Physical Vapor Deposition (PVD) is a thin-film coating technique used to deposit materials onto a substrate in a vacuum environment. It involves the physical vaporization of a solid material, which then condenses onto a target surface to form a thin, uniform layer. PVD is widely used across industries to enhance the mechanical, optical, chemical, or electronic properties of materials. It is particularly valued for its ability to improve wear resistance, reduce friction, and provide decorative finishes. The process is versatile, enabling the creation of advanced materials and coatings for applications ranging from semiconductors and solar panels to decorative hardware and aerospace components.
Key Points Explained:
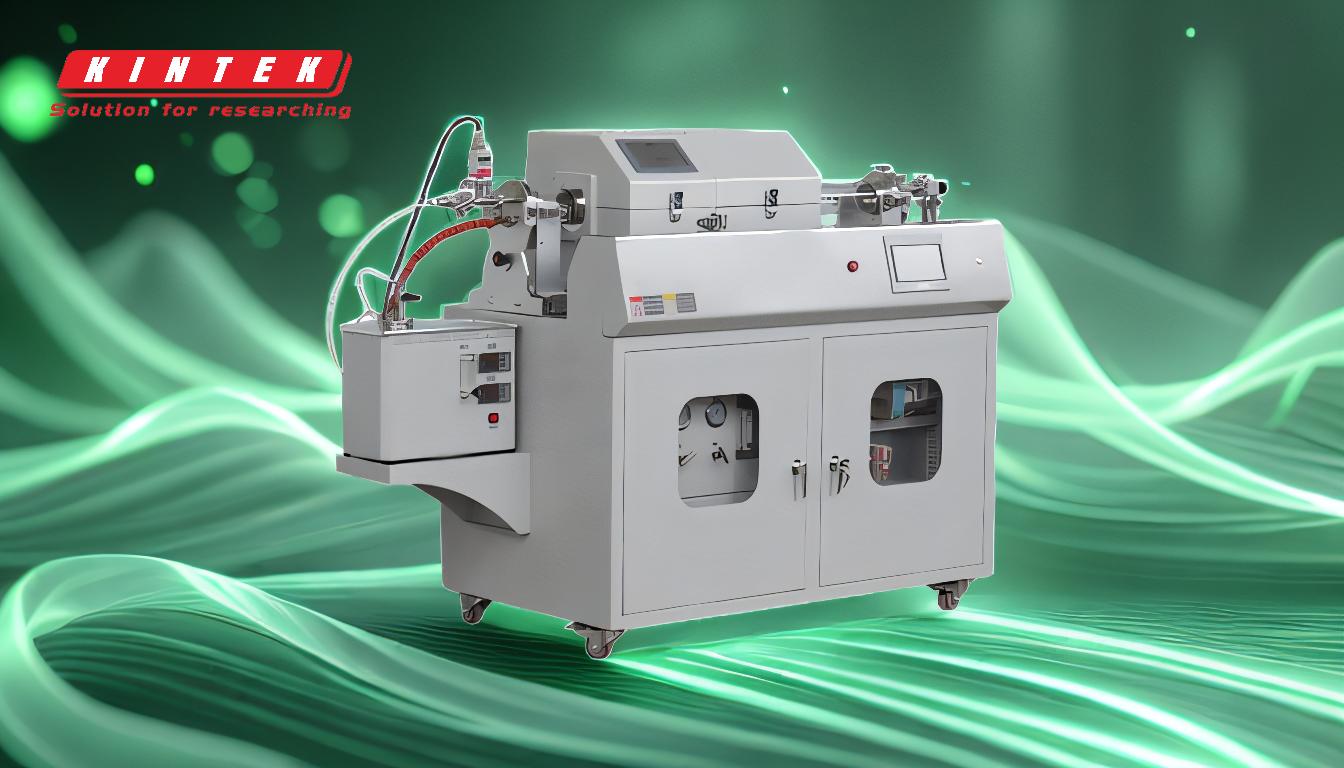
-
Definition and Process of PVD:
- PVD is a vacuum-based coating process where a solid material is vaporized and then deposited onto a substrate to form a thin film.
- The process involves:
- Vaporization: The source material is gasified using methods like evaporation, high-power electricity, or laser ablation.
- Transport: The vaporized material travels through a vacuum or low-pressure environment.
- Condensation: The material condenses on the substrate, forming a thin, uniform layer.
- No chemical reactions occur during PVD, making it a purely physical process.
-
Applications of PVD:
-
Industrial Applications:
- Machining and Tools: PVD coatings, such as titanium nitride, improve wear resistance and extend the life of cutting tools.
- Microelectronics and Semiconductors: PVD is used to deposit thin films for semiconductor devices and integrated circuits.
- Solar Panels: Thin-film solar panels utilize PVD to enhance efficiency and durability.
- Aerospace: PVD coatings improve resistance to high temperatures and ablation in aerospace components.
-
Decorative and Functional Coatings:
- Architectural Glass: PVD coatings provide reflective and energy-efficient properties.
- Jewelry and Hardware: PVD is used for decorative finishes, offering metallic luster and durability.
- Entertainment Electronics: PVD is used in the production of hard drives, CDs, and DVDs.
-
Industrial Applications:
-
Advantages of PVD:
-
Enhanced Material Properties:
- Improves hardness, wear resistance, and oxidation resistance of substrates.
- Reduces friction, making it ideal for moving parts in machinery.
-
Versatility:
- Can deposit a wide range of materials, including metals, alloys, and ceramics.
- Enables the creation of advanced materials with unique properties, such as extended solubilities and fine grain sizes.
-
Aesthetic and Functional Benefits:
- Provides a high-quality metallic finish without the need for polishing.
- Suitable for both functional and decorative applications.
-
Enhanced Material Properties:
-
Materials and Techniques in PVD:
-
Source Materials:
- Pure metals (e.g., titanium, aluminum) and alloys (e.g., Ti–Mg) are commonly used.
- The choice of material depends on the desired properties of the coating.
-
Deposition Techniques:
- Evaporation: The source material is heated until it vaporizes.
- Sputtering: High-energy ions bombard the source material, causing it to eject atoms.
- Laser Ablation: A laser is used to vaporize the source material.
-
Coating Types:
- Single-layer coatings (e.g., titanium nitride for wear resistance).
- Multi-layer coatings for enhanced performance (e.g., alternating layers of different materials).
-
Source Materials:
-
Industries Leveraging PVD:
-
Machining and Manufacturing:
- PVD-coated tools are widely used in cutting, drilling, and forming operations.
-
Electronics:
- PVD is critical for producing thin films in microelectronics and semiconductor devices.
-
Architecture and Design:
- PVD-coated glass and hardware are used in modern buildings for both functional and aesthetic purposes.
-
Jewelry and Decorative Arts:
- PVD provides durable and attractive finishes for jewelry, lamps, and handicrafts.
-
Machining and Manufacturing:
-
Future Trends in PVD:
-
Advanced Alloys and Composites:
- PVD enables the production of experimental alloys with unique properties, such as Ti–Mg, which cannot be made using traditional metallurgy.
-
Sustainability:
- PVD is an environmentally friendly process, as it produces minimal waste and does not involve harmful chemicals.
-
Emerging Applications:
- PVD is being explored for use in energy storage (e.g., batteries) and biomedical devices (e.g., implant coatings).
-
Advanced Alloys and Composites:
In summary, PVD is a versatile and advanced coating technique with wide-ranging applications across industries. Its ability to enhance material properties, provide decorative finishes, and enable the creation of innovative materials makes it a critical technology in modern manufacturing and design.
Summary Table:
Aspect | Details |
---|---|
Process | Vaporization, transport, and condensation in a vacuum environment. |
Applications | Machining tools, microelectronics, solar panels, aerospace, and jewelry. |
Advantages | Improves wear resistance, reduces friction, and offers decorative finishes. |
Materials | Metals (titanium, aluminum), alloys (Ti–Mg), and ceramics. |
Techniques | Evaporation, sputtering, and laser ablation. |
Industries | Manufacturing, electronics, architecture, and decorative arts. |
Future Trends | Advanced alloys, sustainability, and emerging biomedical applications. |
Learn how PVD can transform your products—contact our experts today!