A vacuum furnace operator is a trained professional responsible for the safe and efficient operation of a vacuum furnace. This role involves managing the furnace's vacuum system, ensuring proper heating and cooling processes, and maintaining the equipment to prevent contamination and ensure high-quality outcomes. The operator must understand the technical aspects of the furnace, such as vacuum creation, temperature control, and inert gas usage, as well as follow strict safety protocols. Their expertise ensures that materials like metals and ceramics are processed under optimal conditions, achieving desired properties such as strength, durability, and resistance to oxidation.
Key Points Explained:
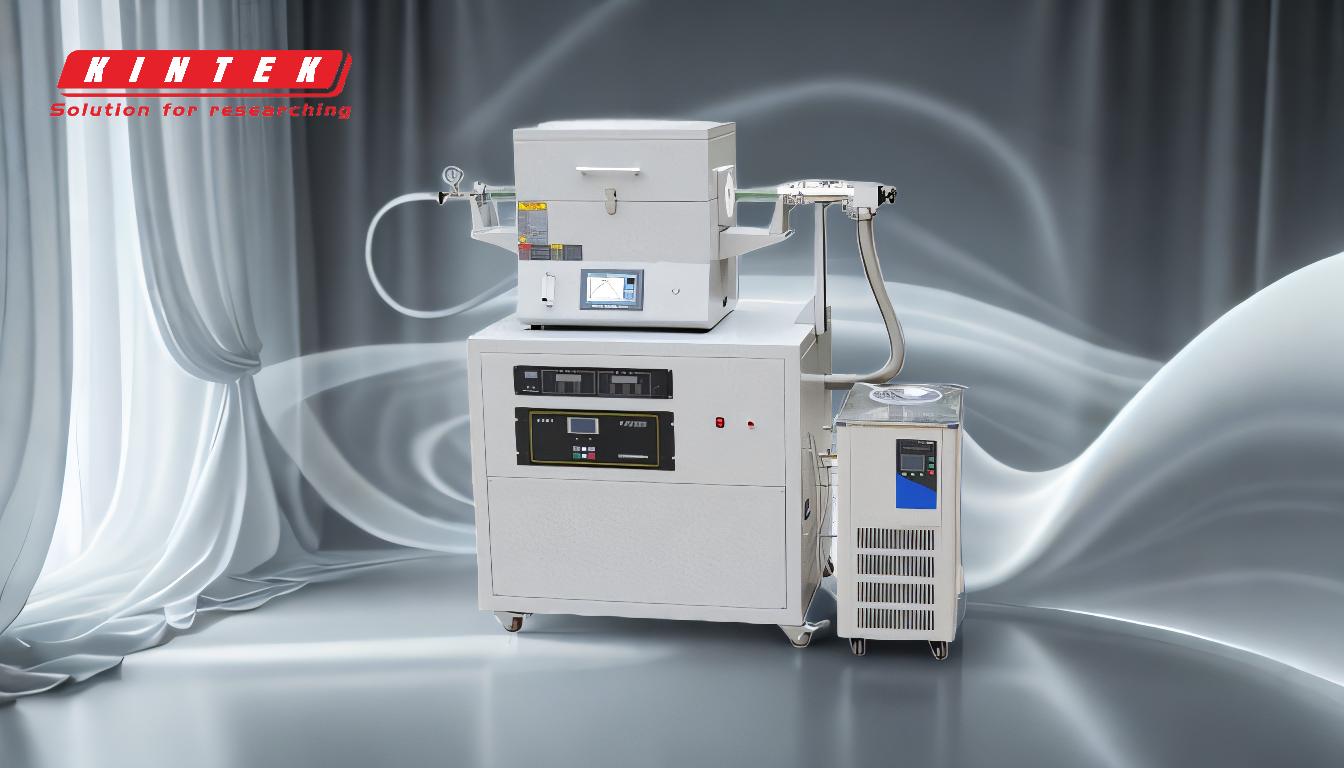
-
Role and Responsibilities of a Vacuum Furnace Operator
- A vacuum furnace operator oversees the entire operation of the vacuum furnace, from setup to shutdown.
- Their primary responsibilities include:
- Loading and unloading materials into the furnace chamber.
- Monitoring and adjusting vacuum levels, temperature, and pressure to meet specific process requirements.
- Ensuring the proper use of inert gases, such as argon or nitrogen, to prevent oxidation and contamination.
- Conducting routine maintenance and troubleshooting to ensure the furnace operates efficiently.
- Operators must follow strict safety protocols to prevent accidents, such as burns or exposure to hazardous gases.
-
Understanding the Vacuum Furnace System
- The operator must have a deep understanding of the furnace's components and how they work together:
- Vacuum System: This includes vacuum pumps, gauges, and valves that reduce pressure inside the chamber to create a vacuum.
- Heating Mechanism: The furnace uses methods like induction heating or resistance heating to achieve high temperatures.
- Cooling System: Inert gases are pressurized and circulated to cool materials quickly after processing.
- The operator ensures that all components function correctly and that the furnace maintains the desired vacuum and temperature levels.
- The operator must have a deep understanding of the furnace's components and how they work together:
-
Material Processing in a Vacuum Furnace
- The vacuum furnace is used for processes like sintering, brazing, and heat treatment of materials such as metals and ceramics.
- The operator ensures that materials are processed under optimal conditions, free from contamination and oxidation.
- They monitor the furnace's performance to achieve precise temperature control, which is critical for achieving the desired material properties.
-
Safety and Training Requirements
- Operating a vacuum furnace requires specialized training due to the high temperatures, vacuum conditions, and potential hazards involved.
- Operators must be familiar with:
- Emergency shutdown procedures.
- Handling inert gases safely.
- Preventing and responding to equipment malfunctions.
- Regular training and certification are essential to ensure operators remain competent and up-to-date with industry standards.
-
Importance of Precision and Consistency
- The operator plays a critical role in maintaining the precision and consistency of the furnace's output.
- They must carefully monitor and adjust process parameters to ensure that each batch of materials meets the required specifications.
- Any deviation in temperature, pressure, or vacuum level can affect the quality of the final product.
-
Maintenance and Troubleshooting
- Routine maintenance is essential to keep the vacuum furnace operating efficiently.
- The operator is responsible for:
- Cleaning the furnace chamber and components.
- Inspecting and replacing worn-out parts, such as heating elements or vacuum seals.
- Identifying and resolving issues that could affect performance, such as leaks or temperature fluctuations.
- Proper maintenance extends the lifespan of the furnace and ensures consistent results.
In summary, a vacuum furnace operator is a highly skilled professional who ensures the safe and efficient operation of a vacuum furnace. Their expertise in vacuum systems, temperature control, and material processing is essential for achieving high-quality outcomes in industries such as aerospace, automotive, and manufacturing.
Summary Table:
Key Aspect | Details |
---|---|
Role | Oversees vacuum furnace operation from setup to shutdown. |
Responsibilities | - Load/unload materials. - Monitor vacuum, temperature, and pressure. - Use inert gases. - Perform maintenance and troubleshooting. |
Furnace Components | - Vacuum system (pumps, gauges, valves). - Heating mechanism (induction/resistance). - Cooling system (inert gases). |
Material Processing | Processes metals and ceramics for sintering, brazing, and heat treatment. |
Safety and Training | Requires specialized training in emergency procedures, gas handling, and equipment maintenance. |
Precision and Consistency | Ensures precise temperature control and consistent output for high-quality results. |
Maintenance | Routine cleaning, inspection, and troubleshooting to maintain furnace efficiency. |
Need expert guidance on vacuum furnace operations? Contact us today for support and solutions!