Debinding and sintering are critical steps in powder metallurgy and ceramic manufacturing processes. Debinding involves the removal of binding agents from a shaped part, which is typically achieved through thermal degradation, evaporation, or solvent extraction. Sintering follows debinding and involves heating the part to high temperatures to fuse the metal or ceramic particles, resulting in a dense and strong final product. These processes are carefully controlled, with specific temperature profiles, heating rates, and holding times to ensure the integrity of the part. Factors such as furnace size, insulation, and vacuum environment are also crucial for optimizing the process.
Key Points Explained:
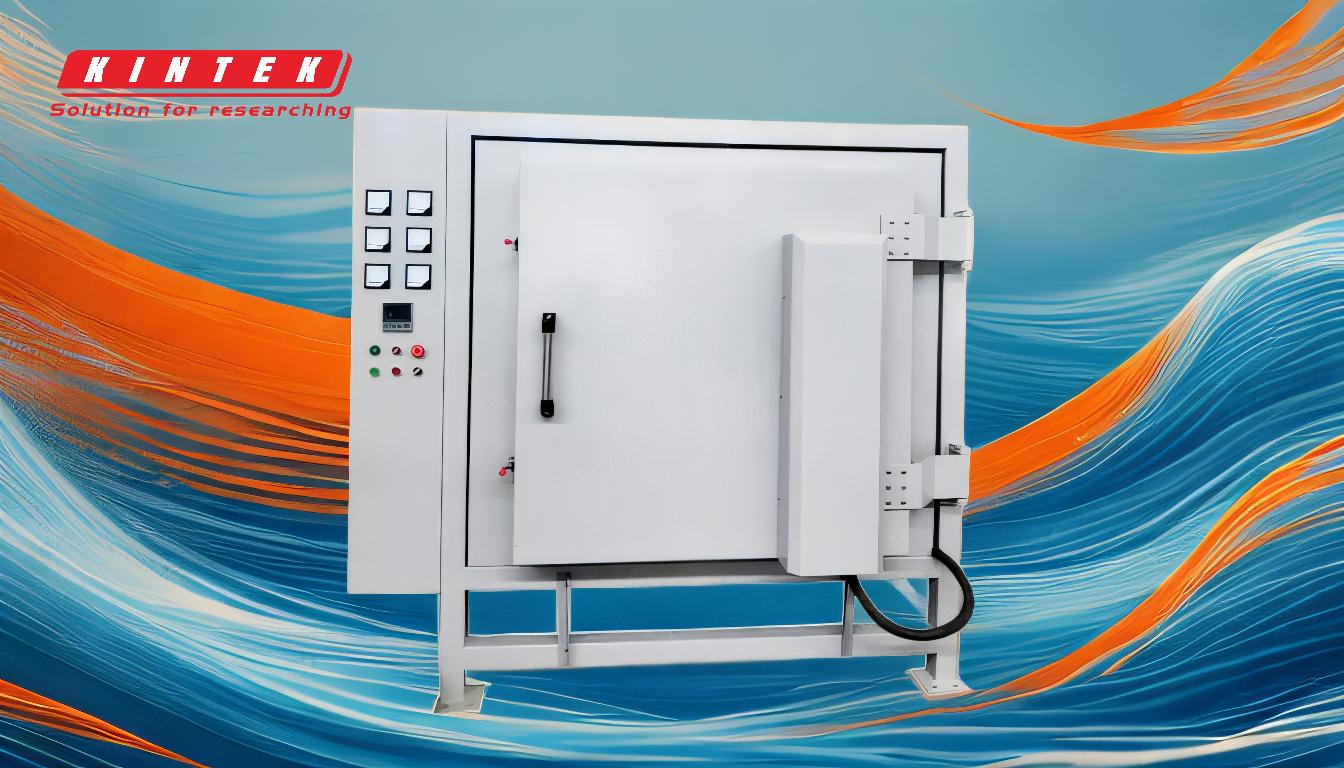
-
Debinding Process:
- Purpose: The primary goal of debinding is to remove the binding agents (e.g., polymeric binders like paraffin) used to shape the metal or ceramic powder into the desired form. These binders are necessary during the shaping process but must be removed before sintering to prevent defects.
- Methods: Debinding can be achieved through thermal degradation, evaporation, or solvent extraction, depending on the type of binder used.
- Temperature Control: The process typically starts at room temperature and gradually increases to around 600°C. Precise control of the temperature profile is essential to avoid defects such as warping or cracking.
-
Sintering Process:
- Purpose: Sintering is the process of heating the debound part to high temperatures (e.g., 1,300°C) to fuse the metal or ceramic particles, resulting in a dense and strong final product.
- Temperature Profile: The sintering process involves several high-temperature cycles. For example, parts are heated to 225°C at a rate of 2°C/min, then to 550°C at 1°C/min and held for 2 hours, followed by heating to 1,300°C at 6°C/min and held for varying times (40 to 180 minutes). Finally, parts are cooled to 600°C at 6°C/min and then cooled in the furnace.
- Environment: Sintering is often performed in a vacuum environment inside a graphite furnace to prevent oxidation and ensure uniform heating.
-
Combined vs. Separate Processes:
- Combined Processes: In some cases, debinding and sintering can be combined into a single continuous process, which can save time and energy. However, this requires careful control of the temperature profile and atmosphere to ensure both processes are effectively carried out.
- Separate Processes: In other cases, debinding and sintering are performed as separate steps, allowing for more precise control of each process. This approach may be necessary for complex parts or materials that require specific debinding conditions.
-
Furnace Considerations:
- Size and Configuration: The size of the furnace and whether to use a boxed or non-boxed configuration are important considerations. These factors influence the efficiency and cost-effectiveness of the sintering process.
- Insulation: The type of insulation used in the thermal chamber is crucial for maintaining the required high temperatures and ensuring uniform heating of the parts.
-
Defect Prevention:
- Control of Parameters: Careful control of temperature profile, pressure, gas atmosphere, and anneal time is essential to avoid defects such as warps and cracks during both debinding and sintering.
- Material Considerations: The specific properties of the metal or ceramic powder, as well as the type of binder used, must be taken into account when planning the debinding and sintering processes to ensure the final product meets the desired specifications.
In summary, debinding and sintering are complex processes that require precise control of various parameters to produce high-quality metal or ceramic parts. Understanding the key factors involved, such as temperature profiles, furnace configuration, and defect prevention, is essential for optimizing these processes.
Summary Table:
Process | Purpose | Key Details |
---|---|---|
Debinding | Remove binding agents from shaped parts. | Methods: Thermal degradation, evaporation, solvent extraction. Temperature control up to 600°C. |
Sintering | Fuse metal/ceramic particles for dense, strong products. | Temperature cycles up to 1,300°C. Performed in vacuum environments for uniform heating. |
Combined/Separate | Optimize time and precision. | Combined: Single process for efficiency. Separate: Better control for complex parts. |
Furnace Setup | Ensure efficiency and cost-effectiveness. | Size, configuration (boxed/non-boxed), and insulation are critical for maintaining high temperatures. |
Defect Prevention | Avoid warps and cracks. | Control temperature, pressure, gas atmosphere, and anneal time. Consider material and binder types. |
Need help optimizing your debinding and sintering processes? Contact our experts today for tailored solutions!