Spark Plasma Sintering (SPS) is an advanced sintering technique that utilizes pulsed direct current (DC) to rapidly densify powder materials. The process involves applying a pulsed current to the powder particles, which generates localized high temperatures, plasma, and Joule heating. This activation of particle surfaces and internal heating facilitates rapid densification at lower temperatures compared to conventional sintering methods. SPS is known for its ability to produce high-density, high-strength materials with fine microstructures in a short time. Despite its name, research indicates that plasma generation is not a primary mechanism, leading to alternative names like Field Assisted Sintering Technique (FAST) or Direct Current Sintering (DCS). SPS is widely used in advanced materials research, including nanoceramics, magnetic materials, and composites.
Key Points Explained:
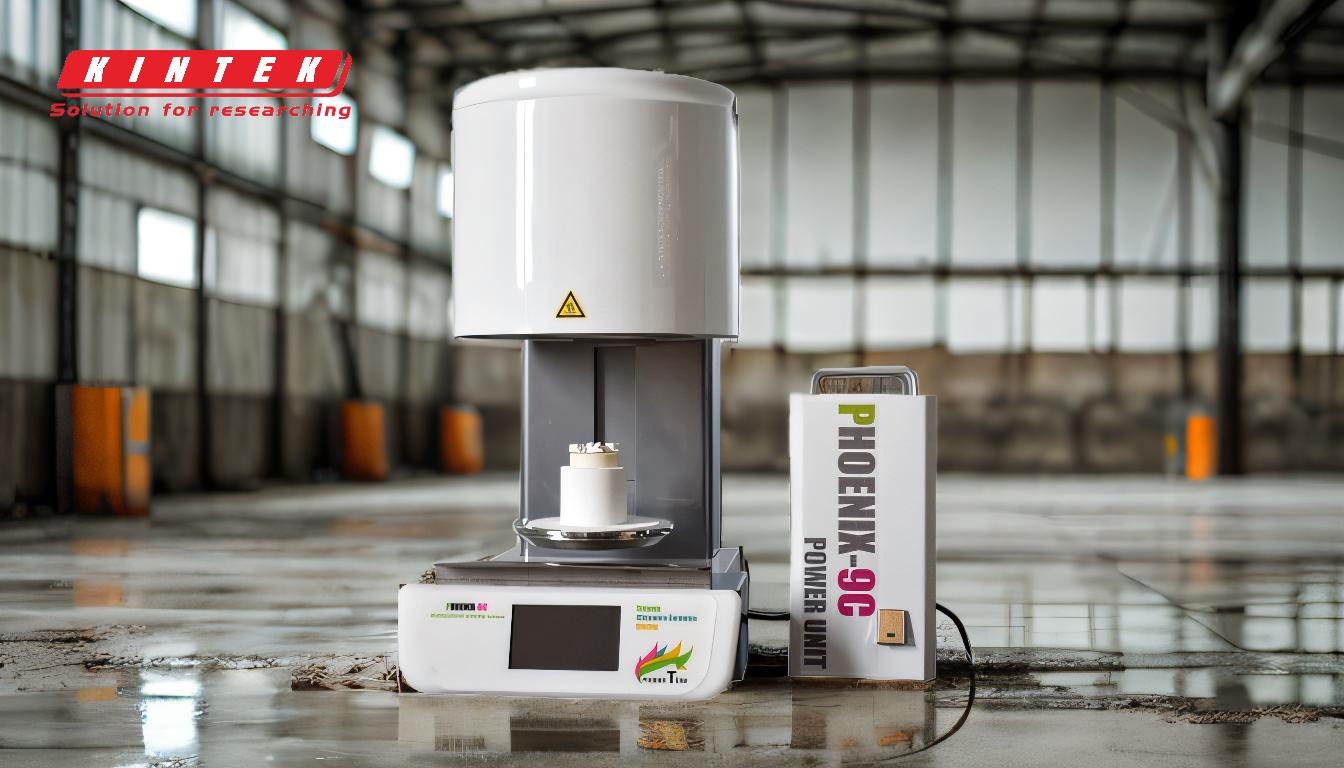
-
Principle of Spark Plasma Sintering (SPS):
- SPS uses a pulsed DC current to generate discharge plasma, Joule heat, and electric field diffusion.
- The pulsed current activates particle surfaces and creates uniform internal heating, enabling rapid densification.
- This process reduces particle gaps and promotes surface and boundary diffusion, leading to strong bonding between particles.
-
Mechanism of Pulsed Current in SPS:
- The pulsed DC current is applied through a conductive die (typically graphite) and, if applicable, through the material itself.
- The die acts as both an external and internal heat source, allowing for rapid heating and cooling rates.
- The instantaneous high current causes localized high temperatures and plasma, which melts particle interfaces and bonds them together.
-
Advantages of SPS:
- Lower Sintering Temperatures: SPS achieves densification at temperatures several hundred degrees lower than conventional methods.
- Shorter Processing Times: The process is significantly faster due to rapid heating and cooling.
- High-Density, High-Strength Materials: SPS produces materials with fine microstructures and minimal porosity.
- Versatility: Suitable for a wide range of materials, including ceramics, metals, and composites.
-
Misconceptions About Plasma in SPS:
- Despite the name, research shows that plasma generation is not a primary mechanism in SPS.
- Alternative names like Field Assisted Sintering Technique (FAST) or Direct Current Sintering (DCS) are more accurate.
- The primary mechanisms are Joule heating and electric field-assisted diffusion.
-
Applications of SPS:
- Magnetic Materials: SPS is used to produce high-performance magnetic materials with controlled microstructures.
- Nanoceramics: The technique is ideal for sintering nanoceramics, preserving their nanoscale features.
- Gradient Functional Materials: SPS enables the creation of materials with graded properties for specialized applications.
- Intermetallic Composites: It is used to sinter intermetallic compounds with enhanced mechanical properties.
-
Historical Development of SPS:
- SPS technology was first proposed in the 1930s but gained practical application in the 1960s in the United States and Japan.
- The first industrial SPS device was developed in Japan in 1988, leading to widespread adoption in advanced materials research.
- SPS is recognized for its speed, low-temperature operation, and energy efficiency.
-
Environmental and Energy Benefits:
- SPS is considered an energy-saving and environmentally friendly technology.
- The process reduces energy consumption and processing time compared to traditional sintering methods.
- Its ability to operate at lower temperatures contributes to reduced carbon emissions.
By combining pulsed current with uniaxial pressure, SPS offers a unique approach to sintering that addresses many limitations of conventional methods. Its ability to produce high-quality materials with fine microstructures in a short time makes it a valuable tool in advanced materials research and industrial applications.
Summary Table:
Key Aspect | Details |
---|---|
Principle | Uses pulsed DC current for plasma, Joule heat, and electric field diffusion. |
Mechanism | Rapid heating and cooling via conductive die; localized high temperatures. |
Advantages | Lower sintering temperatures, shorter processing times, fine microstructures. |
Applications | Magnetic materials, nanoceramics, gradient functional materials, composites. |
Environmental Benefits | Energy-efficient, reduces carbon emissions, and processing time. |
Unlock the potential of Spark Plasma Sintering for your materials research—contact our experts today!