A hydrogen furnace for sintering is a specialized industrial furnace that uses hydrogen as the primary atmosphere to sinter materials, particularly metals and ceramics. This type of furnace is essential for processes requiring high-purity environments, as hydrogen effectively reduces surface oxides and removes impurities like silica from alloys. It prevents metal oxidation, ensuring superior mechanical properties and a bright surface finish in the final product. Hydrogen sintering furnaces are widely used for sintering stainless steel, annealing, and welding high-temperature materials. They are also critical in 3D printing for debinding and sintering ceramic and metal parts, achieving densities up to 99.5%. Safety measures are crucial due to hydrogen's reactive nature.
Key Points Explained:
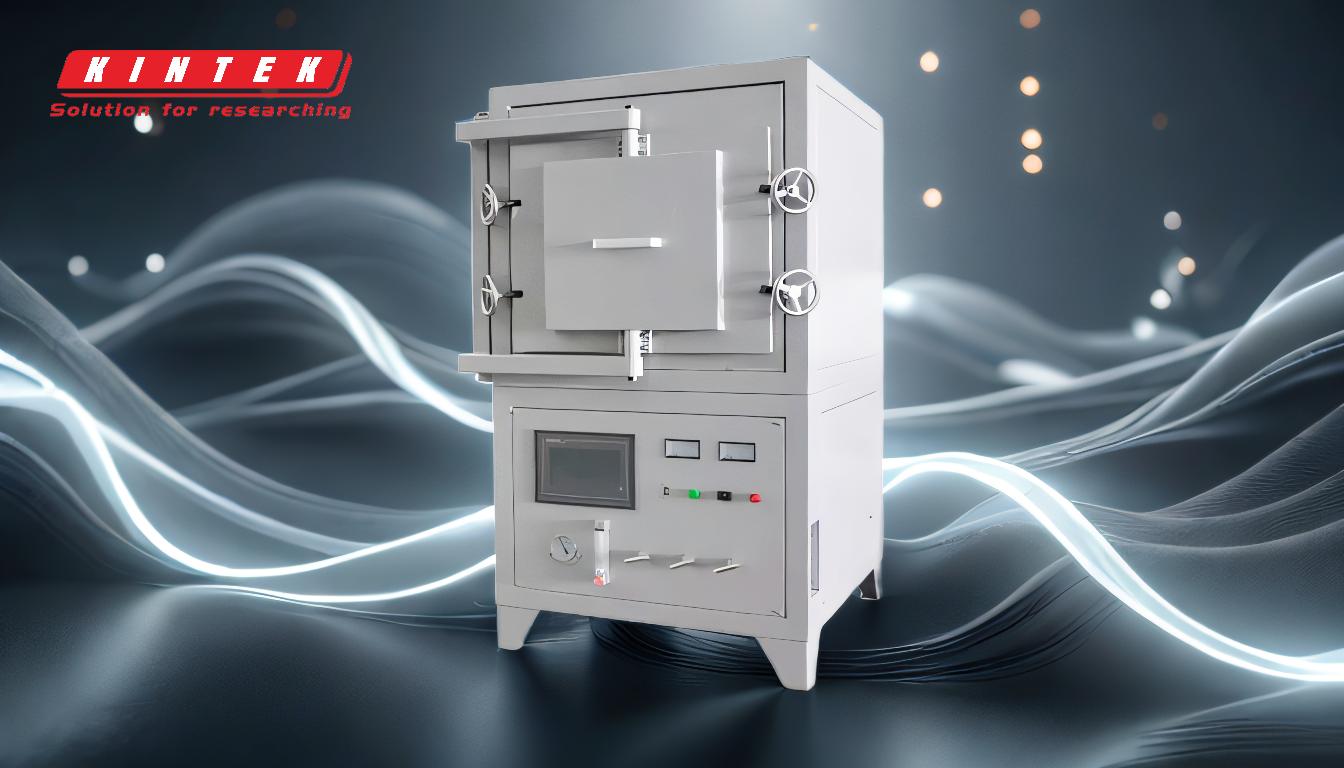
-
Purpose of a Hydrogen Furnace for Sintering:
- A hydrogen atmosphere furnace is designed to create a high-purity environment for sintering, annealing, and welding high-temperature materials.
- It is particularly effective for sintering stainless steel and other metals, as hydrogen reduces surface oxides and removes impurities like silica, ensuring clean and high-quality parts.
-
Benefits of Using Hydrogen in Sintering:
- High Purity: Hydrogen provides an atmosphere with purity levels exceeding 99.9995%, making it suitable for a wide range of materials.
- Oxide Reduction: Hydrogen reduces surface oxides, preventing metal oxidation and improving the aggregation ratio of powders.
- Impurity Removal: It strips impurities such as silica from alloys, enhancing furnace atmosphere performance.
- Mechanical Properties: Parts produced in a hydrogen furnace exhibit superior mechanical qualities and a bright surface finish.
-
Applications of Hydrogen Sintering Furnaces:
- Stainless Steel Sintering: Hydrogen is widely used for sintering stainless steel due to its ability to reduce oxides and control carbon content by removing residual carbon from binders.
- 3D Printing: Hydrogen furnaces are essential for sintering and debinding ceramic and metal parts in 3D printing, achieving densities up to 99.5% and desired mechanical properties.
- High-Temperature Materials: These furnaces are used for sintering, annealing, and welding special high-temperature materials.
-
Components of a Hydrogen Sintering Furnace:
- The main components include the furnace cover (door), bottom (head), furnace body, and electric control system. These components work together to maintain the high-purity hydrogen atmosphere required for sintering.
-
Safety Considerations:
- Due to hydrogen's highly reactive nature, additional safety measures are necessary when operating a hydrogen sintering furnace. Proper ventilation, leak detection systems, and explosion-proof equipment are critical to ensure safe operation.
-
Hydrogen and Nitrogen Mix:
- A hydrogen and nitrogen mix is often used in the sintering atmosphere to act as a carbon restoration gas. This mixture helps maintain the carbon content in powdered metals, ensuring they remain carbon-rich and free of pressing lubricants while preventing oxidation.
-
Impact on Material Properties:
- Hydrogen sintering significantly improves fatigue life (1.5–8 times) and may enhance weldability. It also homogenizes castings, eliminates segregation, and produces slight improvements in tensile properties.
By understanding these key points, equipment and consumable purchasers can make informed decisions about the use of hydrogen sintering furnaces in their manufacturing processes. The high-purity environment, combined with the ability to reduce oxides and remove impurities, makes hydrogen sintering an invaluable process for producing high-quality parts with superior mechanical properties.
Summary Table:
Key Aspect | Details |
---|---|
Purpose | Creates a high-purity environment for sintering, annealing, and welding. |
Benefits | Reduces oxides, removes impurities, and improves mechanical properties. |
Applications | Sintering stainless steel, 3D printing, and high-temperature materials. |
Components | Furnace cover, bottom, body, and electric control system. |
Safety | Requires ventilation, leak detection, and explosion-proof equipment. |
Hydrogen-Nitrogen Mix | Acts as a carbon restoration gas, preventing oxidation. |
Material Impact | Enhances fatigue life, weldability, and tensile properties. |
Discover how a hydrogen sintering furnace can elevate your material processing—contact our experts today!