Sinter-HIP (Sintering-Hot Isostatic Pressing) is an advanced manufacturing process that combines sintering and hot isostatic pressing into a single step. This process is highly efficient as it allows for the creation of a vacuum environment and the application of high pressure simultaneously, which saves time and reduces costs. Sinter-HIP is particularly useful for producing components with consistent geometries, which enhances productivity and reduces manufacturing expenses. This technology is widely used in industries such as aerospace, defense, and electronics, especially for processing super alloys and materials with high melting points like tungsten and molybdenum. The process involves the diffusion of atoms across particle boundaries, fusing them together to form a dense, solid piece without melting the material to the point of liquefaction.
Key Points Explained:
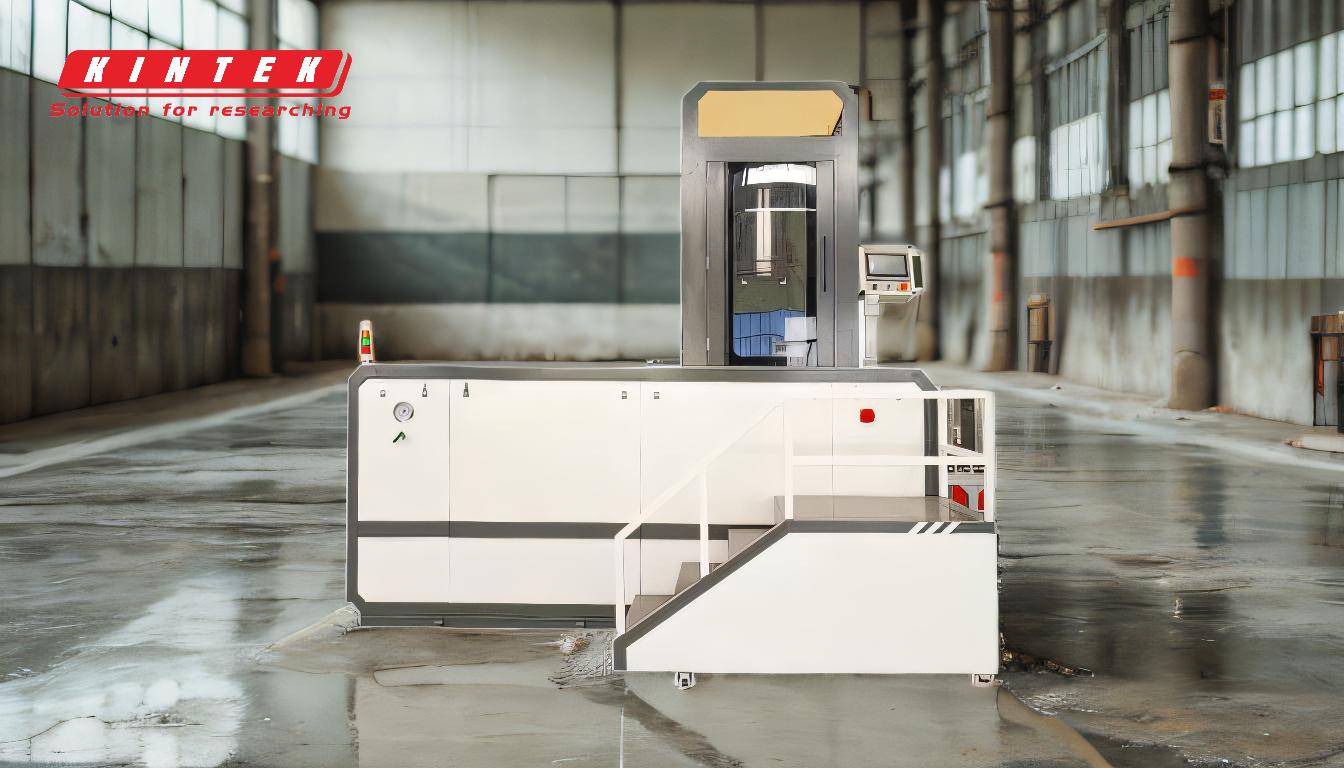
-
Combination of Sintering and Hot Isostatic Pressing:
- Sinter-HIP integrates the sintering process, which compacts and forms a solid mass of material by applying heat or pressure, with hot isostatic pressing (HIP), which applies high pressure uniformly from all directions. This combination allows for the simultaneous application of heat and pressure, leading to a more efficient and cost-effective manufacturing process.
-
Vacuum Environment and High Pressure:
- The ability to create a vacuum environment and apply high pressure at the same time is a key feature of Sinter-HIP. This dual action helps in achieving a high-density, defect-free product with improved mechanical properties. The vacuum environment prevents oxidation and contamination, while the high pressure ensures uniform density and strength throughout the material.
-
Consistent Geometries and Enhanced Productivity:
- Sinter-HIP produces components with consistent geometries, which is crucial for industries that require high precision and reliability. This consistency reduces the need for post-processing and machining, thereby enhancing productivity and reducing overall manufacturing costs.
-
Wide Range of Applications:
- Sinter-HIP is widely used in industries such as aerospace, defense, and electronics. It is particularly beneficial for processing super alloys and materials with extremely high melting points, such as tungsten and molybdenum. These materials are essential for high-performance applications where strength, durability, and resistance to extreme conditions are required.
-
Material Diffusion and Fusion:
- During the Sinter-HIP process, atoms in the materials diffuse across the boundaries of the particles, fusing them together to create a dense, solid piece. This diffusion occurs without melting the material to the point of liquefaction, which is especially important for materials with high melting points. The result is a product with uniform density, improved mechanical properties, and enhanced performance characteristics.
-
Induction Sintering Technology:
- While not directly part of Sinter-HIP, induction sintering technology is relevant as it enhances the bonding of solid particles, particularly in special ceramics. This technology promotes grain growth and the compression of voids, increasing the density and forming a dense polycrystalline sinter. It is increasingly being applied in the research and development of new materials, which could potentially benefit from the Sinter-HIP process.
In summary, Sinter-HIP is a highly efficient and versatile manufacturing process that combines the benefits of sintering and hot isostatic pressing. It is particularly valuable for producing high-performance components in industries that demand precision, reliability, and material integrity. The ability to work with high melting point materials and achieve consistent geometries makes Sinter-HIP a critical technology in modern manufacturing.
Summary Table:
Key Feature | Description |
---|---|
Combination of Processes | Integrates sintering and hot isostatic pressing for simultaneous heat and pressure. |
Vacuum Environment | Prevents oxidation and contamination while ensuring uniform density. |
Consistent Geometries | Produces precise components, reducing post-processing and manufacturing costs. |
Wide Applications | Used in aerospace, defense, and electronics for high-performance materials. |
Material Diffusion | Fuses particles without liquefaction, ideal for high melting point materials. |
Induction Sintering Relevance | Enhances bonding and density in ceramics, complementing Sinter-HIP benefits. |
Interested in leveraging Sinter-HIP for your manufacturing needs? Contact our experts today to learn more!