PVD (Physical Vapor Deposition) coating is a cutting-edge thin-film deposition technique that involves vaporizing a solid material in a vacuum environment and depositing it onto a substrate. This process creates highly durable, pure, or alloyed coatings that enhance the performance, durability, and aesthetics of various products. PVD coatings are widely used across industries, including electronics, optics, home hardware, and manufacturing, due to their ability to provide resistance to corrosion, wear, and high temperatures. The process is environmentally friendly, non-toxic, and produces ultra-thin, high-quality coatings that improve surface properties and functionality. PVD coatings are also versatile, enabling the creation of decorative finishes and functional enhancements for a wide range of applications.
Key Points Explained:
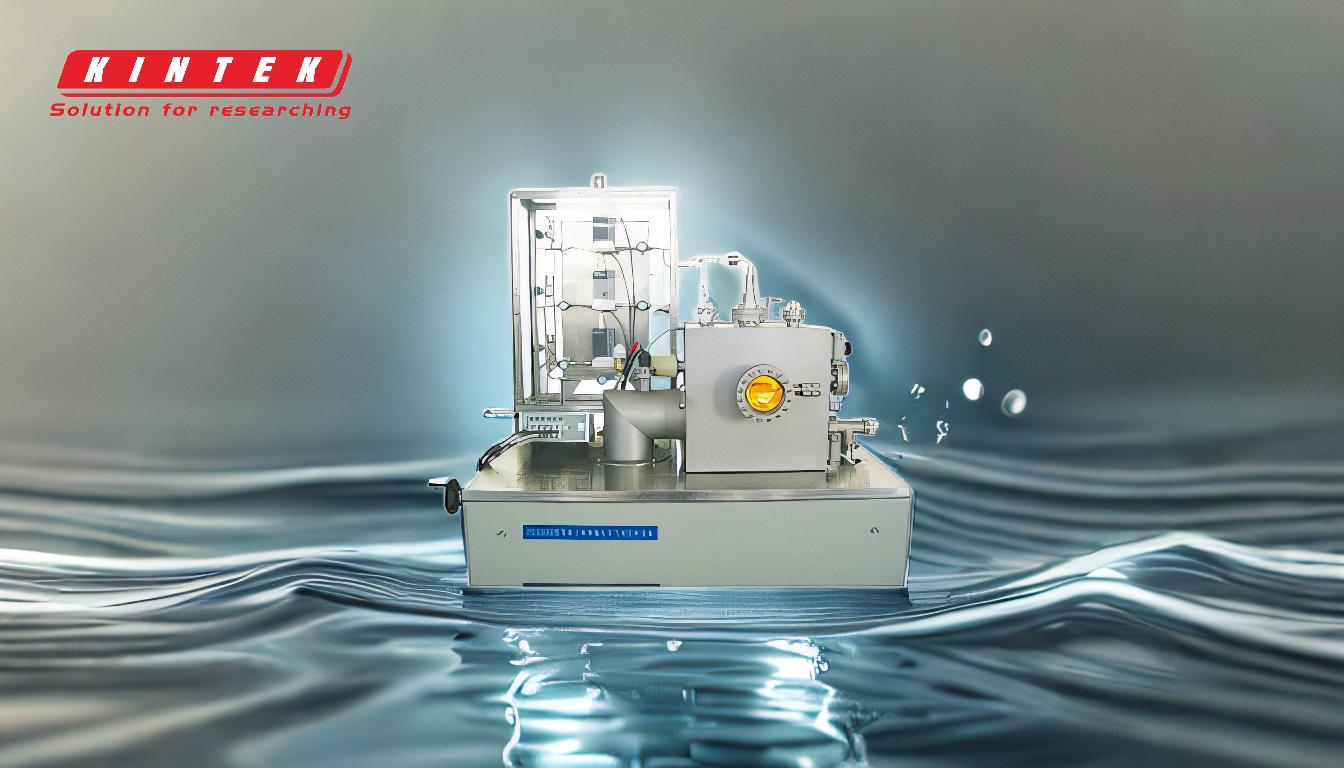
-
What is PVD Coating?
- PVD stands for Physical Vapor Deposition, a process where a solid material is vaporized in a vacuum and deposited onto a substrate as a thin film.
- The coatings can be pure materials or alloy compositions, tailored to specific applications.
- This technique is used to create highly durable, functional, and aesthetically pleasing finishes.
-
Applications of PVD Coating:
- Electronics: PVD coatings protect components from corrosion, wear, and abrasion, extending their lifespan. They also enhance electrical and thermal conductivity, improving device performance and reliability.
- Optics: Used for anti-reflection coatings in cameras, high-reflection coatings in solar receivers, and low-emission (low-e) coatings for glass. Low-e glass, for example, reflects heat, reduces UV fading, and improves energy efficiency.
- Home Hardware: PVD coatings are applied to door handles, window sills, and other fixtures to provide corrosion resistance and decorative finishes in various colors.
- Manufacturing: Used in cutting tools, semiconductor devices, and food packaging materials to enhance durability and functionality.
-
Environmental and Functional Benefits:
- PVD is an environmentally friendly process that meets FDA requirements and is non-toxic.
- The coatings are extremely thin and pure, achieved by depositing materials atom by atom.
- PVD improves surface quality, reduces roughness, and enhances product performance.
-
PVD by Sputtering:
- A specific PVD technique where high-energy particles bombard a target material, ejecting atoms or molecules that condense on a substrate to form a thin film.
- The process involves generating ions, directing them at a target, sputtering atoms, transporting them to the substrate, and condensing them into a film.
-
Durability and Resistance:
- PVD coatings are known for their resistance to high temperatures and wear, making them ideal for demanding applications.
- The lifespan of the coating depends on the product and the extent of heat exposure.
-
Process Steps:
- Cleaning the substrate to ensure proper adhesion.
- Creating an electrical arc in a vacuum chamber to vaporize and ionize a metal target.
- Combining the vaporized metal with gases to form a compound.
- Depositing the compound atom by atom onto the substrate.
- Testing the coating for consistency and quality.
-
Versatility and Innovation:
- PVD coatings are used in a wide range of industries, from decorative finishes to high-performance applications.
- Innovations include specialized tools for scientific purposes and advanced materials like titanium nitride (TiN) for cutting tools.
PVD coating is a versatile and advanced technology that combines durability, functionality, and aesthetics, making it a preferred choice for modern industrial and consumer applications.
Summary Table:
Aspect | Details |
---|---|
Definition | PVD (Physical Vapor Deposition) is a vacuum-based thin-film coating process. |
Key Benefits | Corrosion resistance, wear resistance, high-temperature durability. |
Applications | Electronics, optics, home hardware, manufacturing. |
Environmental Impact | Non-toxic, FDA-compliant, and eco-friendly. |
Process | Vaporizes solid material, deposits atom by atom onto a substrate. |
Explore how PVD coating can enhance your products—contact us today!