Metal forming with a hydraulic press is a manufacturing process that uses hydraulic pressure to shape metal into desired forms. This method is widely used in industries for its precision, efficiency, and ability to handle large-scale production. The process involves placing a metal workpiece between two dies and applying high pressure through a hydraulic system to deform the metal into the desired shape. Hydraulic presses are versatile and can be used for various metal forming techniques, including forging, stamping, and deep drawing. The use of a hydraulic hot press machine enhances the process by allowing the metal to be heated, making it more malleable and easier to shape.
Key Points Explained:
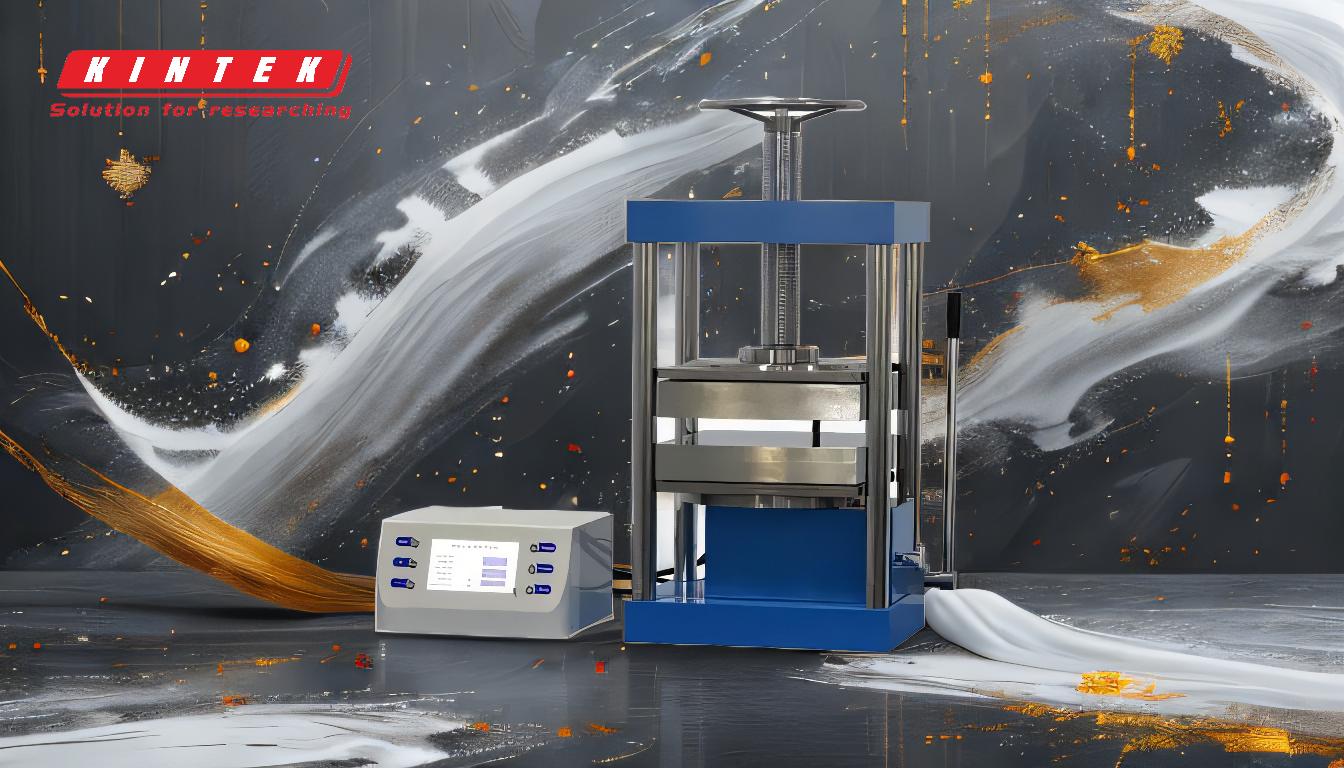
-
Understanding Hydraulic Presses:
- Hydraulic presses operate using Pascal's principle, where a small force applied to a small area creates a larger force over a larger area. This principle allows hydraulic presses to generate immense pressure, making them ideal for metal forming.
- The main components of a hydraulic press include a hydraulic cylinder, a piston, and a hydraulic pump. These components work together to apply controlled pressure to the metal workpiece.
-
Types of Metal Forming Processes:
- Forging: This process involves shaping metal by applying compressive forces. Hydraulic presses are commonly used in forging to produce strong, durable metal parts.
- Stamping: Stamping uses a hydraulic press to cut or shape metal sheets into specific forms. This process is often used in the automotive industry to create body parts.
- Deep Drawing: This technique involves drawing a metal sheet into a die to create hollow shapes, such as cups or cans. Hydraulic presses provide the necessary force to achieve deep draws without tearing the metal.
-
Advantages of Using Hydraulic Presses:
- Precision: Hydraulic presses offer precise control over the pressure and speed of the forming process, resulting in high-quality, consistent products.
- Versatility: These presses can be used for a wide range of metal forming applications, from small, intricate parts to large, heavy-duty components.
- Efficiency: Hydraulic presses can handle high-volume production with minimal manual intervention, reducing labor costs and increasing productivity.
-
Role of Hydraulic Hot Press Machines:
- A hydraulic hot press machine is specifically designed to work with heated metal. Heating the metal reduces its hardness and increases its ductility, making it easier to form complex shapes without cracking or breaking.
- The heating element in these machines can be controlled to maintain the optimal temperature for the specific metal being formed, ensuring consistent results.
-
Applications in Various Industries:
- Automotive: Hydraulic presses are used to manufacture car body parts, engine components, and other critical parts.
- Aerospace: The precision and strength of hydraulic presses make them suitable for producing aircraft components that require high strength-to-weight ratios.
- Construction: Metal forming with hydraulic presses is essential for creating structural components like beams, frames, and reinforcements.
-
Safety and Maintenance Considerations:
- Operating hydraulic presses requires strict adherence to safety protocols to prevent accidents. Regular maintenance of the hydraulic system, including checking for leaks and ensuring proper fluid levels, is crucial for optimal performance.
- Training operators on the correct use of hydraulic presses and understanding the limits of the equipment can prevent damage to both the machine and the workpiece.
In conclusion, metal forming with a hydraulic press is a highly efficient and versatile manufacturing process that leverages hydraulic pressure to shape metal into desired forms. The use of a hydraulic hot press machine further enhances this process by allowing the metal to be heated, making it more malleable and easier to shape. This method is widely used across various industries, including automotive, aerospace, and construction, due to its precision, efficiency, and ability to handle large-scale production.
Summary Table:
Aspect | Details |
---|---|
Key Process | Uses hydraulic pressure to shape metal into desired forms. |
Main Components | Hydraulic cylinder, piston, and hydraulic pump. |
Common Techniques | Forging, stamping, deep drawing. |
Advantages | Precision, versatility, efficiency, and high-volume production capability. |
Applications | Automotive, aerospace, construction. |
Safety Considerations | Regular maintenance, operator training, and adherence to safety protocols. |
Ready to enhance your metal forming process? Contact us today for expert advice and solutions!