Soldering and brazing are both techniques used to create permanent, leak-resistant, and durable joints between materials, particularly metals. While they share similarities, they differ in terms of the temperatures used and the types of materials they can join. Soldering typically involves lower temperatures and is suitable for smaller, more delicate components, while brazing uses higher temperatures and is ideal for stronger, more robust joints. Both methods are widely used in industries such as electronics, plumbing, and automotive manufacturing due to their ability to withstand vibration and shock. Below, we will explore the similarities and differences between soldering, brazing, and other related joining techniques.
Key Points Explained:
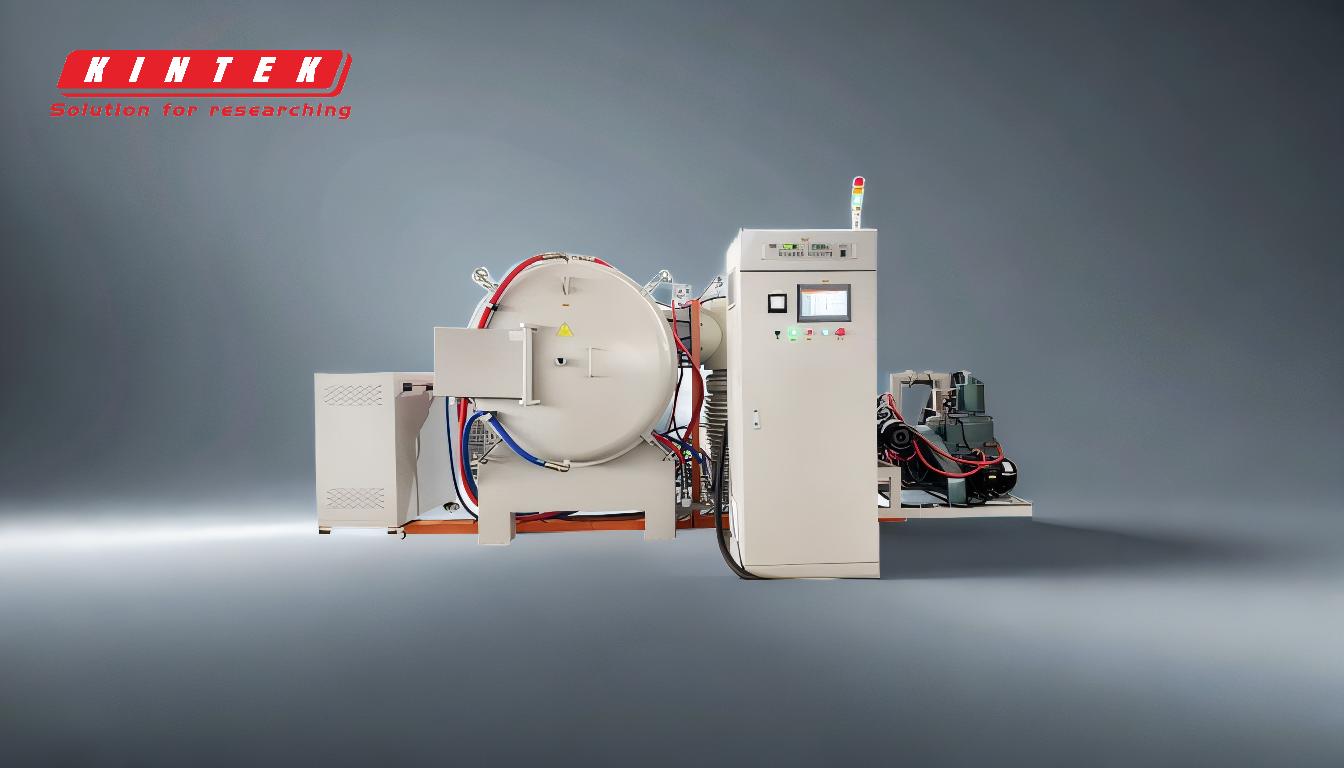
-
Soldering and Brazing: Similarities and Differences
- Similarities: Both soldering and brazing involve joining metals using a filler material that melts at a lower temperature than the base metals. They create strong, leak-proof joints and are widely used in applications requiring precision and durability.
- Differences: Soldering uses filler materials with melting points below 450°C (842°F), making it suitable for delicate work like electronics. Brazing, on the other hand, involves higher temperatures (above 450°C) and stronger filler metals, making it ideal for heavy-duty applications like plumbing and HVAC systems.
-
Other Joining Techniques Similar to Brazing
- Welding: Unlike brazing, welding involves melting the base metals themselves to form a joint. While welding creates stronger bonds, it requires higher temperatures and can distort or weaken the materials.
- Adhesive Bonding: This method uses adhesives to join materials without heat. While it is less durable than brazing, it is suitable for materials that cannot withstand high temperatures.
- Mechanical Fastening: Techniques like riveting or bolting provide strong joints but are less permanent and can introduce stress points compared to brazing.
-
Applications of Brazing and Similar Techniques
- Brazing: Commonly used in HVAC systems, automotive radiators, and plumbing due to its ability to create strong, leak-proof joints.
- Soldering: Ideal for electronics, jewelry making, and small-scale repairs.
- Welding: Used in construction, manufacturing, and heavy machinery where maximum strength is required.
-
Advantages of Brazing Over Other Methods
- Versatility: Brazing can join dissimilar metals, such as copper to steel, which is challenging for welding.
- Precision: The process allows for controlled heat application, minimizing damage to surrounding materials.
- Durability: Brazed joints are resistant to vibration, shock, and thermal stress, making them ideal for demanding environments.
-
Considerations for Choosing a Joining Method
- Material Compatibility: Some materials, like aluminum, require specific techniques (e.g., aluminum brazing) to ensure strong joints.
- Temperature Sensitivity: For heat-sensitive materials, soldering or adhesive bonding may be preferable.
- Joint Strength Requirements: High-stress applications may necessitate welding or brazing over soldering.
By understanding the similarities and differences between brazing, soldering, and other joining techniques, you can select the most appropriate method for your specific application. Each technique has its unique advantages and limitations, making them suitable for different industries and use cases.
Summary Table:
Technique | Temperature Range | Key Applications | Advantages |
---|---|---|---|
Brazing | Above 450°C (842°F) | HVAC, plumbing, automotive radiators | Joins dissimilar metals, durable, precise |
Soldering | Below 450°C (842°F) | Electronics, jewelry, small repairs | Low heat, suitable for delicate components |
Welding | Very high | Construction, heavy machinery | Strongest bonds, high-temperature resistant |
Adhesive Bonding | None | Heat-sensitive materials | No heat required, versatile |
Mechanical Fastening | None | General applications | Strong but less permanent |
Need help choosing the right joining technique for your project? Contact our experts today for tailored solutions!