Calcination and roasting are pyrometallurgical processes used in metallurgy to treat metal ores and convert them into more usable forms. Calcination involves heating carbonate ores in the absence or limited supply of air to remove volatile impurities and decompose the ore into its oxide form. Roasting, on the other hand, involves heating sulphide ores in the presence of excess air to convert them into oxides or other compounds, while also removing impurities like sulfur. Both processes aim to purify the ore and prepare it for further reduction or extraction of the pure metal.
Key Points Explained:
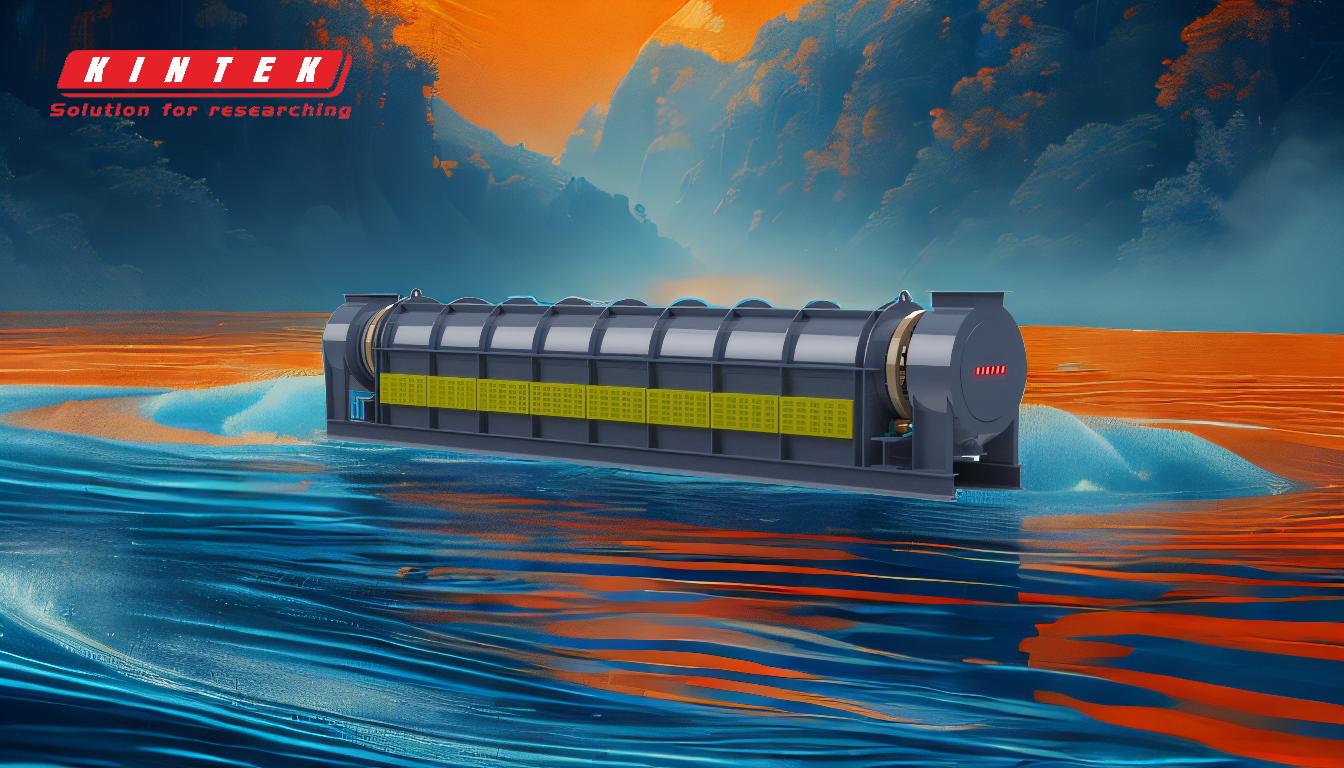
-
Definition and Purpose of Calcination:
- Calcination is a thermal treatment process where carbonate ores are heated in the absence or limited supply of air.
- The primary aim is to remove volatile impurities such as water, carbon dioxide, or organic matter.
- It decomposes the carbonate ore into its oxide form, making it easier to extract the pure metal in subsequent steps.
- Example: Heating limestone (CaCO₃) to produce lime (CaO) and carbon dioxide (CO₂).
-
Definition and Purpose of Roasting:
- Roasting is a thermal treatment process where sulphide ores are heated in the presence of excess air or oxygen.
- The primary aim is to convert sulphide ores into oxides or other compounds, while also removing sulfur as sulfur dioxide (SO₂).
- It helps in eliminating impurities and preparing the ore for further reduction to extract the metal.
- Example: Roasting zinc sulphide (ZnS) to produce zinc oxide (ZnO) and sulfur dioxide (SO₂).
-
Key Differences Between Calcination and Roasting:
- Air Supply: Calcination is performed in the absence or limited supply of air, while roasting requires excess air or oxygen.
- Type of Ores: Calcination is primarily used for carbonate ores, whereas roasting is used for sulphide ores.
- Chemical Reactions: Calcination involves decomposition reactions, while roasting involves oxidation reactions.
- By-products: Calcination releases gases like CO₂, while roasting releases SO₂.
-
Applications in Metallurgy:
- Both processes are essential steps in the extraction of metals like iron, zinc, copper, and aluminum.
- Calcination is used in the production of cement, lime, and other industrial materials.
- Roasting is crucial in the extraction of metals from sulphide ores, such as in the production of zinc, lead, and copper.
-
Importance in Purification and Metal Extraction:
- Calcination and roasting help in removing impurities, which improves the efficiency of subsequent reduction processes.
- They convert ores into more reactive forms (oxides), which are easier to reduce to pure metals using reducing agents like carbon or hydrogen.
- These processes ensure the production of high-purity metals, which are essential for industrial and commercial applications.
By understanding the aims and mechanisms of calcination and roasting, purchasers of equipment and consumables can better select the appropriate materials and technologies for their metallurgical processes.
Summary Table:
Aspect | Calcination | Roasting |
---|---|---|
Air Supply | Absence or limited supply of air | Excess air or oxygen |
Type of Ores | Carbonate ores | Sulphide ores |
Chemical Reactions | Decomposition reactions | Oxidation reactions |
By-products | CO₂, water vapor | SO₂ |
Applications | Cement, lime production | Extraction of zinc, lead, copper |
Discover how calcination and roasting can optimize your metallurgical processes—contact our experts today!