A controlled atmosphere furnace is a specialized heating device designed to provide precise temperature and atmospheric conditions for various laboratory and industrial processes. It is particularly useful when larger chamber volumes are needed, and deep vacuum conditions are not essential. These furnaces can operate under vacuum conditions as low as 1 Torr and can also handle inert and reactive gases, making them versatile for heat treatment, sintering, annealing, and other processes. They are widely used in industries and academic settings for tasks such as chemical vapor deposition, graphitization, and material sintering, ensuring precise control over environmental conditions for successful project outcomes.
Key Points Explained:
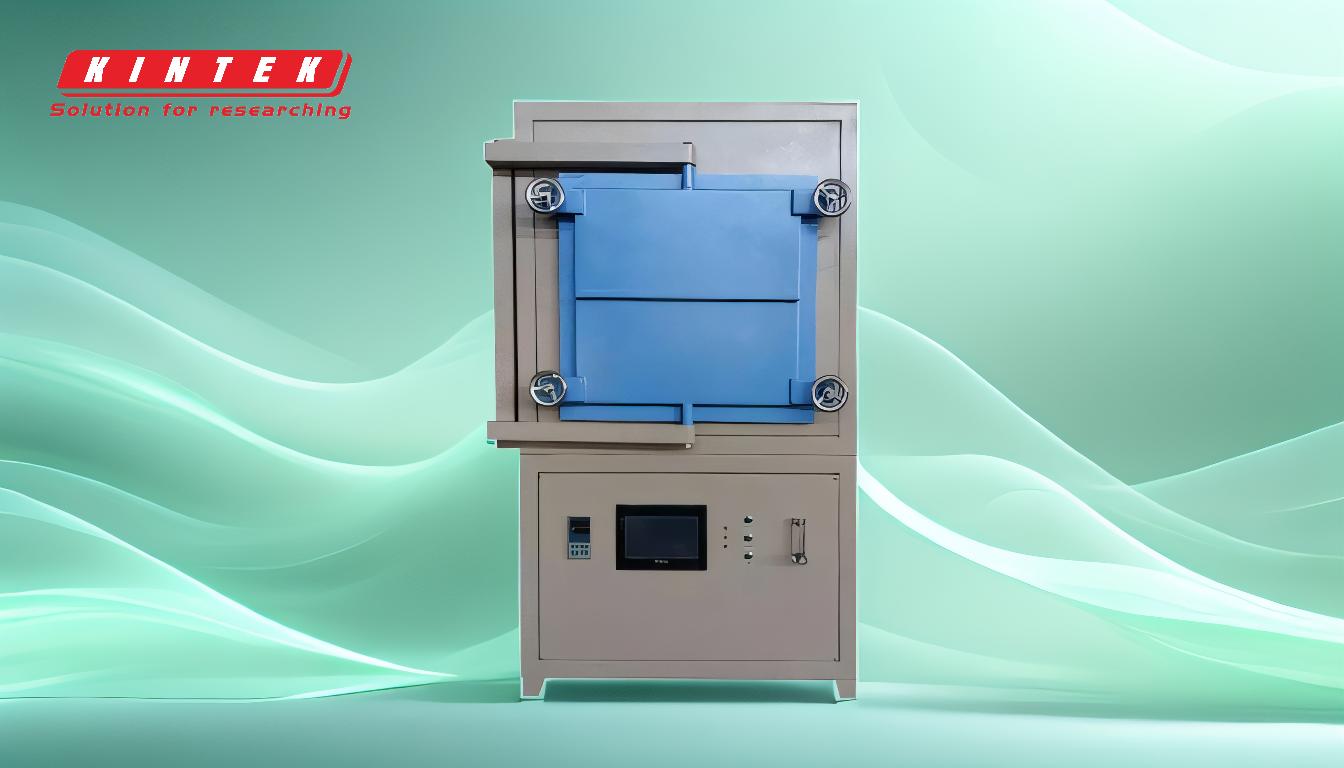
-
Definition and Purpose:
- A controlled atmosphere furnace is a heating device that provides a tightly sealed environment with controlled temperature and atmospheric conditions.
- It is used for various heat treatment experiments and processes, ensuring precise control over environmental factors to achieve desired outcomes.
-
Key Features:
- Vacuum Capability: Can maintain a vacuum down to 1 Torr, which is suitable for processes that require low-pressure environments.
- Gas Compatibility: Can operate with both inert gases (e.g., argon, nitrogen) and reactive gases (e.g., hydrogen), making it versatile for different applications.
- Temperature Control: Offers precise temperature regulation, which is critical for processes like annealing, sintering, and heat treatment.
-
Applications:
- Heat Treatment: Used for processes such as annealing, hardening, tempering, and nitriding.
- Material Processing: Suitable for sintering, graphitization, and purification of materials like metals and ceramics.
- Chemical Processes: Employed in chemical vapor deposition (CVD) and chemical vapor infiltration (CVI).
- Laboratory Use: Ideal for academic and industrial laboratories for tasks like chemical analysis, physical measurements, and small-scale material processing.
-
Advantages Over Tube Furnaces:
- Larger Chamber Volume: Better suited for applications requiring larger sample sizes or batch processing.
- Versatility: Can handle a wider range of atmospheric conditions compared to tube furnaces, which are typically limited to smaller volumes and specific gas environments.
-
Industrial and Academic Use:
- Widely used in industries for processes like brazing, soldering, and specialist welding.
- Commonly found in universities and research institutions for experiments requiring controlled environments, such as material sintering and heat treatment of small steel parts.
-
Sealed Environment:
- The furnace maintains a tightly sealed environment to prevent contamination and ensure consistent atmospheric conditions, which is crucial for the success of sensitive experiments and processes.
-
Precision and Reliability:
- Ensures tasks are completed with exact temperatures and atmospheric conditions, minimizing errors and guaranteeing the successful outcome of projects.
In summary, a controlled atmosphere furnace is a versatile and essential tool for processes requiring precise temperature and atmospheric control. Its ability to handle various gases and maintain low-pressure environments makes it indispensable in both industrial and academic settings for a wide range of applications.
Summary Table:
Feature | Description |
---|---|
Vacuum Capability | Operates under vacuum down to 1 Torr for low-pressure environments. |
Gas Compatibility | Works with inert (argon, nitrogen) and reactive (hydrogen) gases. |
Temperature Control | Precise regulation for annealing, sintering, and heat treatment. |
Applications | Heat treatment, material processing, chemical vapor deposition, lab experiments. |
Advantages | Larger chamber volume, versatile atmospheric handling, sealed environment. |
Ready to enhance your lab or industrial processes? Contact us today to learn more about controlled atmosphere furnaces!