A CVD (Chemical Vapor Deposition) furnace is a specialized type of furnace used to deposit thin layers of material onto a substrate through a chemical vapor deposition process. This process involves the reaction of gaseous precursors at high temperatures to form a solid deposit on the surface of the substrate. CVD furnaces are widely used in industries such as semiconductor manufacturing, aerospace, and materials science to create protective coatings, improve surface properties, or fabricate advanced materials. These furnaces are designed to operate under controlled atmospheres, often with vacuum or gas purging capabilities, to ensure precise and uniform deposition. Key features include high-temperature uniformity, programmable temperature control, and compatibility with various tube materials like quartz and alumina.
Key Points Explained:
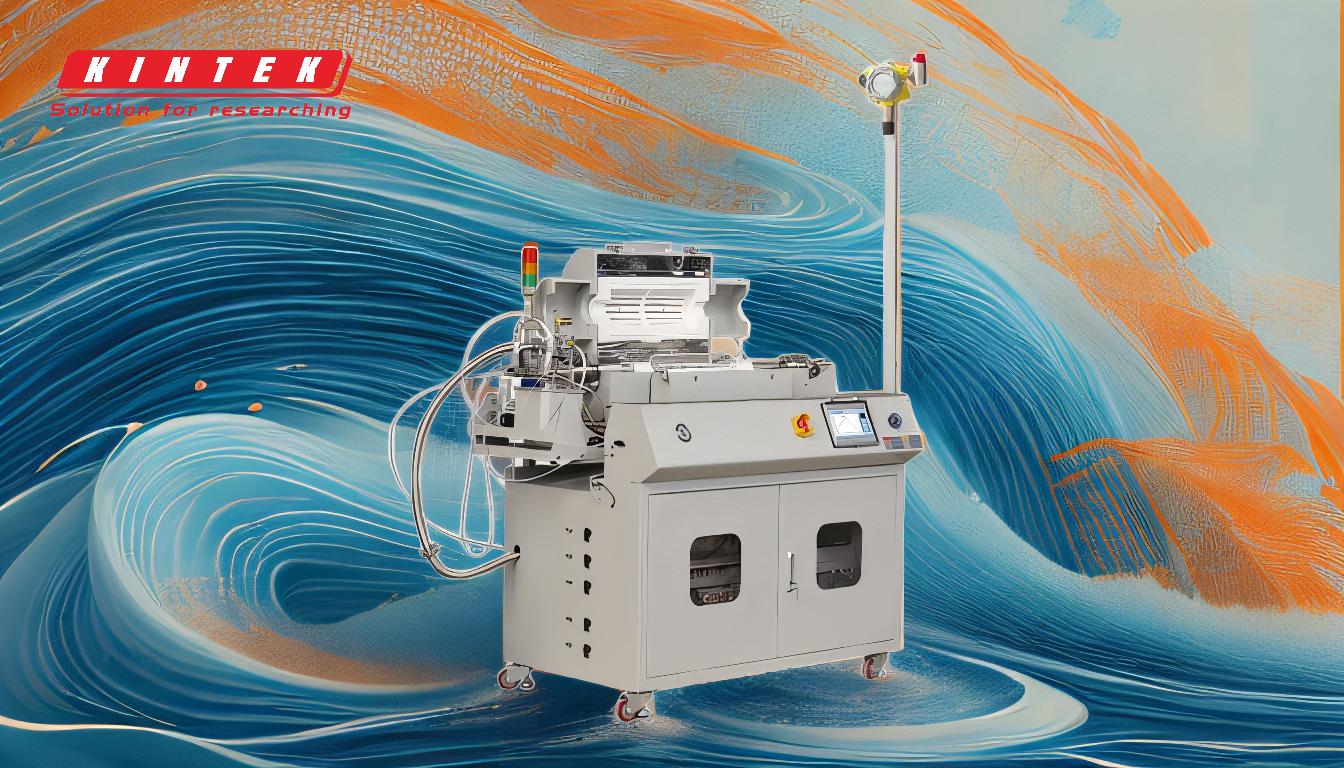
-
Definition and Purpose of a CVD Furnace:
- A CVD furnace is a specialized furnace used for the Chemical Vapor Deposition (CVD) process, which involves depositing a thin layer of material onto a substrate. This process is critical for applications like corrosion protection, oxidation resistance, and the fabrication of advanced materials.
- The furnace is designed to create a controlled environment where gaseous precursors react at high temperatures to form a solid deposit on the substrate.
-
Applications of CVD Furnaces:
- Semiconductor Manufacturing: Used to deposit thin films of materials like silicon, silicon dioxide, and silicon nitride on semiconductor wafers.
- Aerospace and Automotive Industries: Applied to create protective coatings on mechanical parts to enhance durability and resistance to wear, corrosion, and oxidation.
- Materials Science: Utilized in the development of advanced materials, such as graphene, carbon nanotubes, and ceramic coatings.
-
Key Features of CVD Furnaces:
- High-Temperature Uniformity: Ensures consistent deposition across the substrate, which is critical for achieving high-quality coatings.
- Programmable Temperature Control: Allows precise control over the deposition process, enabling customization for different materials and applications.
- Vacuum and Gas Purging Capabilities: Maintains a controlled atmosphere, preventing contamination and ensuring the purity of the deposited material.
- Compatibility with Various Tube Materials: CVD furnaces often use quartz or alumina tubes, which can withstand high temperatures and corrosive environments.
-
Types of CVD Furnaces:
- CVD Tube Furnace: Features a vertically standing chamber with a fixed well tube reactor. It is commonly used for quenching tests on wire-shaped materials under vacuum or atmospheric protection. Key components include high alumina fiber lining, powerful heaters, and vacuum tubes with SS KF flanges for vacuum pumping and gas purging.
- Other Variations: Depending on the application, CVD furnaces may vary in design, such as horizontal or vertical configurations, and may include additional features like multi-zone heating or advanced gas delivery systems.
-
Comparison with Other Furnaces:
- Vacuum Furnaces: While vacuum furnaces are used for processes like annealing, sintering, and brazing, CVD furnaces are specifically designed for chemical vapor deposition. Both operate under controlled atmospheres, but CVD furnaces focus on material deposition rather than heat treatment.
- Drying Ovens and Muffle Furnaces: These are used for drying, baking, or high-temperature processing but lack the specialized capabilities for CVD processes.
-
Advantages of CVD Furnaces:
- Precision and Uniformity: The ability to control temperature and atmosphere ensures precise and uniform deposition.
- Versatility: Can be used for a wide range of materials and applications, from thin films to advanced composites.
- Efficiency: Modern CVD furnaces are designed for fast heating and cooling, with low energy consumption.
-
Considerations for Purchasing a CVD Furnace:
- Temperature Range: Ensure the furnace can achieve the required temperatures for your specific application (e.g., up to 1200°C for quartz tubes or 1700°C for alumina tubes).
- Atmosphere Control: Look for features like vacuum pumping and gas purging to maintain a controlled environment.
- Compatibility: Check the compatibility of the furnace with the materials and substrates you plan to use.
- Control System: A microprocessor PID-controlled system offers precise temperature control and programmability.
By understanding these key points, you can make an informed decision when selecting a CVD furnace for your specific needs, whether in industrial production or advanced research.
Summary Table:
Aspect | Details |
---|---|
Applications | Semiconductor manufacturing, aerospace coatings, advanced materials science |
Key Features | High-temperature uniformity, programmable control, vacuum/gas purging |
Advantages | Precision, versatility, efficiency, compatibility with quartz/alumina tubes |
Considerations | Temperature range, atmosphere control, material compatibility |
Ready to enhance your material deposition process? Contact us today to find the perfect CVD furnace for your needs!