Ceramic insulation is primarily used in high-temperature environments where thermal resistance is critical. It is commonly found in applications such as tube seals, furnace maintenance, high-temperature gaskets, fabric expansion joints, and industrial insulation blankets. Its excellent thermal insulation properties make it ideal for these uses, although it lacks the strength and durability of materials like glass mat. Beyond industrial applications, ceramics are also widely used in everyday items like ceramic knives and sanitary ware, showcasing their versatility. This material is chosen for its ability to withstand extreme heat while providing effective insulation.
Key Points Explained:
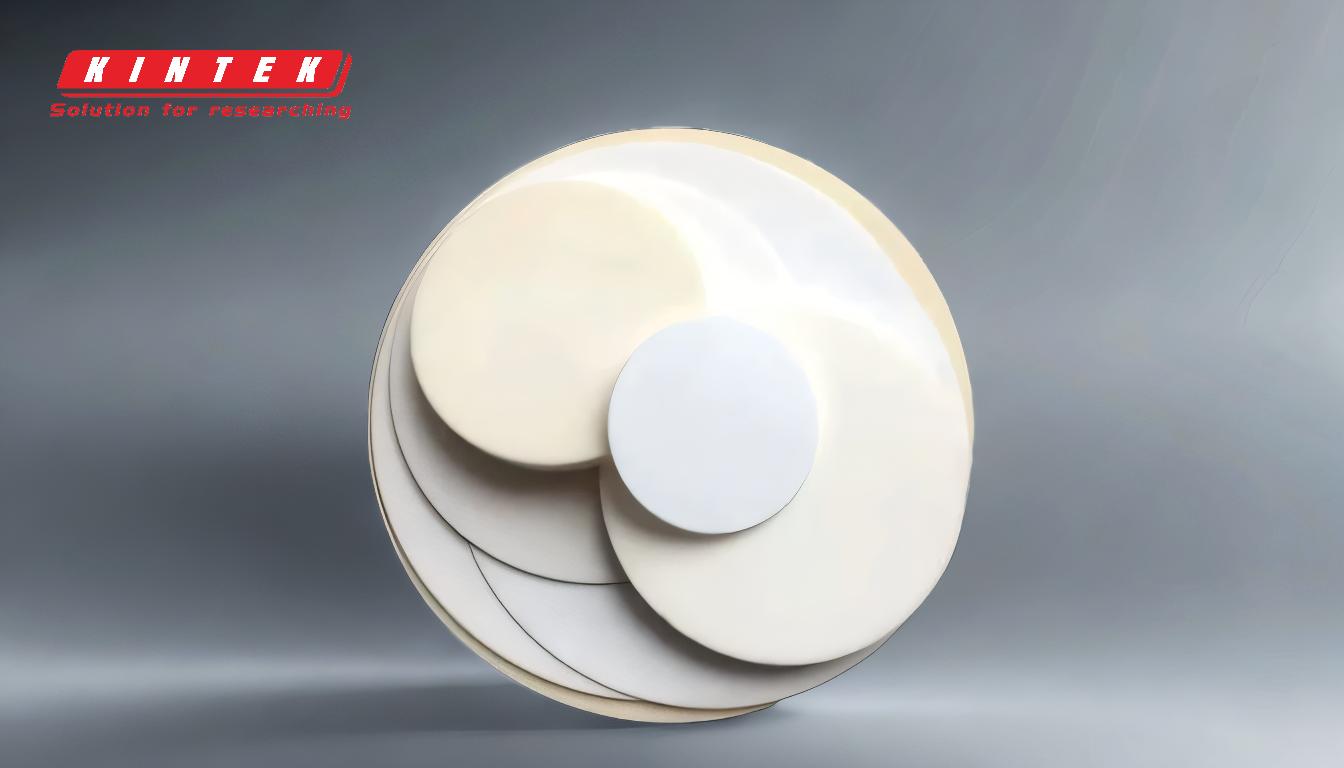
-
High-Temperature Applications:
- Tube Seals: Ceramic insulation is used in tube seals to prevent heat loss and ensure efficient thermal management in high-temperature systems.
- Furnace Maintenance: It is employed in furnaces to maintain high temperatures and protect the structure from heat damage.
- High-Temperature Gaskets: These gaskets use ceramic insulation to seal joints and prevent heat leakage in industrial equipment.
-
Industrial Insulation:
- Fabric Expansion Joints: Ceramic insulation is used in fabric expansion joints to accommodate thermal expansion and contraction in industrial piping systems.
- Industrial Insulation Blankets: These blankets provide thermal insulation for equipment and pipelines, reducing heat loss and improving energy efficiency.
-
Thermal Resistance vs. Strength:
- Thermal Resistance: Ceramic insulation excels in thermal resistance, making it suitable for high-temperature environments.
- Strength and Durability: While it provides excellent insulation, ceramic insulation is not as strong or durable as materials like glass mat, which may limit its use in certain applications.
-
Everyday Uses of Ceramics:
- Ceramic Knives: Known for their sharpness and resistance to wear, ceramic knives are a common household item.
- Ceramic Sanitary Ware: Used in bathrooms and kitchens, ceramic sanitary ware is valued for its durability and ease of cleaning.
-
Versatility of Ceramic Materials:
- Industrial and Domestic Applications: Ceramic materials are versatile, finding use in both high-temperature industrial settings and everyday household items.
- Material Properties: The unique properties of ceramics, such as thermal resistance and hardness, make them suitable for a wide range of applications.
In summary, ceramic insulation is a critical material in high-temperature industrial applications, providing excellent thermal resistance. However, its lower strength and durability compared to other materials like glass mat may limit its use in certain scenarios. Beyond industrial uses, ceramics are also widely used in everyday items, highlighting their versatility and importance in various fields.
Summary Table:
Application | Description |
---|---|
High-Temperature Applications | - Tube Seals: Prevents heat loss in high-temperature systems. |
- Furnace Maintenance: Protects furnace structures from heat damage. | |
- High-Temperature Gaskets: Seals joints to prevent heat leakage. | |
Industrial Insulation | - Fabric Expansion Joints: Accommodates thermal expansion in piping systems. |
- Industrial Insulation Blankets: Reduces heat loss in equipment. | |
Everyday Uses | - Ceramic Knives: Sharp, wear-resistant household items. |
- Ceramic Sanitary Ware: Durable and easy to clean. | |
Material Properties | - Thermal Resistance: Ideal for high-temperature environments. |
- Strength & Durability: Less durable than materials like glass mat. |
Interested in ceramic insulation for your high-temperature needs? Contact us today to learn more!