A furnace belt is a critical component in industrial furnaces, designed to facilitate the movement of materials through the heating and cooling chambers. It ensures even heat distribution and efficient processing of materials, particularly in high-temperature environments exceeding 752 °F (400 °C). Over time, the belt may wear out, leading to operational issues such as noise or bearing damage. Understanding its role, maintenance needs, and importance in industrial processes is essential for ensuring the longevity and efficiency of furnace systems.
Key Points Explained:
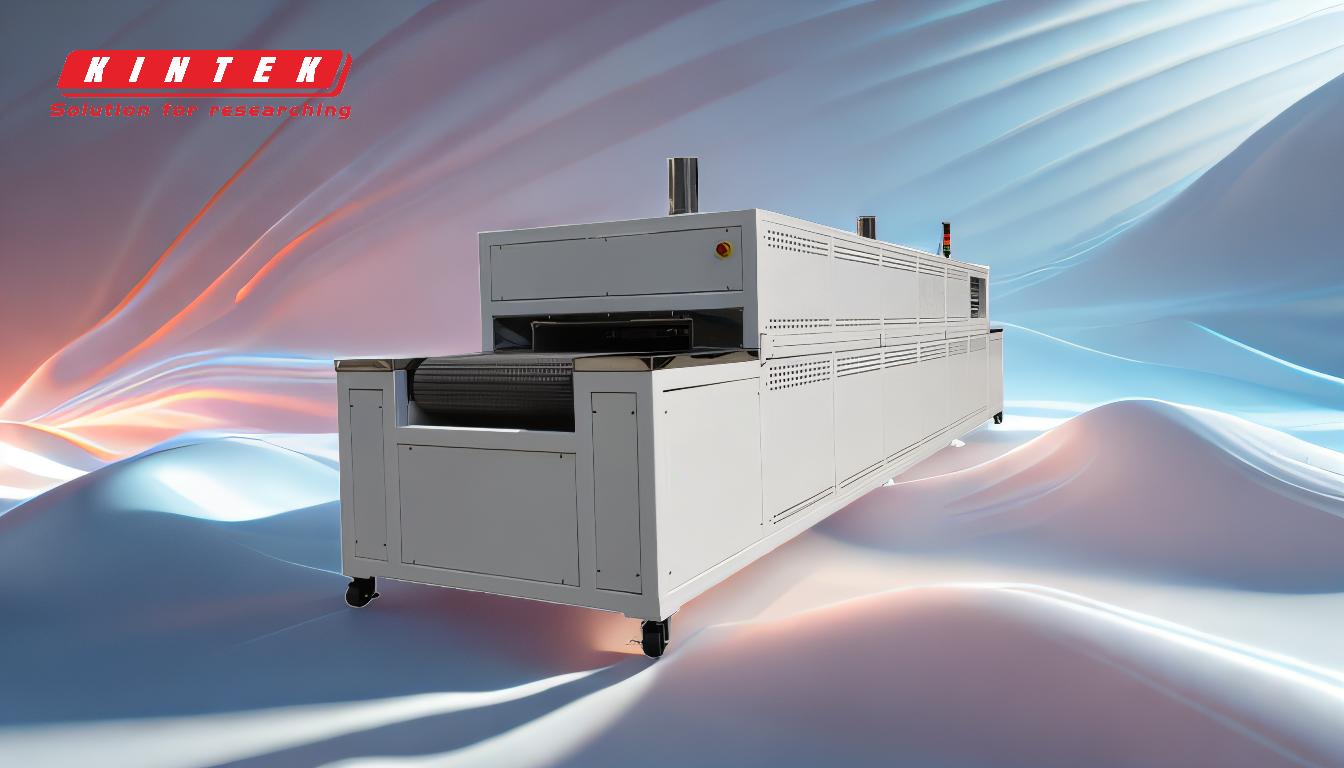
-
Definition and Function of a Furnace Belt:
- A furnace belt is a mechanical component used in industrial furnaces to transport materials through the heating and cooling chambers.
- It ensures consistent heat distribution, which is vital for processes requiring precise temperature control, such as material preparation or manufacturing applications.
- The belt's movement allows for continuous processing, improving efficiency and throughput in industrial operations.
-
Role in Industrial Furnaces:
- Furnaces are designed to provide high-temperature environments, often exceeding 752 °F (400 °C), for various industrial processes.
- The furnace belt is integral to the loading mechanism, enabling the smooth transfer of materials into and out of the heating and cooling chambers.
- Without a functioning belt, the furnace's ability to maintain consistent temperature and process materials efficiently would be compromised.
-
Components and Design:
- Furnace belts are typically made from materials capable of withstanding extreme temperatures and mechanical stress, such as heat-resistant alloys or ceramics.
- They are designed to operate seamlessly within the furnace's heating and cooling chambers, ensuring minimal friction and wear.
- The belt's design often includes features to enhance durability, such as reinforced edges or coatings to resist corrosion and abrasion.
-
Common Issues and Maintenance:
- Over time, furnace belts may experience wear and tear due to continuous exposure to high temperatures and mechanical stress.
- Common issues include hissing noises, which may indicate misalignment or damage to the belt, and bearing wear, which can affect the belt's movement.
- Regular maintenance, such as lubrication, alignment checks, and timely replacement of worn components, is essential to prevent operational disruptions and extend the belt's lifespan.
-
Importance for Equipment Purchasers:
- For purchasers of industrial equipment, understanding the furnace belt's role and maintenance requirements is crucial for selecting the right furnace system.
- A high-quality furnace belt ensures reliable performance, reducing downtime and maintenance costs.
- When evaluating furnaces, purchasers should consider the belt's material, design, and compatibility with their specific industrial processes to ensure optimal efficiency and longevity.
-
Applications in Industrial Processes:
- Furnace belts are used in a wide range of industries, including metallurgy, ceramics, and manufacturing, where high-temperature processing is required.
- They are essential for applications such as annealing, sintering, and heat treatment, where precise temperature control and material handling are critical.
- The belt's ability to withstand extreme conditions makes it indispensable for industries relying on continuous and efficient heat processing.
By understanding the furnace belt's function, design, and maintenance needs, industrial operators and equipment purchasers can make informed decisions to optimize their processes and ensure the longevity of their furnace systems.
Summary Table:
Aspect | Details |
---|---|
Function | Transports materials through heating/cooling chambers for consistent processing. |
Role | Ensures smooth material transfer and maintains consistent furnace temperatures. |
Materials | Heat-resistant alloys or ceramics for durability in extreme conditions. |
Common Issues | Hissing noises, bearing wear, misalignment due to high-temperature stress. |
Maintenance | Regular lubrication, alignment checks, and timely replacement of worn parts. |
Applications | Used in metallurgy, ceramics, and manufacturing for annealing, sintering, etc. |
Optimize your industrial furnace performance—contact our experts today to learn more about furnace belts!