Sintering glass is a specialized process that involves heating glass particles or powders to a temperature below their melting point, allowing them to bond and form a solid, dense mass without liquefying. This technique is widely used in various industries, including ceramics, electronics, and optics, to create materials with specific properties such as strength, durability, and transparency. The process relies on the diffusion of atoms across particle boundaries, which fuses the particles together. Sintering glass is particularly useful for materials with high melting points or when precise control over the final product's properties is required.
Key Points Explained:
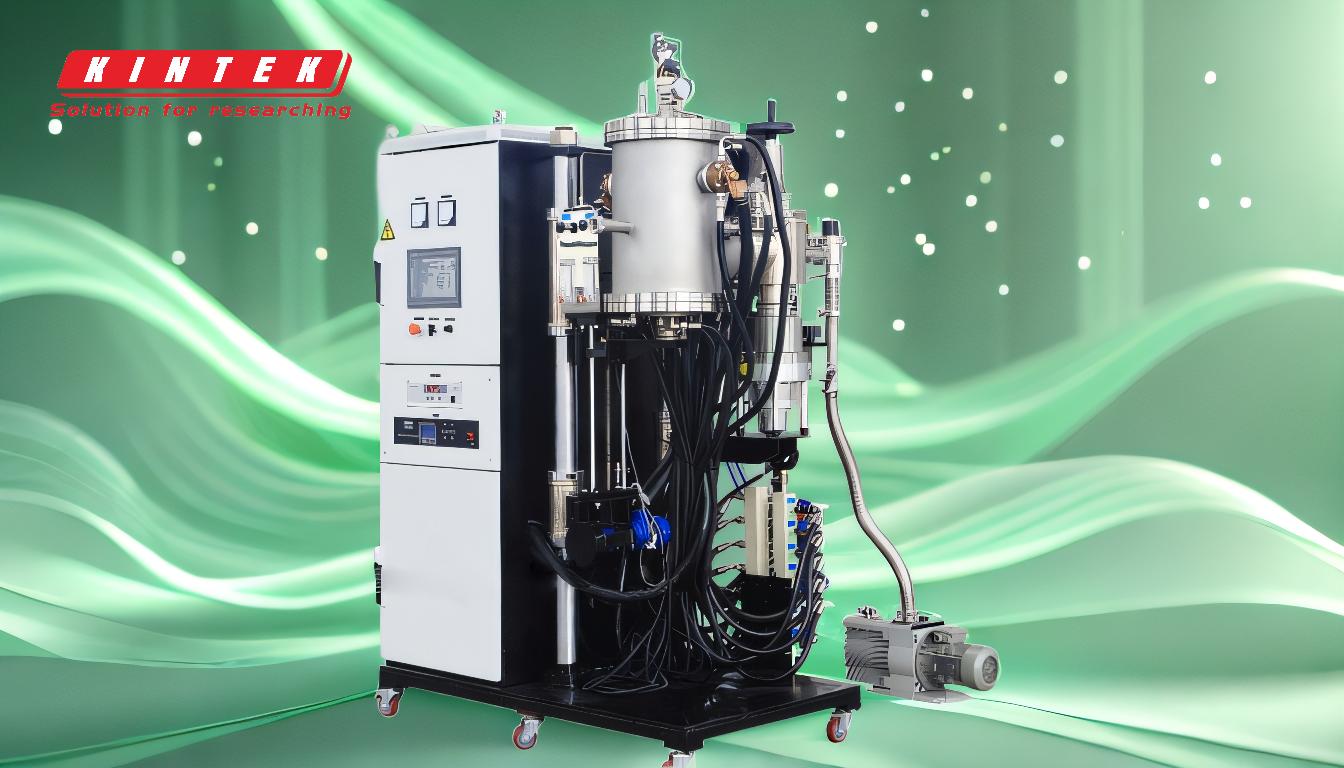
-
Definition of Sintering Glass:
- Sintering glass is the process of heating glass particles or powders to a temperature below their melting point, causing them to bond and form a solid, dense mass.
- Unlike melting, sintering does not involve liquefaction, which allows for better control over the material's properties and structure.
-
Mechanism of Sintering:
- The process relies on the diffusion of atoms across the boundaries of adjacent particles.
- Heat and pressure are applied to encourage the particles to fuse together, creating a cohesive and durable material.
- The temperature used in sintering is always below the melting point of the glass to prevent complete liquefaction.
-
Applications of Sintered Glass:
- Ceramics and Pottery: Sintering is used to create strong and durable ceramic products.
- Electronics: Sintered glass is used in the production of components like insulators and substrates.
- Optics: The process is employed to manufacture lenses and other optical components with precise properties.
- High-Temperature Materials: Sintering is ideal for materials with extremely high melting points, such as tungsten and molybdenum.
-
Advantages of Sintering Glass:
- Control Over Properties: Sintering allows for precise control over the final product's density, strength, and transparency.
- Energy Efficiency: Since the process occurs below the melting point, it requires less energy compared to melting.
- Versatility: Sintering can be applied to a wide range of materials, including metals, ceramics, and plastics.
-
Process Steps:
- Preparation: Glass particles or powders are prepared and often compacted into a desired shape.
- Heating: The material is heated to a specific temperature below its melting point.
- Holding: The material is held at this temperature for a certain period to allow for particle bonding.
- Cooling: The material is cooled to solidify the bonds and achieve the desired properties.
-
Factors Influencing Sintering:
- Temperature: The sintering temperature must be carefully controlled to ensure proper bonding without melting.
- Pressure: Applied pressure can enhance the bonding process, especially in powder metallurgy.
- Particle Size: Smaller particles generally sinter more effectively due to their higher surface area.
- Time: The duration of heating and holding affects the degree of particle bonding and the final material properties.
-
Comparison with Other Processes:
- Melting: Unlike melting, sintering does not involve complete liquefaction, which allows for better control over the material's microstructure.
- Compaction: Sintering often involves compaction, but the primary mechanism is atomic diffusion rather than mechanical bonding.
By understanding these key points, one can appreciate the complexity and versatility of the sintering process, particularly when applied to glass. This method offers significant advantages in terms of material properties and energy efficiency, making it a valuable technique in various industrial applications.
Summary Table:
Aspect | Details |
---|---|
Definition | Heating glass particles below melting point to form a solid, dense mass. |
Mechanism | Diffusion of atoms across particle boundaries under heat and pressure. |
Applications | Ceramics, electronics, optics, and high-temperature materials. |
Advantages | Precise control over properties, energy efficiency, and material versatility. |
Process Steps | Preparation, heating, holding, and cooling. |
Influencing Factors | Temperature, pressure, particle size, and time. |
Comparison | Unlike melting, sintering avoids liquefaction for better microstructure control. |
Ready to explore how sintering glass can enhance your projects? Contact us today for expert guidance!