Heat treatment is a critical process used across various industries to enhance the physical and mechanical properties of materials, primarily metals. It involves controlled heating and cooling to alter a material's structure, improving properties such as strength, hardness, ductility, and wear resistance. This process is essential in industries like aerospace, automotive, tooling, healthcare, and energy, where precision-engineered components must meet stringent performance standards. Heat treatment methods such as through-hardening, case hardening, annealing, and brazing are employed to prepare parts for demanding applications, ensuring durability and reliability. Vacuum and controlled atmosphere heat treatments are particularly valuable for minimizing distortions and achieving high-quality results in industries requiring intricate designs and superior material performance.
Key Points Explained:
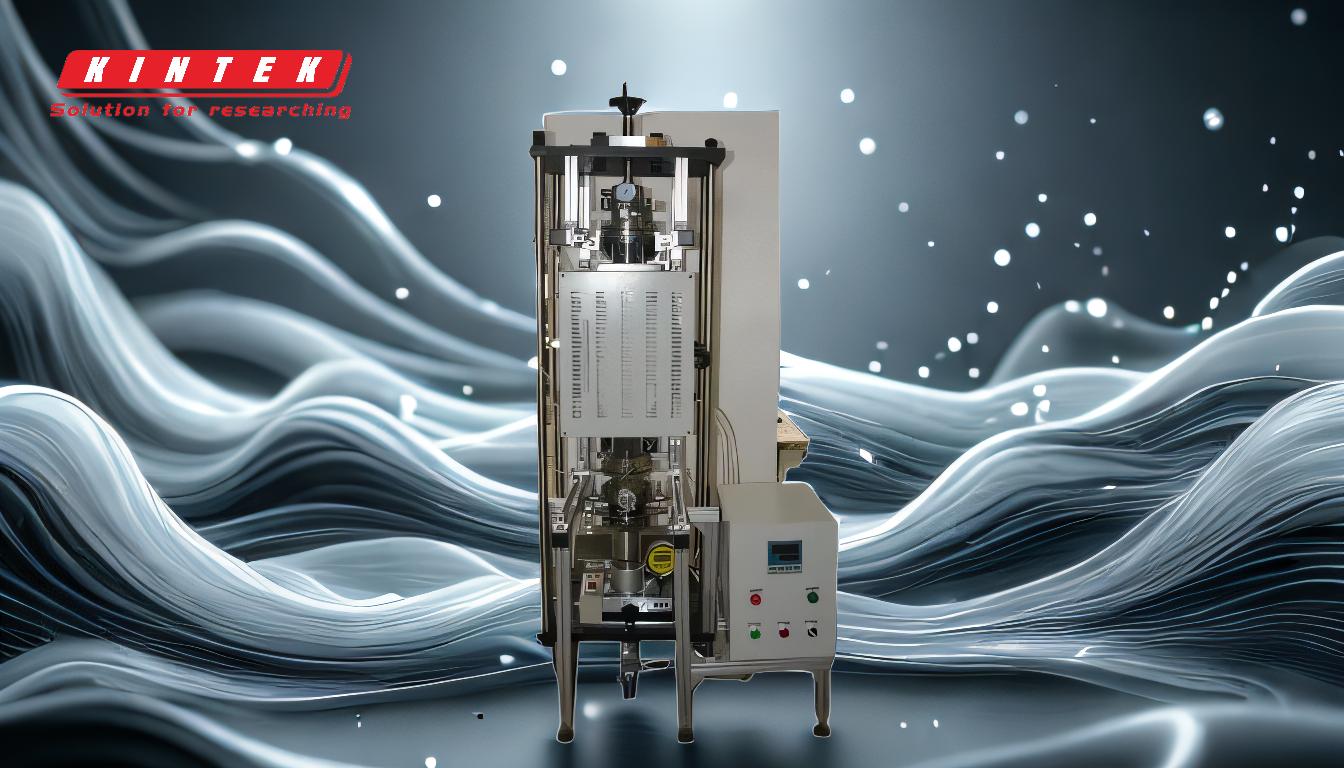
-
Purpose of Heat Treatment:
- Heat treatment is used to alter or strengthen the structure of materials through controlled heating and cooling processes.
- It improves physical properties such as strength, ductility, hardness, and wear resistance, making materials suitable for demanding industrial applications.
- Both ferrous (iron-based) and non-ferrous metals (e.g., aluminum, copper) can undergo heat treatment to enhance their performance.
-
Common Heat Treatment Processes:
- Through-Hardening: Involves heating the material to a high temperature and then cooling it rapidly to achieve uniform hardness throughout the part.
- Case Hardening: Hardens only the surface layer of the material while maintaining a softer, more ductile core, ideal for components requiring wear resistance and toughness.
- Annealing: Softens the material by heating it and then slowly cooling it, improving ductility and reducing internal stresses.
- Brazing: Joins two or more metal parts by melting a filler metal into the joint, often used in applications requiring strong, leak-proof bonds.
-
Applications in Key Industries:
- Aerospace and Aviation: Heat-treated components such as turbine blades, landing gear, and structural parts must withstand extreme temperatures and stresses. Vacuum heat treatment is particularly beneficial for minimizing distortions and ensuring high-quality results.
- Automotive: Critical parts like gears, axles, camshafts, and crankshafts require heat treatment to enhance durability and performance under high loads and wear conditions.
- Tooling and Cutting Tools: Tools such as saws, axes, and cutting tools are heat-treated to achieve the necessary hardness and wear resistance for efficient operation.
- Healthcare and Electronics: Precision components in medical devices and electronics often undergo heat treatment to ensure reliability and longevity.
- Energy and Oil & Gas: Heat-treated parts are essential for equipment used in harsh environments, such as drilling tools and pipelines, where strength and corrosion resistance are critical.
-
Advantages of Vacuum and Controlled Atmosphere Heat Treatment:
- Vacuum Heat Treatment: Eliminates oxidation and contamination, making it ideal for industries like aerospace and automotive that require precision-engineered components with minimal distortions and superior surface quality.
- Controlled Atmosphere Heat Treatment: Provides exceptional advantages in heating steel parts, ensuring consistent results and improved material properties for industries such as laboratories, universities, and mechanics.
-
Examples of Heat-Treated Components:
- Bearings and Gears: Heat-treated to withstand high loads and reduce friction.
- Fasteners and Axles: Enhanced for strength and durability in automotive and machinery applications.
- Camshafts and Crankshafts: Critical for engine performance, requiring precise heat treatment to ensure reliability.
-
Importance in Modern Manufacturing:
- Heat treatment is indispensable for producing high-performance components that meet the rigorous demands of modern industries.
- It enables the creation of materials with tailored properties, ensuring that parts can perform reliably under specific operating conditions.
By understanding the applications and benefits of heat treatment, industries can optimize the performance and longevity of their components, ensuring they meet the highest standards of quality and reliability.
Summary Table:
Key Aspect | Details |
---|---|
Purpose | Improves strength, hardness, ductility, and wear resistance of materials. |
Common Processes | Through-hardening, case hardening, annealing, and brazing. |
Key Industries | Aerospace, automotive, tooling, healthcare, energy, and oil & gas. |
Advantages | Minimizes distortions, enhances durability, and ensures high-quality results. |
Examples of Components | Bearings, gears, fasteners, axles, camshafts, and crankshafts. |
Optimize your industrial components with expert heat treatment solutions—contact us today!