Physical Vapor Deposition (PVD) is a sophisticated coating process used to deposit thin films of material onto a substrate. It involves transforming a solid material into a vapor phase and then condensing it back into a solid phase on the substrate. The process is carried out in a vacuum chamber and includes steps such as vaporization, migration, and deposition of the coating material. PVD is widely used in industries requiring high precision and durability, such as electronics, optics, and automotive. The process offers advantages like tight tolerances, no excessive build-up, and the ability to replicate the finish of the coating. Common methods include sputtering, thermal evaporation, and eBeam evaporation.
Key Points Explained:
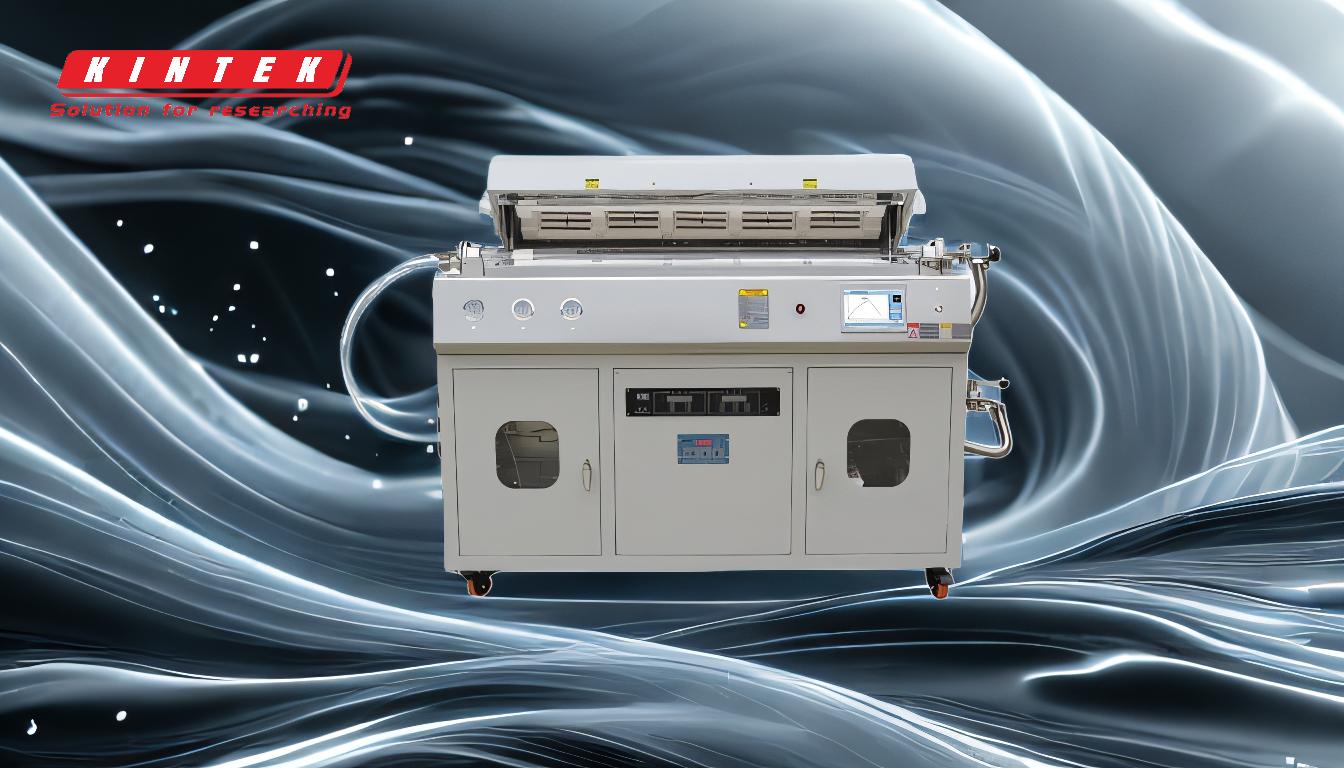
-
Definition and Overview of PVD:
- PVD is a set of deposition methods where a material transitions from a dense state to a vapor phase and then back to a dense phase as a thin film.
- The process is conducted in a vacuum chamber, ensuring a clean and controlled environment for deposition.
-
Main Steps in the PVD Process:
- Vaporization: The coating material is vaporized through methods like evaporation, separation, or sputtering.
- Migration: The vaporized atoms, molecules, or ions migrate towards the substrate, often undergoing reactions during this phase.
- Deposition: The vaporized material condenses onto the substrate, forming a thin film.
-
Detailed Steps in PVD Coating:
- Cleaning the Substrate: The substrate is thoroughly cleaned to remove any contaminants that could affect the coating quality.
- Creating an Electrical Arc: An electrical arc is generated in the vacuum chamber to vaporize and ionize a metal target.
- Combining with Gases: The vaporized metal combines with gases to form a compound.
- Deposition: The compound is deposited atom by atom onto the substrate.
- Testing: Each batch of coated components is tested for consistency using tools like X-ray fluorescent (XRF) machines and spectrophotometers.
-
Temperature and Conditions:
- PVD is processed in a vacuum chamber at temperatures ranging from 320 to 900 degrees Fahrenheit.
- The process uses a 'line of sight' coating method, ensuring a physical bond between the coating and the substrate.
-
Advantages of PVD:
- Wide Range of Materials: PVD can be used with a variety of materials, making it versatile.
- Tight Tolerances: It is recommended for applications requiring precise dimensions.
- No Heat Treatment: PVD does not require post-deposition heat treatment.
- No Excessive Build-Up: The process ensures a uniform and thin coating without excessive build-up.
- Finish Replication: PVD can replicate the finish of the coating material accurately.
-
Common PVD Methods:
- Thermal Evaporation: Uses heat to vaporize the coating material.
- Sputtering: Involves bombarding the target material with ions to eject atoms, which then deposit onto the substrate.
- eBeam Evaporation: Uses an electron beam to vaporize the material.
-
Applications and Importance:
- PVD is crucial in industries requiring durable and precise coatings, such as electronics, optics, and automotive.
- The process is valued for its ability to produce high-quality, consistent coatings with excellent adhesion and durability.
By understanding these key points, one can appreciate the complexity and versatility of the PVD process, making it an essential technique in modern manufacturing and material science.
Summary Table:
Aspect | Details |
---|---|
Definition | PVD transforms solid materials into vapor and deposits them as thin films. |
Main Steps | Vaporization, migration, and deposition. |
Temperature Range | 320 to 900°F in a vacuum chamber. |
Advantages | Tight tolerances, no excessive build-up, finish replication. |
Common Methods | Thermal evaporation, sputtering, eBeam evaporation. |
Applications | Electronics, optics, automotive, and more. |
Discover how PVD processing can enhance your manufacturing process—contact us today for expert guidance!