Sintering in an induction furnace refers to the process of compacting and bonding powder particles into a solid mass by applying heat, typically below the melting point of the material. This process is crucial for forming the furnace lining, which must withstand high temperatures and mechanical stresses during operation. The sintering process in an induction furnace involves three key stages: baking, semi-sintering, and complete sintering. Each stage is carefully controlled to ensure the lining achieves a uniform, durable, and high-performance microstructure. Induction furnaces, with their precise temperature control and uniform heating capabilities, are well-suited for sintering processes, ensuring the lining's integrity and longevity.
Key Points Explained:
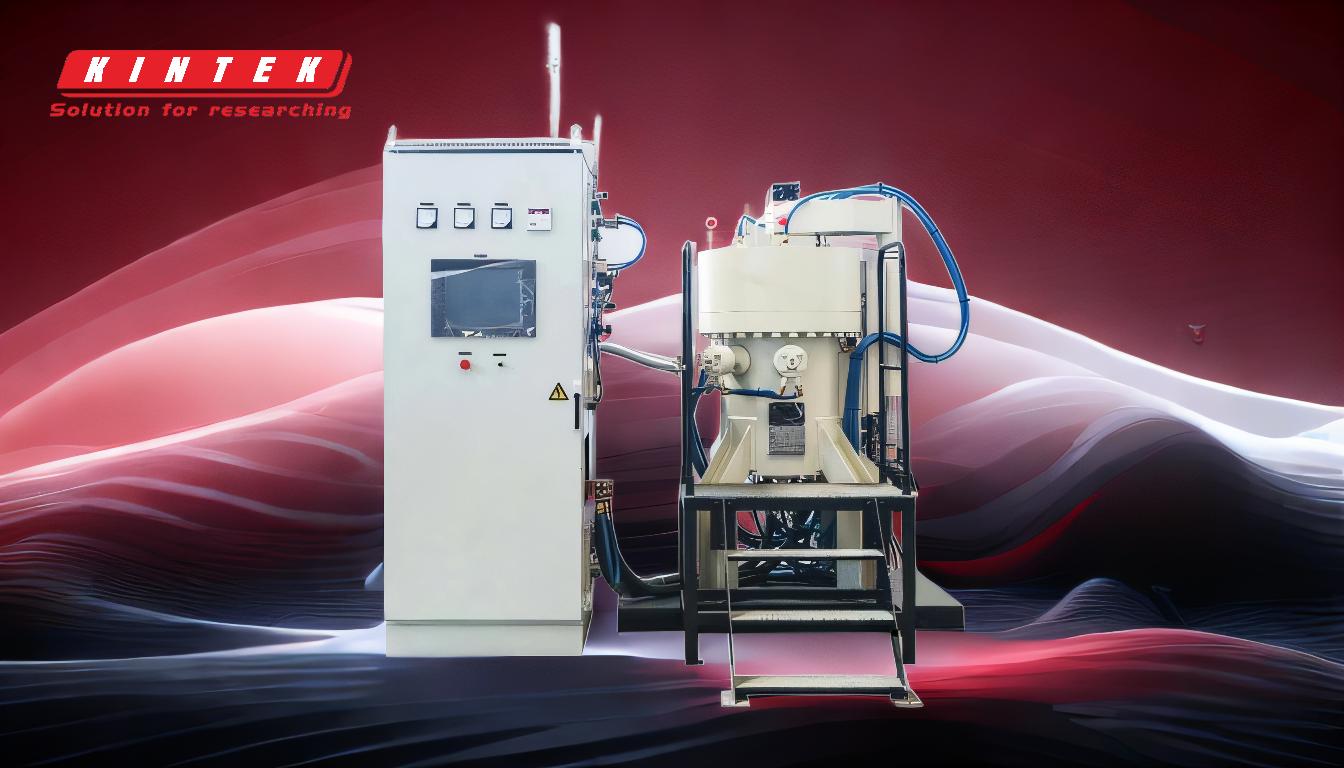
-
Definition of Sintering in Induction Furnaces:
- Sintering is the process of compacting and bonding powder particles into a solid mass using heat, typically below the material's melting point.
- In induction furnaces, sintering is primarily used to form the refractory lining, which must endure high temperatures and mechanical stresses during operation.
-
Stages of the Sintering Process:
-
Baking Stage:
- The furnace lining is heated to around 600°C at a controlled rate.
- This stage removes moisture from the refractory material, preventing cracks and ensuring structural integrity.
-
Semi-Sintering Stage:
- The temperature is increased to 900°C and held for a period.
- Subsequently, the temperature is raised to 1200°C at a faster rate and held again.
- This stage initiates the bonding of particles, forming a semi-solid structure.
-
Complete Sintering Stage:
- The final temperature is adjusted based on the material's properties and the desired lining characteristics.
- This stage ensures the lining achieves a fully bonded, dense, and durable microstructure.
-
Baking Stage:
-
Importance of Sintering for Furnace Linings:
- A well-sintered lining has a three-layer structure, providing optimal thermal and mechanical properties.
- Proper sintering enhances the lining's resistance to thermal shock, erosion, and chemical reactions with molten metals.
- The sintering process directly impacts the lining's service life and overall furnace performance.
-
Role of Induction Furnaces in Sintering:
- Induction furnaces provide precise temperature control and uniform heating, essential for consistent sintering results.
- The electromagnetic field in induction furnaces generates eddy currents, ensuring uniform composition and temperature distribution in the lining material.
- Induction furnaces can reach temperatures up to 1650°C, suitable for sintering a wide range of refractory materials.
-
Advantages of Induction Furnaces for Sintering:
- Uniform Heating: Ensures consistent sintering across the entire lining, reducing the risk of weak spots.
- Energy Efficiency: Induction furnaces are highly efficient, with over 95% effective output power.
- Automation and Control: Advanced control systems allow precise regulation of heating rates, temperatures, and holding times.
- Durability: Induction furnaces are designed for 24-hour continuous operation, making them ideal for industrial sintering processes.
-
Key Process Parameters:
- Temperature Control: Precise regulation of heating rates and holding times is critical for achieving the desired lining properties.
- Material Composition: The chemical composition of the refractory material, especially elements with high oxygen affinity, must be carefully managed.
- Physical Properties: Factors such as melting point, wettability, and surface tension influence the sintering process.
- Purity and Fluidity: Ensuring the purity and fluidity of the molten material during sintering improves the lining's performance.
-
Practical Considerations for Sintering in Induction Furnaces:
- Furnace Design: The furnace must be equipped with a high-quality inductor, power supply, and control system to support the sintering process.
- Lining Materials: The choice of refractory materials and their compatibility with the sintering process is crucial.
- Maintenance: Regular inspection and maintenance of the furnace lining are necessary to ensure long-term performance.
By understanding these key points, equipment and consumable purchasers can make informed decisions about the sintering process in induction furnaces, ensuring optimal performance and longevity of the furnace lining.
Summary Table:
Aspect | Details |
---|---|
Definition | Compacting and bonding powder particles using heat below melting point. |
Key Stages | Baking (600°C), Semi-Sintering (900°C-1200°C), Complete Sintering. |
Importance | Enhances lining durability, thermal shock resistance, and furnace lifespan. |
Advantages | Uniform heating, energy efficiency, precise control, and durability. |
Key Parameters | Temperature control, material composition, physical properties, purity. |
Practical Considerations | Furnace design, lining materials, and regular maintenance. |
Ready to optimize your sintering process? Contact our experts today for tailored solutions!