Magnetron sputtering is a highly efficient and versatile physical vapor deposition (PVD) technique used to create thin films on substrates. It involves the use of plasma ions to sputter material from a target, which then deposits onto a substrate, forming a thin film. This method is widely used in industries such as microelectronics, semiconductors, and optical production due to its high deposition rates, precise control, and ability to work with a wide range of materials. Magnetron sputtering is particularly valued for its ability to produce high-purity, uniform, and adhesive films at low temperatures, making it a cost-effective solution for large-scale production.
Key Points Explained:
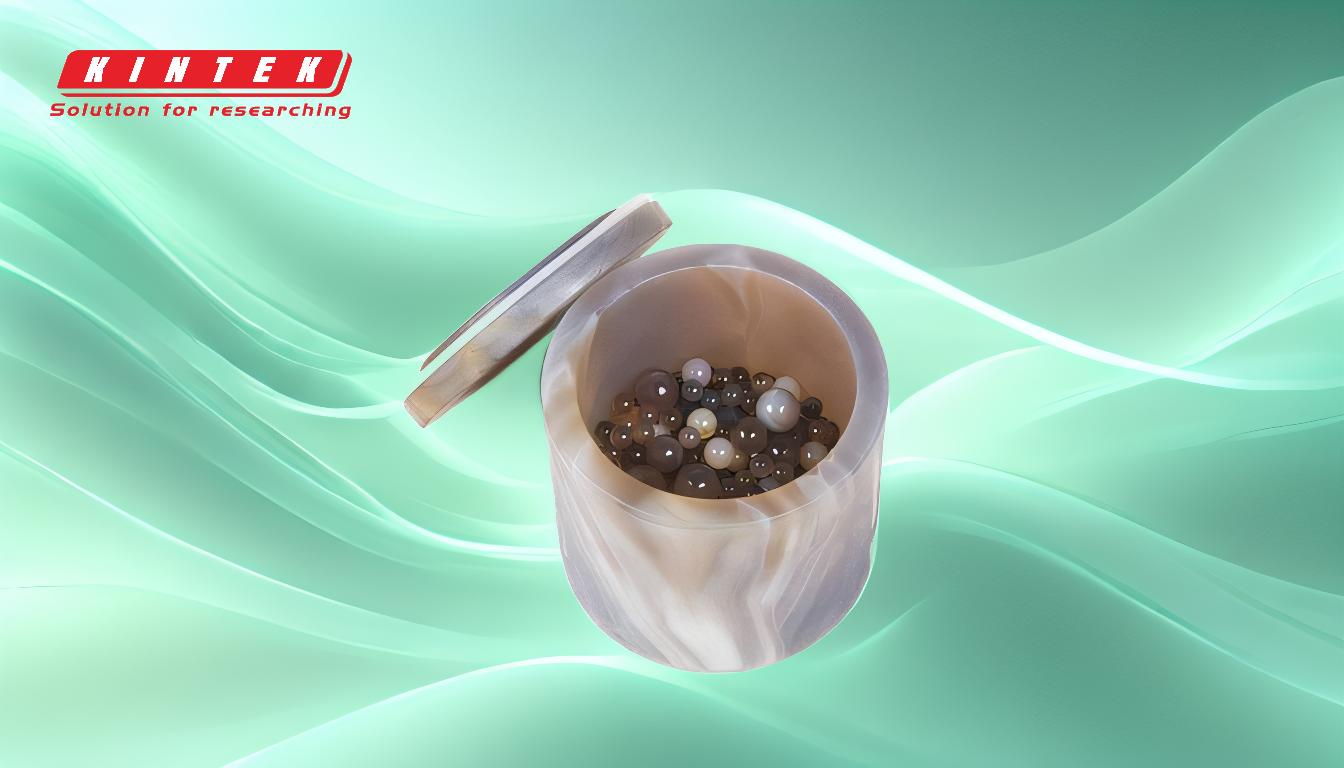
-
Definition and Process of Magnetron Sputtering:
- Magnetron sputtering is a plasma-based physical vapor deposition method.
- Plasma ions interact with a target material, causing atoms to sputter and form a thin film on a substrate.
- The process involves the use of a high magnetic and electric field to confine plasma electrons close to the target, enhancing sputtering efficiency.
-
Mechanism of Thin Film Formation:
- Ions are accelerated towards the cathode (target), and upon collision, they sputter out material atoms.
- These sputtered atoms travel and deposit onto a substrate, forming a thin film.
- The technique allows for precise control over the deposition process, ensuring uniformity and high-quality films.
-
Advantages of Magnetron Sputtering:
- High Deposition Rate: Enables rapid thin film formation, suitable for large-scale production.
- Material Versatility: Can deposit a wide range of materials, including metals, alloys, dielectrics, and nitrides.
- High Purity and Adhesion: Produces films with excellent purity and strong adhesion to substrates.
- Low-Temperature Operation: Ideal for temperature-sensitive substrates.
- Cost-Effectiveness: Efficient and economical for producing large quantities of films.
-
Applications in Industry:
- Widely used in microelectronics, semiconductors, and optical production.
- Suitable for depositing dielectric and nitride films, which are critical in advanced electronic devices.
- Enables the creation of uniform films on large-area substrates, essential for industrial applications.
-
RF Magnetron Sputtering:
- A specialized form of magnetron sputtering that does not require the target to be conductive.
- Expands the range of materials that can be used for thin film deposition, including insulators and ceramics.
-
Ongoing Research and Advancements:
- Magnetron sputtering continues to evolve with advancements in plasma physics and material science.
- Research focuses on improving deposition rates, film quality, and expanding the range of applicable materials.
By leveraging the principles of magnetron sputtering, industries can achieve high-performance thin films with exceptional precision and efficiency, making it a cornerstone technology in modern manufacturing and research.
Summary Table:
Key Aspect | Details |
---|---|
Process | Plasma-based PVD technique using magnetic and electric fields. |
Mechanism | Ions sputter target material, forming thin films on substrates. |
Advantages | High deposition rate, material versatility, high purity, low-temperature. |
Applications | Microelectronics, semiconductors, optical production, and more. |
Specialized Form | RF Magnetron Sputtering: works with non-conductive materials. |
Research Focus | Improving deposition rates, film quality, and material range. |
Discover how a magnetron sputtering machine can revolutionize your production process—contact us today!