Deposition on a substrate refers to the process of creating thin or thick layers of a substance on a solid surface, atom-by-atom or molecule by molecule. This process alters the properties of the substrate surface, depending on the application. The thickness of these layers can vary significantly, from a single atom (nanometer scale) to several millimeters, depending on the deposition method and material used. Techniques such as ion bombardment, diamond powder scratching, and ultrasonic treatment are often employed to prepare the substrate surface before deposition. Common methods for depositing thin films include e-beam evaporation and thermal evaporation. Deposition is crucial in various industries for creating coatings that enhance the functionality, durability, or aesthetic appeal of materials.
Key Points Explained:
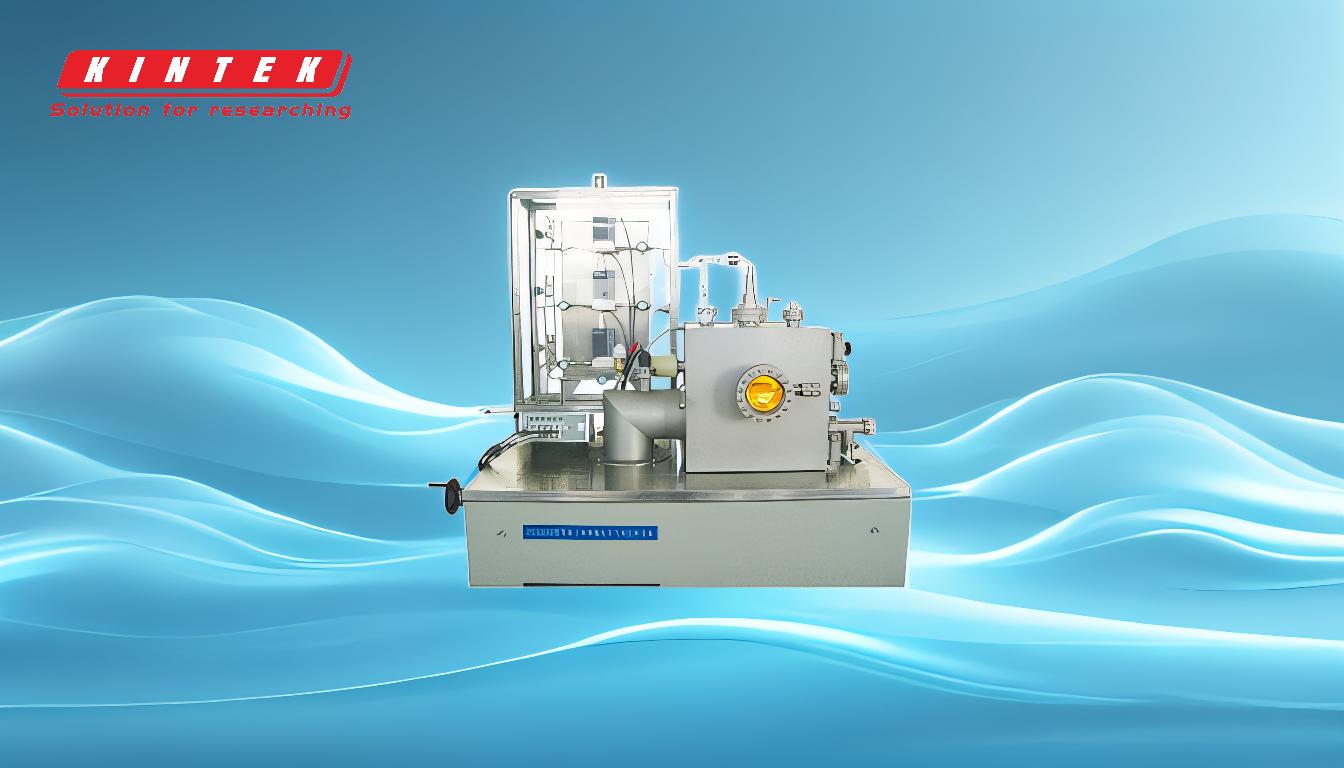
-
Definition of Deposition on a Substrate:
- Deposition involves creating layers of material on a solid surface, either atom-by-atom or molecule by molecule.
- The process changes the properties of the substrate surface, making it suitable for specific applications.
-
Thickness of Deposited Layers:
- The thickness of the deposited layers can range from a single atom (nanometer scale) to several millimeters.
- The specific thickness depends on the deposition method and the type of material being used.
-
Preparation of Substrate Surface:
- Before deposition, the substrate surface often undergoes various treatments to ensure proper adhesion and quality of the deposited layer.
- Common techniques include ion bombardment, diamond powder scratching, and ultrasonic treatment with a diamond solution.
-
Deposition Methods:
- E-beam Evaporation: This method uses an electron beam to heat the material, causing it to evaporate and deposit onto the substrate.
- Thermal Evaporation: In this technique, the material is heated in a vacuum until it evaporates and then condenses on the substrate.
-
Applications of Deposition:
- Deposition is used in various industries to create coatings that enhance the functionality, durability, or aesthetic appeal of materials.
- Applications include semiconductor manufacturing, optical coatings, and protective layers for tools and machinery.
-
Importance of Controlled Synthesis:
- Deposition or growth refers to the controlled synthesis, growth, or transfer of materials as thin films on a substrate.
- A thin film is a layer of material ranging from fractions of a nanometer (monolayer) to several micrometers in thickness, crucial for precise applications in technology and industry.
By understanding these key points, one can appreciate the complexity and importance of deposition processes in modern material science and engineering.
Summary Table:
Aspect | Details |
---|---|
Definition | Creating layers of material on a solid surface, altering its properties for specific applications. |
Thickness Range | From a single atom (nanometer scale) to several millimeters. |
Surface Preparation | Techniques like ion bombardment, diamond powder scratching, and ultrasonic treatment. |
Deposition Methods | E-beam evaporation, thermal evaporation. |
Applications | Semiconductor manufacturing, optical coatings, protective layers for tools and machinery. |
Importance | Enables controlled synthesis of thin films for precise technological and industrial applications. |
Discover how deposition can enhance your material applications—contact our experts today!