Calcination is a thermal treatment process primarily used to decompose materials, remove volatile components, and induce chemical or physical changes in substances. It is widely applied in industries such as cement production, metallurgy, and materials synthesis. The process involves heating materials to high temperatures below their melting points, often in the presence of limited air or oxygen. Key applications include the decomposition of limestone to produce lime, the removal of impurities from metal ores, and the synthesis of advanced materials like zeolites. Calcination also plays a crucial role in processes such as devitrification of glass and the removal of water or volatile compounds from samples.
Key Points Explained:
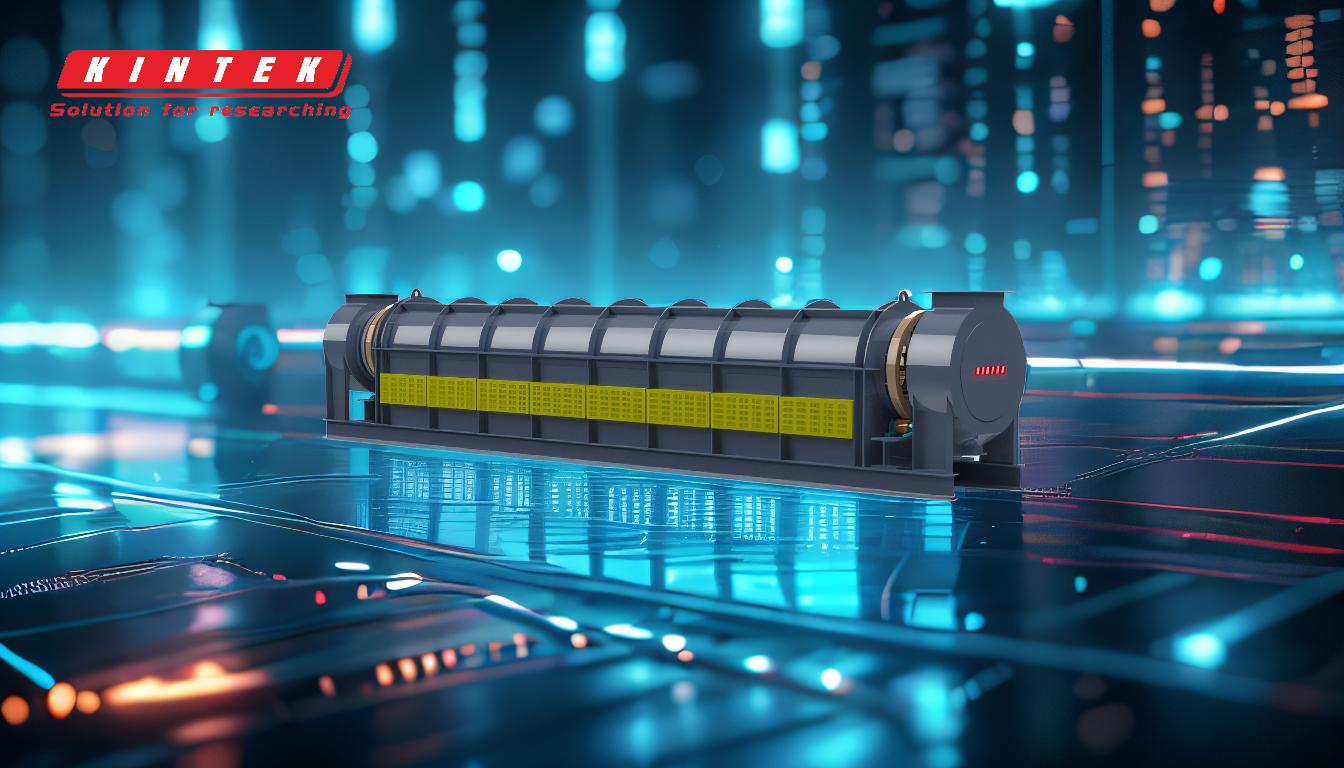
-
Decomposition of Limestone:
- Calcination is most commonly used to decompose limestone (calcium carbonate) into lime (calcium oxide) and carbon dioxide. This reaction is fundamental in cement production, where lime is a key ingredient.
- The process is represented by the chemical equation:
[ \text{CaCO}_3 \rightarrow \text{CaO} + \text{CO}_2 ] - This application is critical in the construction industry, as cement is a primary building material.
-
Removal of Volatile Impurities in Metallurgy:
- In metallurgy, calcination is used to heat metal ores in the presence of limited air or oxygen to remove volatile impurities such as sulfur dioxide, carbon dioxide, or water.
- This process helps purify the metal ore, making it suitable for further refining or extraction.
- For example, in the extraction of zinc, calcination removes sulfur and other impurities from zinc sulfide ores.
-
Synthesis of Zeolites:
- Calcination is employed in the synthesis of zeolites, a class of porous materials used in catalysis, adsorption, and ion exchange.
- During zeolite synthesis, calcination removes ammonium ions from the precursor material, enabling the formation of the desired crystalline structure.
-
Devitrification of Glass:
- Calcination is used in the glass industry to induce phase transformations through devitrification. This process converts amorphous glass into a crystalline or semi-crystalline material, enhancing its mechanical and thermal properties.
-
Removal of Water and Volatile Constituents:
- Calcination is widely used to remove water (dehydration) or other volatile components from materials. This is particularly important in the preparation of powdered materials, ceramics, and catalysts.
- For example, in the production of alumina (aluminum oxide), calcination removes water from aluminum hydroxide to produce a pure, anhydrous form of alumina.
-
Oxidation and Chemical Transformation:
- Calcination can be used to oxidize part or all of a substance, leading to chemical transformations. This is useful in processes such as the production of pigments or the modification of material properties.
- For instance, calcination is used to convert iron oxide into a more stable form for use in pigments or magnetic materials.
-
Applications in Cement Production:
- The production of cement is one of the most significant applications of calcination. The process involves heating limestone and other raw materials to high temperatures to form clinker, which is then ground into cement powder.
- This application underscores the importance of calcination in the construction and infrastructure sectors.
-
Role in Advanced Material Synthesis:
- Calcination is a key step in the synthesis of advanced materials, such as catalysts, ceramics, and nanomaterials. It helps achieve the desired chemical composition, crystal structure, and physical properties.
By understanding these key points, it becomes clear that calcination is a versatile and essential process in various industrial and scientific applications. Its ability to induce chemical and physical changes in materials makes it indispensable in fields ranging from construction to advanced material synthesis.
Summary Table:
Key Applications of Calcination | Description |
---|---|
Decomposition of Limestone | Converts calcium carbonate into lime and CO₂, vital for cement production. |
Removal of Volatile Impurities | Purifies metal ores by removing sulfur, water, and other impurities. |
Synthesis of Zeolites | Enables the formation of porous materials used in catalysis and adsorption. |
Devitrification of Glass | Converts amorphous glass into crystalline or semi-crystalline forms. |
Removal of Water and Volatiles | Produces anhydrous materials like alumina for ceramics and catalysts. |
Oxidation and Chemical Changes | Transforms substances for use in pigments, magnetic materials, and more. |
Cement Production | Forms clinker from limestone, a critical step in cement manufacturing. |
Advanced Material Synthesis | Achieves desired properties in catalysts, ceramics, and nanomaterials. |
Discover how calcination can optimize your industrial processes—contact our experts today!