Annealing is a heat treatment process that softens metals, increases ductility, and reduces internal stresses by altering the material's microstructure. It involves heating the material to a specific temperature and then cooling it slowly. However, alternatives to annealing exist, depending on the desired outcome and material properties. These alternatives include processes like normalizing, tempering, stress relieving, and cryogenic treatment, each offering unique benefits such as improved machinability, reduced brittleness, or enhanced mechanical properties. The choice of alternative depends on the specific requirements of the material and its intended application.
Key Points Explained:
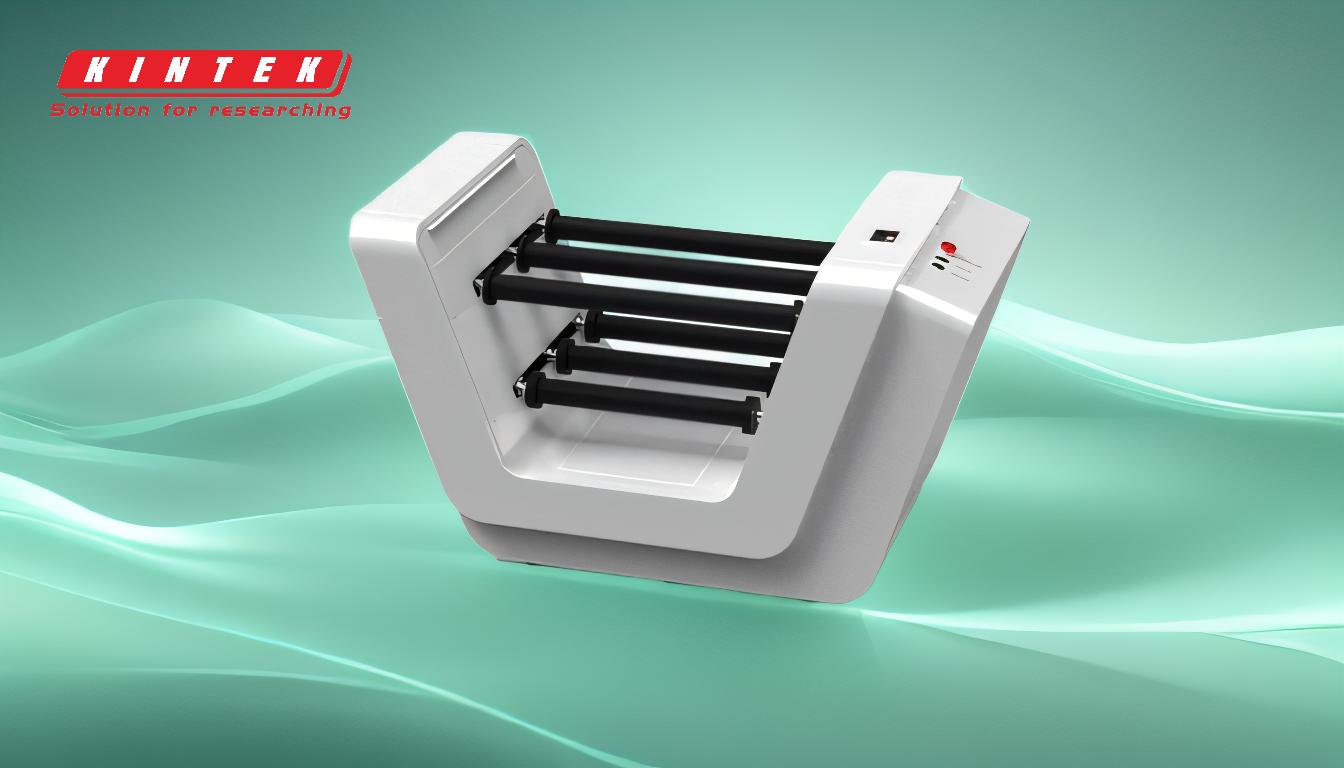
-
Normalizing:
- Normalizing is a heat treatment process similar to annealing but involves cooling the material in air rather than in a furnace. This process refines the grain structure, improves mechanical properties, and enhances uniformity in the material.
- It is often used for steels to achieve a more consistent microstructure and better machinability compared to annealing.
- Normalizing is particularly effective for materials that require improved toughness and strength without the need for the slow cooling associated with annealing.
-
Tempering:
- Tempering is a heat treatment process applied after hardening to reduce brittleness and improve toughness. It involves reheating the material to a temperature below its critical point and then cooling it.
- This process is commonly used for steels and other alloys to achieve a balance between hardness and ductility.
- Tempering is an excellent alternative when the goal is to reduce internal stresses and improve the material's resistance to impact and fatigue.
-
Stress Relieving:
- Stress relieving is a heat treatment process used to reduce internal stresses in a material without significantly altering its microstructure. It involves heating the material to a temperature below its transformation range and then cooling it slowly.
- This process is particularly useful for materials that have undergone welding, machining, or cold working, as it helps to prevent distortion and cracking.
- Stress relieving is a practical alternative when the primary concern is to eliminate residual stresses rather than to soften the material.
-
Cryogenic Treatment:
- Cryogenic treatment involves cooling the material to extremely low temperatures, typically below -150°C, to improve its mechanical properties. This process can enhance wear resistance, reduce residual stresses, and improve dimensional stability.
- It is often used for tool steels and other high-performance materials that require increased durability and longevity.
- Cryogenic treatment is a unique alternative that can complement or replace annealing in applications where enhanced material performance is critical.
-
Cold Working and Work Hardening:
- Cold working involves deforming the material at room temperature to increase its strength and hardness. This process can be an alternative to annealing when the goal is to achieve higher strength without the need for heat treatment.
- Work hardening can be used to improve the mechanical properties of materials like stainless steel and aluminum alloys.
- While cold working increases hardness, it may reduce ductility, so it is essential to balance the process to meet specific material requirements.
-
Quenching and Aging:
- Quenching involves rapidly cooling the material from a high temperature to achieve a hardened state. Aging is a subsequent heat treatment process that enhances the material's strength and stability.
- This combination is often used for aluminum alloys and other non-ferrous metals to achieve high strength and durability.
- Quenching and aging can be an effective alternative to annealing when the goal is to achieve a specific combination of strength and toughness.
In summary, while annealing is a widely used heat treatment process, several alternatives can be employed depending on the desired material properties and application requirements. Each alternative offers unique advantages, and the choice of process should be based on a thorough understanding of the material's characteristics and the intended use.
Summary Table:
Alternative | Key Benefits | Best Use Cases |
---|---|---|
Normalizing | Refines grain structure, improves toughness, and enhances uniformity. | Steels requiring consistent microstructure and better machinability. |
Tempering | Reduces brittleness, improves toughness, and balances hardness and ductility. | Steels and alloys needing impact and fatigue resistance. |
Stress Relieving | Reduces internal stresses without altering microstructure. | Welded, machined, or cold-worked materials to prevent distortion and cracking. |
Cryogenic Treatment | Enhances wear resistance, reduces residual stresses, and improves stability. | Tool steels and high-performance materials requiring durability. |
Cold Working | Increases strength and hardness at room temperature. | Stainless steel and aluminum alloys needing higher strength. |
Quenching and Aging | Achieves high strength and durability through rapid cooling and heat treatment. | Aluminum alloys and non-ferrous metals requiring specific strength and toughness. |
Need help choosing the right heat treatment process for your materials? Contact our experts today for personalized advice!