Rolling pressure is a critical parameter in the metal rolling process, referring to the force exerted by the rolls on the metal being rolled. It plays a significant role in determining the final thickness, shape, and mechanical properties of the rolled product. The pressure is influenced by factors such as the material's properties, roll diameter, reduction ratio, and rolling speed. Proper control of rolling pressure ensures efficient deformation, minimizes defects, and optimizes the quality of the output. Understanding and managing rolling pressure is essential for achieving desired product dimensions and mechanical characteristics in industries like steel manufacturing, automotive, and aerospace.
Key Points Explained:
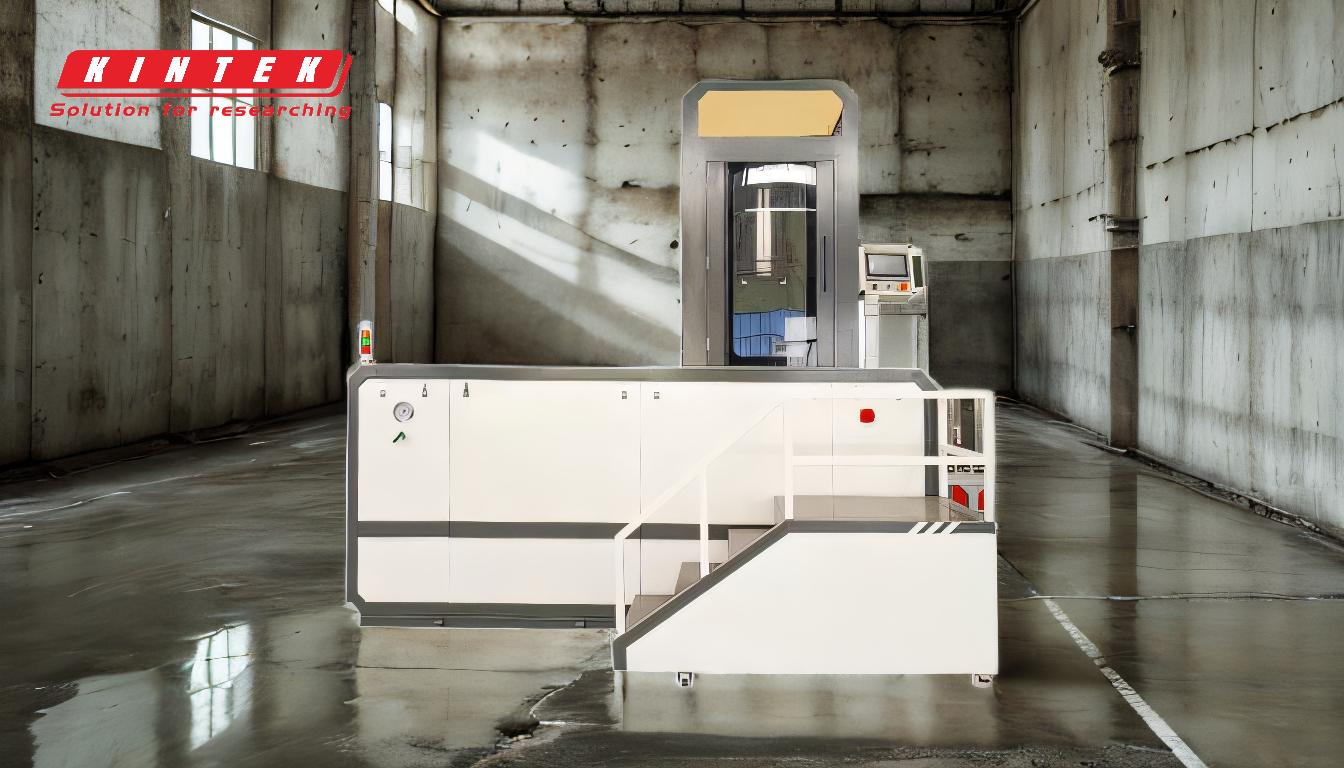
-
Definition of Rolling Pressure:
- Rolling pressure is the force applied by the rolls to deform the metal during the rolling process. It is a measure of the resistance encountered by the rolls as they compress and shape the material. This pressure is distributed over the contact area between the rolls and the metal, influencing the degree of deformation.
-
Factors Influencing Rolling Pressure:
- Material Properties: The hardness, ductility, and yield strength of the metal directly affect the rolling pressure. Harder materials require higher pressure to achieve the same deformation as softer ones.
- Roll Diameter: Larger roll diameters increase the contact area, which can reduce the pressure required for deformation but may also lead to higher friction.
- Reduction Ratio: The ratio of the initial thickness to the final thickness of the metal. Higher reduction ratios typically require higher rolling pressures.
- Rolling Speed: Faster rolling speeds can increase the pressure due to higher frictional forces and strain rates.
-
Importance in the Rolling Process:
- Product Quality: Proper control of rolling pressure ensures uniform thickness, smooth surfaces, and desired mechanical properties in the final product.
- Efficiency: Optimizing rolling pressure minimizes energy consumption and reduces wear on the rolls, enhancing the overall efficiency of the process.
- Defect Prevention: Excessive rolling pressure can cause defects like cracks, while insufficient pressure may result in incomplete deformation.
-
Measurement and Control:
- Rolling pressure is often measured using load cells or pressure sensors integrated into the rolling mill. Advanced control systems adjust the pressure in real-time based on feedback to maintain consistent product quality.
- Techniques like lubrication and roll cooling are employed to manage friction and heat generation, which in turn affects rolling pressure.
-
Applications in Industry:
- Steel Manufacturing: Rolling pressure is crucial in producing sheets, plates, and structural shapes with precise dimensions and mechanical properties.
- Automotive and Aerospace: High-strength alloys used in these industries require precise control of rolling pressure to achieve the desired strength-to-weight ratios.
Understanding rolling pressure is fundamental for optimizing the rolling process, ensuring high-quality output, and minimizing production costs. It bridges the gap between material science and engineering, enabling the creation of advanced materials for modern applications.
Summary Table:
Aspect | Details |
---|---|
Definition | Force applied by rolls to deform metal during rolling. |
Key Factors | Material properties, roll diameter, reduction ratio, rolling speed. |
Importance | Ensures product quality, efficiency, and defect prevention. |
Measurement & Control | Load cells, pressure sensors, real-time adjustments, lubrication, cooling. |
Applications | Steel manufacturing, automotive, aerospace. |
Optimize your metal rolling process with expert insights—contact us today!