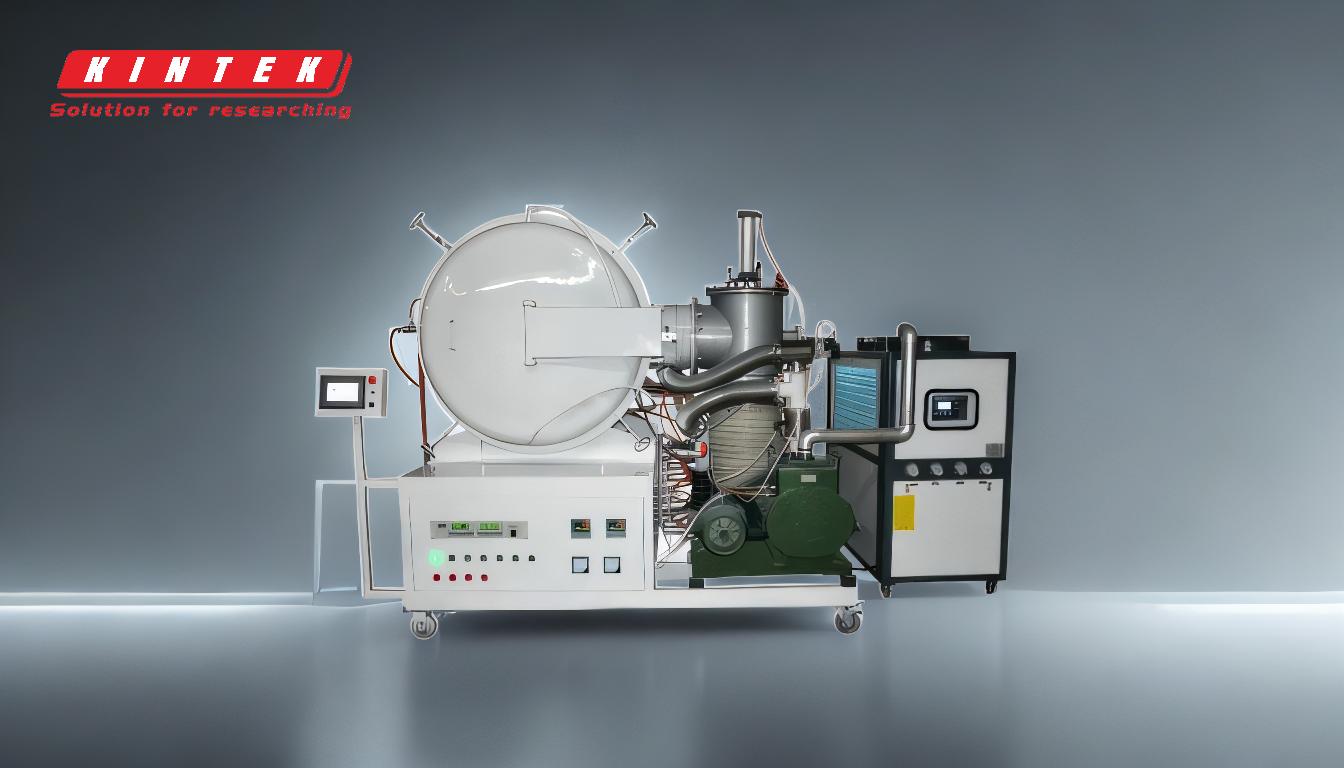
-
What is Brazing?
- Brazing is a metal-joining process that uses a filler metal with a lower melting point than the base metals being joined. The filler metal, often brass, is melted and flows into the joint by capillary action, creating a strong bond upon cooling. This process typically occurs at temperatures above 840°F (450°C), known as "red heat," but below the melting point of the base metals.
-
Key Components of Brazing
- Filler Metal: The filler metal is the material that melts and flows into the joint. Brass is a common choice due to its compatibility with many base metals and its ability to form strong, corrosion-resistant bonds.
- Flux: Flux is a chemical cleaning agent used to prevent oxidation of the metal surfaces during heating. It ensures that the filler metal adheres properly to the base metals.
- Heat Source: Brazing requires a controlled heat source, such as a torch, furnace, or induction heater, to achieve the necessary temperatures for melting the filler metal.
-
Advantages of Brazing
- Joining Dissimilar Metals: Brazing can join metals with different compositions, such as copper to steel or aluminum to stainless steel, which is often challenging with other welding methods.
- Leak-Proof Seals: The capillary action of the filler metal creates tight, leak-proof joints, making brazing ideal for applications like plumbing and HVAC systems.
- Minimal Distortion: Since the base metals do not melt, brazing causes minimal distortion or warping, preserving the integrity of the components.
- Strength and Durability: Brazed joints are strong and resistant to vibration and thermal cycling, making them suitable for demanding applications like automotive and aerospace components.
-
Common Applications of Brazing
- Metal Housings: Brazing is used to assemble metal enclosures and housings for electronics, machinery, and other equipment, ensuring durability and protection.
- Electromechanical Components: It is widely used in the production of electrical contacts, connectors, and sensors, where reliable electrical and mechanical connections are critical.
- Pipe Fittings: Brazing is a preferred method for joining pipes and fittings in plumbing, refrigeration, and gas systems due to its ability to create leak-proof seals.
- Automotive Engine Components: In the automotive industry, brazing is used to join critical components like radiators, heat exchangers, and exhaust systems, which must withstand high temperatures and mechanical stress.
- HVAC System Components: Heating, ventilation, and air conditioning systems rely on brazing to assemble heat exchangers, coils, and other components that require efficient heat transfer and airtight seals.
-
Process Considerations
- Surface Preparation: Proper cleaning and preparation of the metal surfaces are essential to ensure a strong bond. Contaminants like oil, grease, or oxide layers must be removed before brazing.
- Joint Design: The design of the joint plays a crucial role in the success of brazing. Joints should be designed to allow capillary action to draw the filler metal into the gap between the base metals.
- Temperature Control: Precise control of the heating process is necessary to avoid overheating the base metals or insufficiently melting the filler metal.
-
Comparison with Other Joining Methods
- Brazing vs. Welding: Unlike welding, which melts the base metals to form a joint, brazing only melts the filler metal. This makes brazing suitable for joining dissimilar metals and reduces the risk of warping or distortion.
- Brazing vs. Soldering: Soldering operates at lower temperatures than brazing and uses a different type of filler metal. Brazing is generally stronger and more suitable for high-stress applications.
In summary, brazing is a highly effective and versatile method for joining metal parts, offering numerous advantages such as the ability to join dissimilar metals, create leak-proof seals, and produce strong, durable connections. Its applications span a wide range of industries, from automotive and HVAC to electronics and plumbing, making it an indispensable technique in modern manufacturing and repair processes.
Summary Table:
Key Aspect | Details |
---|---|
Process | Joins metals using a filler metal (e.g., brass) at high temperatures. |
Key Components | Filler metal, flux, and controlled heat source (torch, furnace, etc.). |
Advantages | Joins dissimilar metals, creates leak-proof seals, minimal distortion. |
Applications | Automotive, HVAC, electronics, plumbing, and more. |
Comparison | Stronger than soldering, less distortion than welding. |
Interested in how brazing can enhance your projects? Contact our experts today for tailored solutions!