The basic process of heat treatment involves three fundamental steps: heating, soaking, and cooling. These steps are carefully controlled to alter the physical and sometimes chemical properties of a material, typically metals or plastics. Heating involves raising the material to a specific temperature, which can range up to 2,400°F depending on the material and desired outcome. Soaking ensures the material maintains this temperature for a set duration, allowing for uniform structural changes. Cooling is then conducted according to specific methods to achieve the desired properties, such as hardness, softness, or stress relief. Heat treatment is used for various purposes, including hardening, softening, stress relief, and altering magnetic properties.
Key Points Explained:
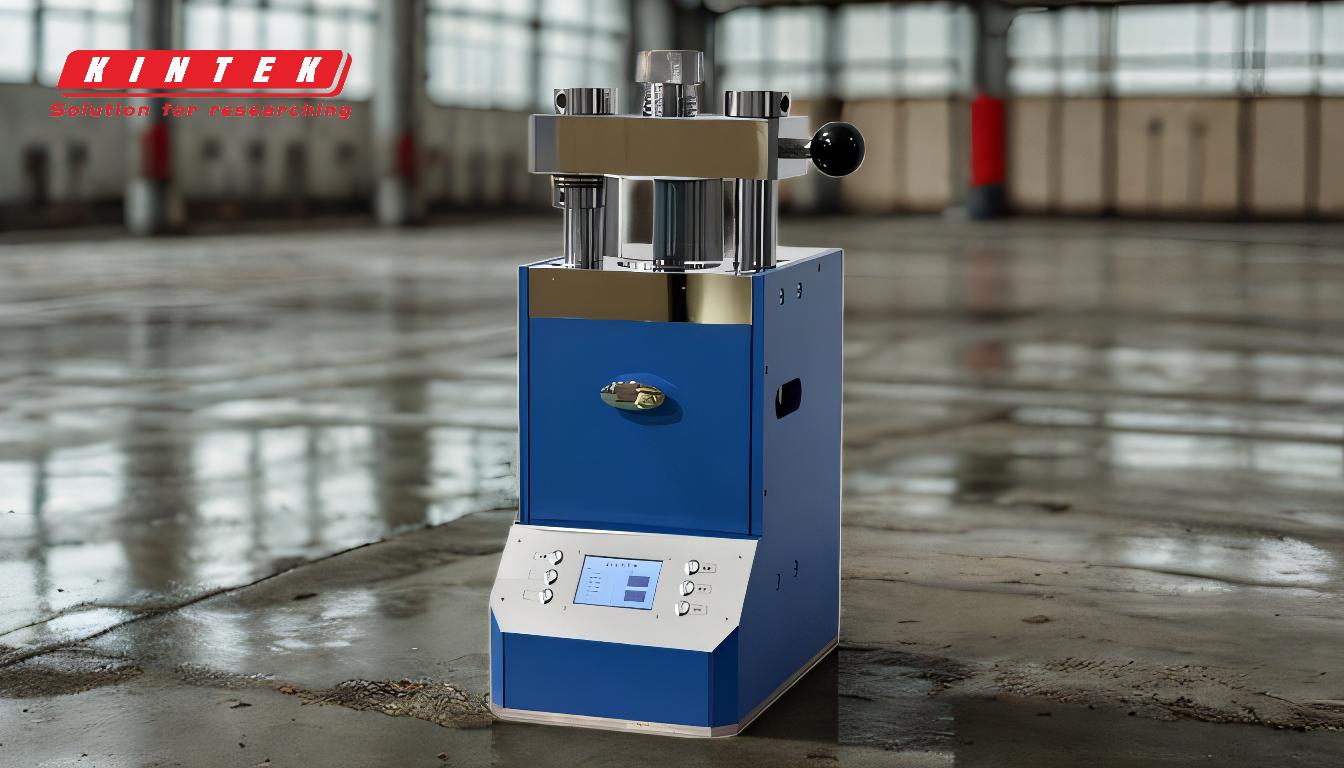
-
Heating:
- Purpose: The first step in heat treatment involves heating the material to a specified temperature. This temperature is critical as it determines the structural changes that will occur in the material.
- Temperature Range: Depending on the material and the desired outcome, temperatures can range from relatively low to as high as 2,400°F.
- Importance: Proper heating ensures the material reaches a state where its internal structure can be altered uniformly. Inadequate heating can lead to uneven structural changes, resulting in inconsistent material properties.
-
Soaking:
- Purpose: Soaking involves maintaining the material at the specified temperature for a set period. This step ensures that the entire material reaches a uniform temperature and allows for the desired internal structural changes to occur.
- Duration: The soaking time can vary significantly, from a few seconds to 60 hours or more, depending on the material and the specific heat treatment process.
- Importance: Soaking is crucial for achieving homogeneity in the material's structure. Without adequate soaking, the material may not achieve the desired properties, leading to potential weaknesses or inconsistencies.
-
Cooling:
- Purpose: The final step in heat treatment is cooling the material according to prescribed methods. The cooling rate and method are critical in determining the final properties of the material.
- Methods: Cooling can be done through various methods, including air cooling, oil quenching, water quenching, or furnace cooling. Each method has a different effect on the material's properties.
- Importance: The cooling process locks in the structural changes achieved during heating and soaking. Improper cooling can lead to issues such as cracking, warping, or the material not achieving the desired hardness or softness.
-
Applications of Heat Treatment:
- Softening (Annealing): Heat treatment can be used to soften metals or plastics, making them easier to machine or form.
- Hardening: Processes like through hardening, case hardening, carburizing, and nitriding are used to increase the hardness of metals.
- Localized Hardening/Softening: Techniques such as induction and flame hardening allow for the hardening or softening of specific areas on a part.
- Stress Relief: Heat treatment can remove internal stresses from materials, which is particularly important after machining, forming, or bending.
- Resilience: Processes like austempering and marquenching can add resilience or springiness to metals.
- Magnetic Properties: Heat treatment can also be used to alter the magnetic permeability of materials, as seen in magnetic anneal or mu metal anneal processes.
-
Importance of Control:
- Temperature Control: Precise control of heating and cooling temperatures is essential to achieve the desired material properties.
- Time Control: The duration of heating and soaking must be carefully managed to ensure uniform structural changes.
- Cooling Rate: The rate at which the material is cooled can significantly impact its final properties, making it a critical factor in the heat treatment process.
In summary, heat treatment is a controlled process that involves heating, soaking, and cooling materials to achieve specific properties. The process is versatile, with applications ranging from hardening and softening metals to stress relief and altering magnetic properties. Proper control of temperature, time, and cooling methods is essential to achieve the desired outcomes in heat treatment.
Summary Table:
Step | Purpose | Key Details |
---|---|---|
Heating | Raise material to a specific temperature for structural changes. | Temperature range: up to 2,400°F; ensures uniform internal structure. |
Soaking | Maintain temperature to allow uniform structural changes. | Duration: seconds to 60+ hours; critical for homogeneity. |
Cooling | Cool material to lock in structural changes. | Methods: air, oil, water, or furnace cooling; impacts final properties like hardness or softness. |
Applications | Alter material properties for hardening, softening, stress relief, and more. | Includes annealing, hardening, localized treatments, and magnetic property adjustments. |
Need expert guidance on heat treatment processes? Contact us today for tailored solutions!