Cold working and hot working are two fundamental metalworking processes used to shape and form metals into desired shapes and sizes. Cold working is performed at temperatures below the metal's recrystallization temperature, which increases strength and hardness but reduces ductility. Examples include rolling, drawing, and bending. Hot working, on the other hand, is done above the recrystallization temperature, allowing the metal to be shaped more easily without significant hardening. Examples include forging, extrusion, and hot rolling. Both processes have distinct advantages and are chosen based on the desired properties of the final product.
Key Points Explained:
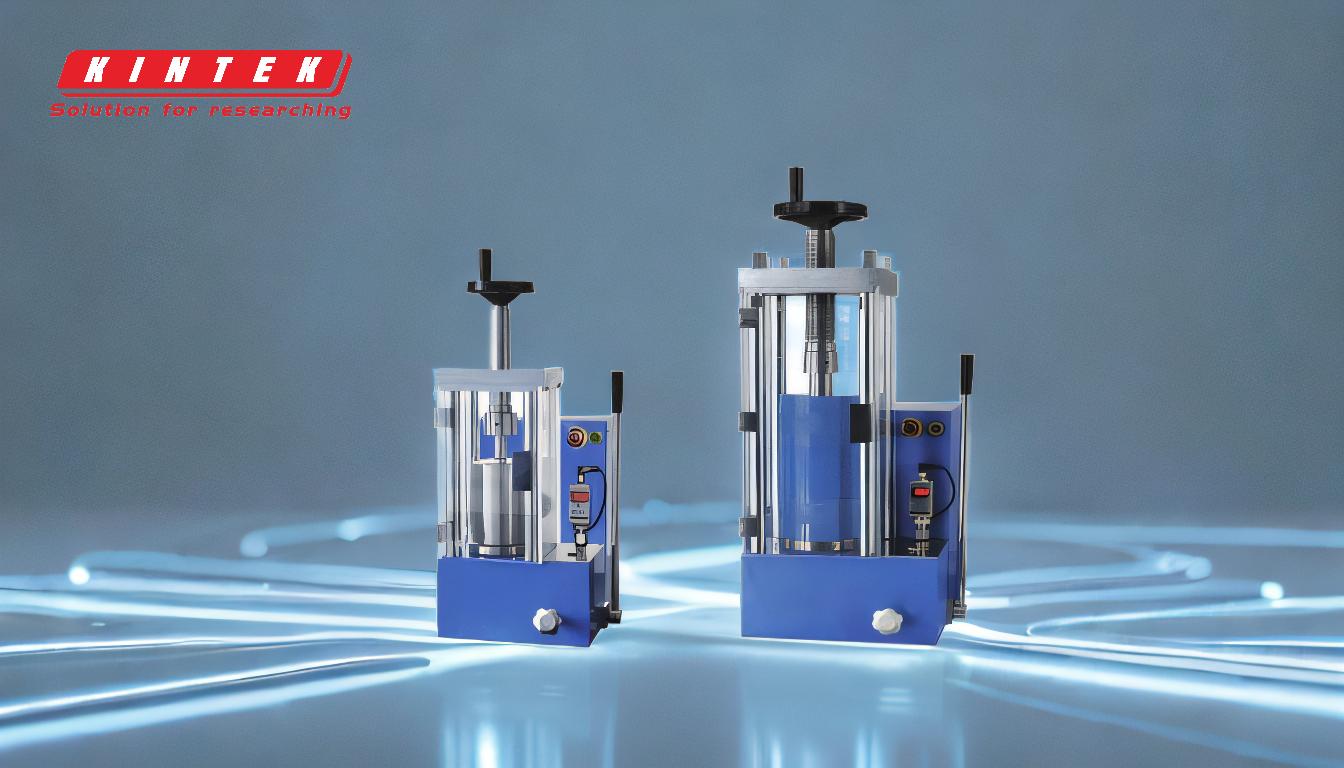
-
Cold Working:
- Definition: Cold working refers to the process of shaping metals at temperatures below their recrystallization point. This process increases the metal's strength and hardness but reduces its ductility.
-
Examples:
- Rolling: Passing metal through rollers to reduce thickness and improve surface finish.
- Drawing: Pulling metal through a die to create wires or tubes.
- Bending: Applying force to metal to change its shape without heating.
- Advantages: Improved strength, better surface finish, and precise dimensional control.
- Disadvantages: Reduced ductility, increased brittleness, and higher energy consumption due to increased resistance to deformation.
-
Hot Working:
- Definition: Hot working involves shaping metals at temperatures above their recrystallization point. This allows the metal to be deformed more easily without significant hardening.
-
Examples:
- Forging: Shaping metal using localized compressive forces, often with hammers or presses.
- Extrusion: Forcing metal through a die to create long, uniform shapes.
- Hot Rolling: Rolling metal at high temperatures to reduce thickness and improve mechanical properties.
- Advantages: Easier deformation, reduced energy consumption, and improved ductility.
- Disadvantages: Potential for oxidation, less precise dimensional control, and the need for high-temperature equipment.
-
Comparison of Cold and Hot Working:
- Temperature: Cold working is done below the recrystallization temperature, while hot working is done above it.
- Material Properties: Cold working increases strength and hardness but reduces ductility, whereas hot working maintains or improves ductility.
- Applications: Cold working is often used for precision parts and components requiring high strength, while hot working is used for large-scale shaping and forming.
-
Choosing Between Cold and Hot Working:
- Material Type: Some materials are better suited to cold working, while others require hot working to achieve the desired properties.
- End-Use Requirements: The final application of the metal part will dictate whether cold or hot working is more appropriate.
- Economic Considerations: The cost of equipment, energy consumption, and production speed can influence the choice between the two processes.
By understanding the differences and applications of cold and hot working, manufacturers can select the most appropriate process to achieve the desired properties and performance in their metal products.
Summary Table:
Aspect | Cold Working | Hot Working |
---|---|---|
Temperature | Below recrystallization temperature | Above recrystallization temperature |
Examples | Rolling, Drawing, Bending | Forging, Extrusion, Hot Rolling |
Advantages | Increased strength, better surface finish | Easier deformation, improved ductility |
Disadvantages | Reduced ductility, higher energy consumption | Oxidation risk, less precise control |
Applications | Precision parts, high-strength components | Large-scale shaping and forming |
Need help choosing between cold and hot working for your project? Contact our experts today for tailored advice!