Atmosphere brazing, specifically controlled atmosphere brazing (CAB), is a specialized process used to join metal components in a controlled environment to prevent oxidation and ensure high-quality joints. The process involves moving parts through a furnace on a conveyor belt, where the atmosphere is typically oxygen-free, using gases like nitrogen or hydrogen. This method includes several stages, such as cleaning, pre-assembly, application of filler material, heating, brazing, and cooling. The controlled environment ensures that the joints are clean, strong, and free from defects like oxidation. This technique is particularly useful in industries where precision and reliability are critical.
Key Points Explained:
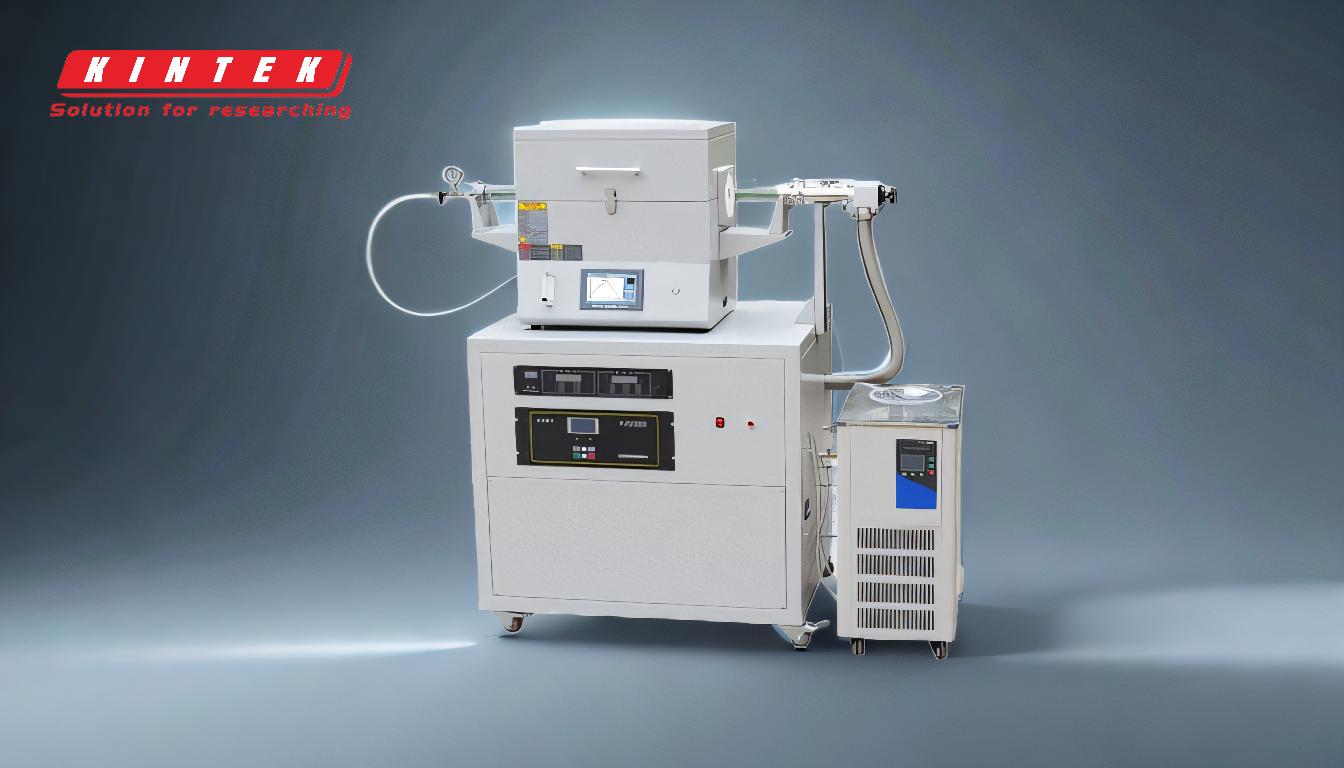
-
Definition of Atmosphere Brazing:
- Atmosphere brazing, particularly controlled atmosphere brazing (CAB), is a process where metal parts are joined in a controlled environment to prevent oxidation and ensure high-quality joints. This method is essential in industries where precision and reliability are paramount.
-
Process Overview:
- The process involves moving parts through a furnace on a conveyor belt. The atmosphere inside the furnace is carefully controlled, typically using oxygen-free gases like nitrogen or hydrogen. This controlled environment is crucial to prevent oxidation and ensure the integrity of the joints.
-
Stages of Controlled Atmosphere Brazing:
- Cleaning and Degreasing: The first step involves cleaning the components to remove any contaminants that could affect the brazing process.
- Pre-Assembly: Components are pre-assembled using methods like press fit or TIG welding to ensure they are correctly positioned before brazing.
- Application of Filler Material: A paste or ring filler material is applied to the joints. This filler material has a lower melting point than the adjacent metal, allowing it to flow into the joint during the heating process.
- Preheating (Optional): Depending on the specific requirements, the components may be preheated to prepare them for the brazing process.
- Heating and Brazing: The components are heated to a temperature just below the melting point of the base metals, allowing the filler material to melt and flow into the joint.
- Cooling: After brazing, the components are cooled to solidify the joint and complete the process.
-
Benefits of Controlled Atmosphere Brazing:
- Oxidation Prevention: The controlled environment prevents oxidation, ensuring clean and high-quality joints.
- High-Quality Joints: The process results in strong, reliable joints that are free from defects.
- Versatility: CAB can be used with a variety of metals and is suitable for complex assemblies.
-
Comparison with Vacuum Brazing:
- Environment: While CAB uses a controlled atmosphere of gases like nitrogen or hydrogen, vacuum brazing takes place in a vacuum environment.
- Process: Both processes involve heating components and using a filler metal to create joints, but the environment and specific steps may vary.
- Applications: CAB is often used in industries where a continuous process is needed, while vacuum brazing is preferred for high-precision applications where contamination must be minimized.
-
Applications of Atmosphere Brazing:
- Automotive Industry: CAB is widely used in the automotive industry for joining components like heat exchangers and air conditioning systems.
- Aerospace: The aerospace industry utilizes CAB for joining critical components that require high strength and reliability.
- Electronics: In the electronics industry, CAB is used for joining components that require precise and clean joints.
In summary, controlled atmosphere brazing is a sophisticated process that ensures the creation of high-quality, oxidation-free joints in a controlled environment. This method is essential in industries where precision, reliability, and cleanliness are critical. By understanding the stages and benefits of CAB, manufacturers can achieve superior results in their brazing processes.
Summary Table:
Aspect | Details |
---|---|
Definition | Joining metal parts in a controlled, oxygen-free environment to prevent oxidation. |
Key Stages | Cleaning, pre-assembly, filler application, heating, brazing, and cooling. |
Benefits | Oxidation prevention, high-quality joints, and versatility. |
Applications | Automotive, aerospace, and electronics industries. |
Comparison with Vacuum Brazing | CAB uses gases like nitrogen/hydrogen; vacuum brazing occurs in a vacuum. |
Ready to enhance your metal joining process? Contact us today to learn more about controlled atmosphere brazing!