Sinter temperature refers to the specific temperature range used during the sintering process, where heat is applied to fuse particles together into a solid mass without melting the material. This temperature is critical for achieving desired material properties such as hardness, toughness, and precision. The process involves precise control of heating rates, hold times, and cooling rates to ensure optimal results. Sintering is commonly used for metals, ceramics, and plastics, enabling the production of complex shapes and geometries while combining the properties of multiple materials. The temperature must be carefully managed to avoid issues like overfiring or incomplete sintering, as it directly influences grain boundary diffusion and bulk diffusion.
Key Points Explained:
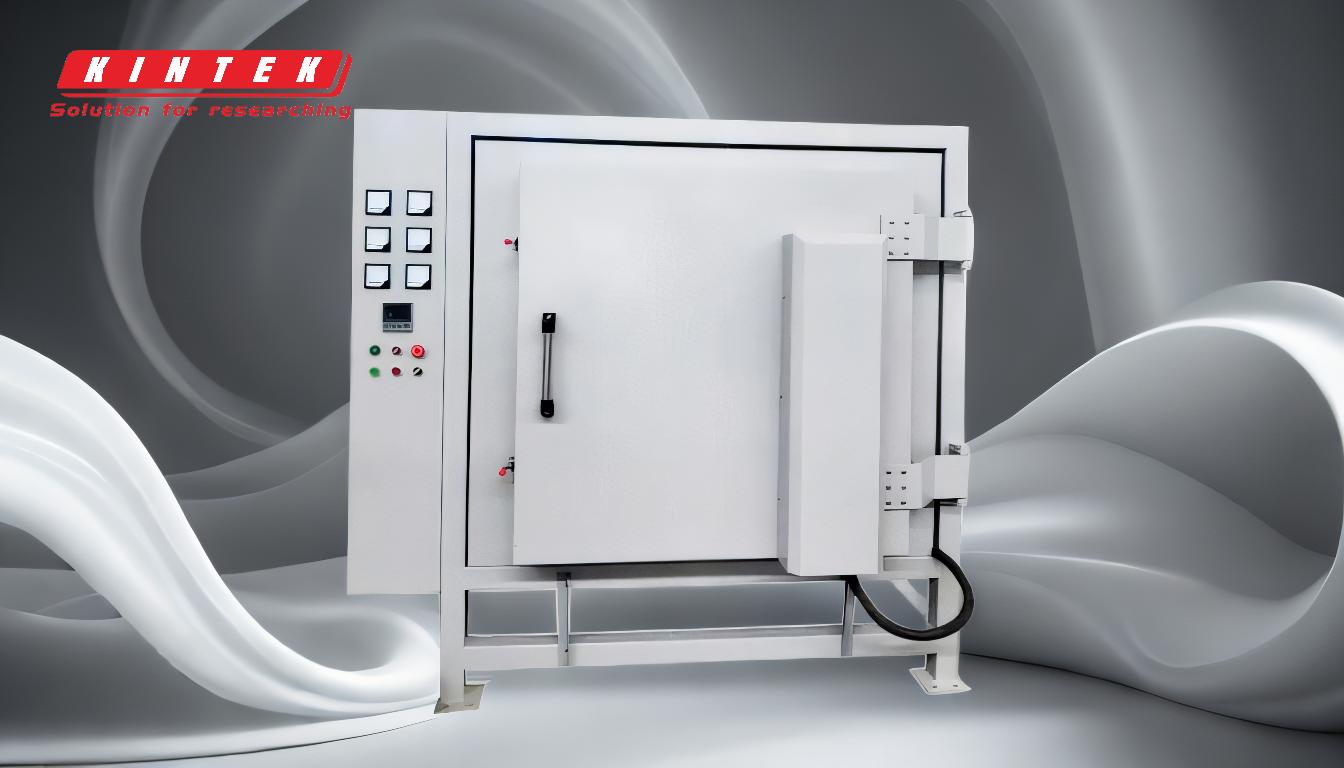
-
Definition of Sinter Temperature:
- Sinter temperature is the specific temperature range used during the sintering process to fuse particles into a solid mass without melting the material. This process involves the application of heat and sometimes pressure to achieve bonding and densification.
-
Importance of Temperature Control:
- Precise temperature control is crucial to preserve the desired material properties, such as small grain size in hard metals. Exceeding the optimal temperature range, such as 1450°C for hard metals, can lead to undesirable grain growth and loss of material properties.
- Temperature control also affects grain boundary diffusion and bulk diffusion, which are essential for achieving the desired density and mechanical properties.
-
Temperature Ranges and Critical Phases:
- From room temperature to 900°C, the temperature has little effect on the restorations. However, the ramp rate from 900°C to the top temperature, the consistency of temperature during the hold time, and the cooling rate back to about 900°C are critical for achieving the best results.
- High temperatures, often reaching several thousand degrees Celsius, promote bonding and diffusion between particles, leading to grain growth and densification.
-
Materials and Applications:
- Sintering is used for a variety of materials, including metals, ceramics, plastics, and other materials. It allows for the production of intricate shapes and geometries that are difficult to achieve with traditional manufacturing methods.
- The process combines the properties of multiple materials, such as toughness and abrasion resistance, and enables lower-cost tooling for complex parts and rapid mass production.
-
Process Parameters and Outcomes:
- The sintering process involves precise control of temperature and pressure to achieve desired material properties and avoid issues like overfiring or incomplete sintering.
- The process is important for producing components with great hardness, toughness, and precision, making it suitable for applications requiring high performance and complex geometries.
-
Benefits of Sintering:
- Sintering merges the properties of multiple materials, combining toughness with abrasion resistance.
- It allows for lower-cost tooling for manufacturing complex parts and enables rapid mass production while retaining precision and repeatability.
By understanding and controlling the sinter temperature, manufacturers can achieve the desired material properties and produce high-quality components with complex geometries and superior performance characteristics.
Summary Table:
Aspect | Details |
---|---|
Definition | Specific temperature range to fuse particles without melting the material. |
Importance | Ensures desired properties like hardness, toughness, and precision. |
Critical Phases | Ramp rate, hold time, and cooling rate between 900°C and top temperature. |
Materials | Metals, ceramics, plastics, and more. |
Applications | Complex shapes, combining material properties, and rapid mass production. |
Benefits | Combines toughness with abrasion resistance; cost-effective for complex parts. |
Optimize your sintering process with precise temperature control—contact our experts today!