The best braze for aluminum depends on the specific application and the brazing method used. In vacuum brazing, the process relies on the thermal expansion differences between aluminum and its oxide layer to allow the brazing alloy to penetrate and bond with the base material. This method is particularly effective in industries like semiconductor and aerospace, where precision and reliability are critical. Key considerations include the brazing alloy's composition, the vacuum environment, and the use of getter materials to prevent oxidation.
Key Points Explained:
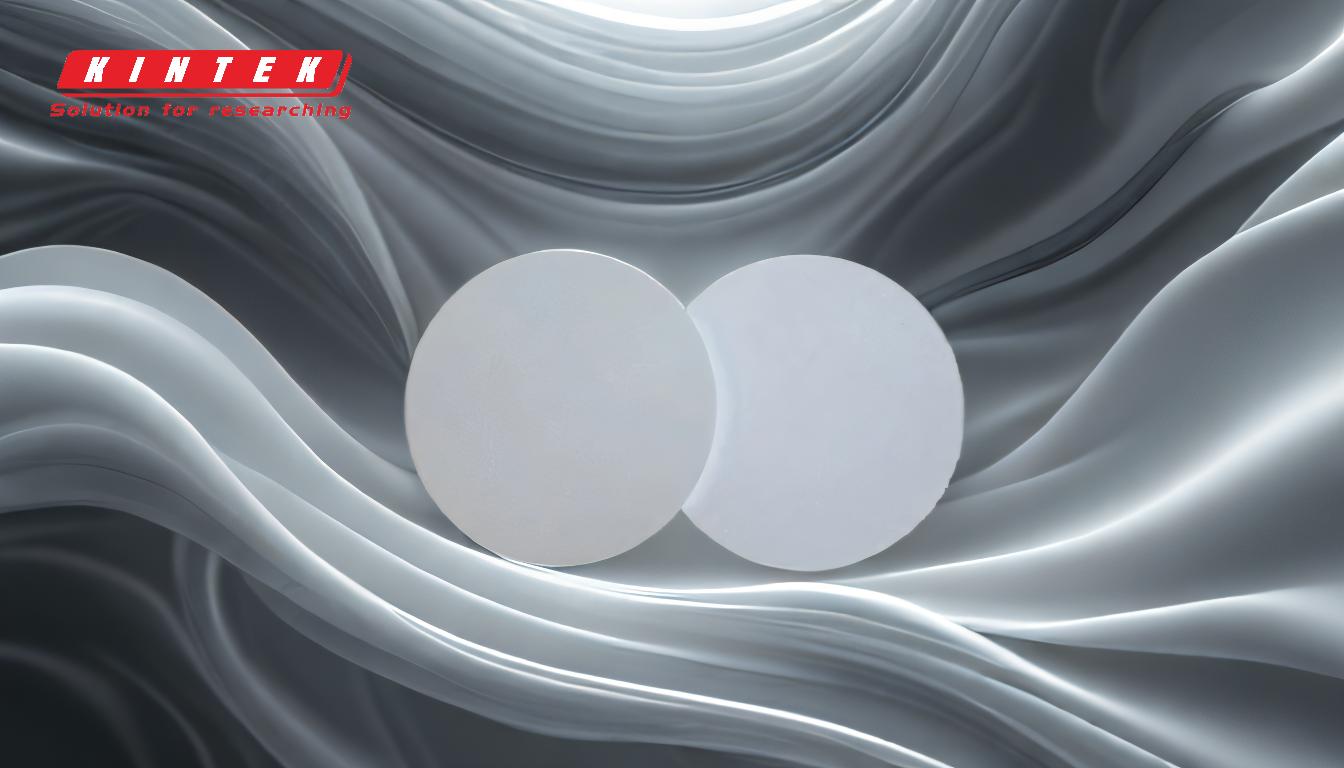
-
Understanding the Role of Aluminum Oxide in Brazing:
- Aluminum naturally forms an oxide layer that is challenging to remove during brazing. In vacuum brazing, this layer is not removed by the vacuum itself but by the thermal expansion differences between aluminum and its oxide. When heated, the oxide layer cracks, allowing the liquid brazing alloy to flow through and bond with the base material.
- This process is critical for ensuring a strong and reliable bond, especially in high-performance applications.
-
Importance of Vacuum Environment:
- A vacuum environment is essential for preventing oxidation during the brazing process. Maintaining a vacuum of at least 10^-4 mbar ensures that the aluminum surface remains clean and free from contaminants.
- Getter materials are often used in vacuum brazing to scavenge any remaining oxygen atoms, further enhancing the quality of the brazed joint.
-
Brazing Alloys for Aluminum:
- The choice of brazing alloy is crucial for achieving optimal results. Common alloys for aluminum brazing include aluminum-silicon (Al-Si) alloys, which have a lower melting point than pure aluminum and provide excellent wetting and flow characteristics.
- The specific alloy composition should be selected based on the application requirements, such as strength, corrosion resistance, and thermal conductivity.
-
Applications in High-Tech Industries:
- Aluminum brazing is widely used in industries like semiconductor manufacturing and aerospace, where precision and reliability are paramount. In these applications, the brazing process must produce joints that can withstand extreme conditions, including high temperatures and mechanical stress.
- The ability to create strong, leak-tight joints makes vacuum brazing particularly suitable for these demanding environments.
-
Process Considerations:
- Temperature control is critical in aluminum brazing. The brazing alloy must reach its melting point without overheating the base material, which could lead to distortion or weakening of the joint.
- Proper cleaning and preparation of the aluminum surfaces are also essential to ensure good wetting and adhesion of the brazing alloy.
By carefully considering these factors, you can select the best braze for aluminum that meets the specific needs of your application, ensuring strong, durable, and reliable joints.
Summary Table:
Key Factor | Details |
---|---|
Role of Aluminum Oxide | Oxide layer cracks under heat, allowing brazing alloy to bond with aluminum. |
Vacuum Environment | Maintains cleanliness, prevents oxidation (10^-4 mbar or better). |
Brazing Alloys | Al-Si alloys preferred for wetting, flow, and lower melting points. |
Applications | Aerospace, semiconductor industries for precision and reliability. |
Process Considerations | Temperature control, surface cleaning, and preparation are critical. |
Need help selecting the best braze for your aluminum application? Contact our experts today for tailored solutions!