Brazing is often preferred over other joining methods, such as welding or soldering, due to its ability to create strong, durable joints without significantly altering the base materials. Unlike welding, which involves melting the base metals, brazing uses a filler metal with a lower melting point, allowing it to flow into the joint by capillary action. This process minimizes thermal distortion and stress on the components, making it ideal for joining dissimilar metals or delicate parts. Additionally, brazing produces clean, aesthetically pleasing joints with excellent corrosion resistance, making it suitable for applications in industries like aerospace, automotive, and electronics.
Key Points Explained:
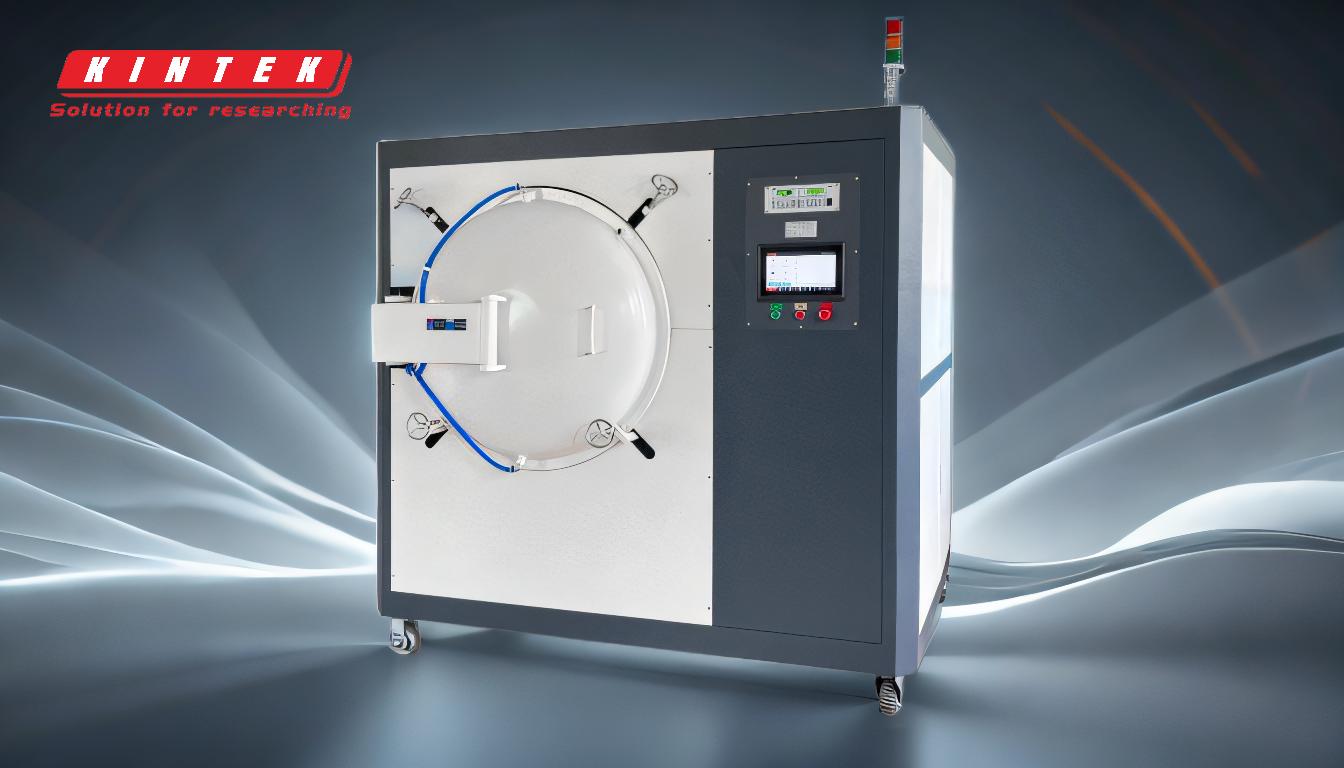
-
Minimized Thermal Distortion and Stress:
- Brazing operates at temperatures below the melting point of the base materials, reducing the risk of warping or distortion. This is particularly important for delicate or precision components where maintaining dimensional accuracy is critical.
- Unlike welding, which generates high heat and can create residual stresses, brazing distributes heat more evenly, resulting in stronger, more reliable joints.
-
Ability to Join Dissimilar Metals:
- Brazing is highly effective for joining dissimilar metals, such as copper to stainless steel or aluminum to titanium. This versatility is due to the filler metal's ability to bond with different materials without requiring them to be metallurgically compatible.
- This characteristic makes brazing a preferred method in industries like electronics, where components often consist of multiple materials.
-
Strong and Durable Joints:
- Brazed joints are known for their strength and durability, often matching or exceeding the strength of the base materials. The filler metal forms a metallurgical bond with the base metals, creating a joint that can withstand high mechanical loads and thermal cycling.
- The capillary action of the filler metal ensures complete penetration of the joint, resulting in a uniform and robust connection.
-
Clean and Aesthetic Results:
- Brazing produces clean, smooth joints with minimal surface roughness, making it ideal for applications where appearance matters, such as architectural or decorative components.
- The process also eliminates the need for extensive post-processing, such as grinding or polishing, reducing production time and costs.
-
Corrosion Resistance:
- Brazed joints often exhibit excellent corrosion resistance, especially when using filler metals like silver or nickel-based alloys. This makes brazing suitable for applications in harsh environments, such as marine or chemical industries.
- The absence of flux residues in properly executed brazing further enhances the joint's resistance to corrosion.
-
Cost-Effectiveness and Efficiency:
- Brazing is a cost-effective joining method, as it requires less energy and equipment compared to welding. The lower temperatures reduce energy consumption and extend the lifespan of heating equipment.
- The process is also highly efficient, allowing for the simultaneous joining of multiple components in a single operation, which is particularly advantageous in mass production.
In summary, brazing is a versatile and reliable joining method that offers numerous advantages over other techniques. Its ability to create strong, durable, and aesthetically pleasing joints with minimal thermal distortion makes it a preferred choice for a wide range of applications across various industries.
Summary Table:
Advantage | Description |
---|---|
Minimized Thermal Distortion | Operates below base material melting points, reducing warping and stress. |
Joins Dissimilar Metals | Bonds different metals without requiring metallurgical compatibility. |
Strong and Durable Joints | Creates joints that match or exceed base material strength. |
Clean and Aesthetic Results | Produces smooth, visually appealing joints with minimal post-processing. |
Corrosion Resistance | Offers excellent resistance, especially with silver or nickel-based fillers. |
Cost-Effective and Efficient | Requires less energy and allows simultaneous joining of multiple components. |
Interested in learning how brazing can benefit your projects? Contact our experts today for more information!