PVD (Physical Vapor Deposition) coatings are composed of a variety of materials, including metals, alloys, ceramics, and reactive gases, which are combined to create customized coatings with specific properties. The primary components of PVD coatings include metals such as titanium, chromium, tungsten, aluminum, and zirconium, which are often combined with reactive gases like nitrogen, oxygen, or carbon-based gases to form compounds such as nitrides, carbides, and carbonitrides. These coatings are applied to substrates like metals, plastics, glass, and ceramics, and are tailored to meet the requirements of various industries, including aerospace, automotive, electronics, and decorative applications. The process involves converting solid materials into vapor, which then condenses onto the substrate, forming a strong, durable bond.
Key Points Explained:
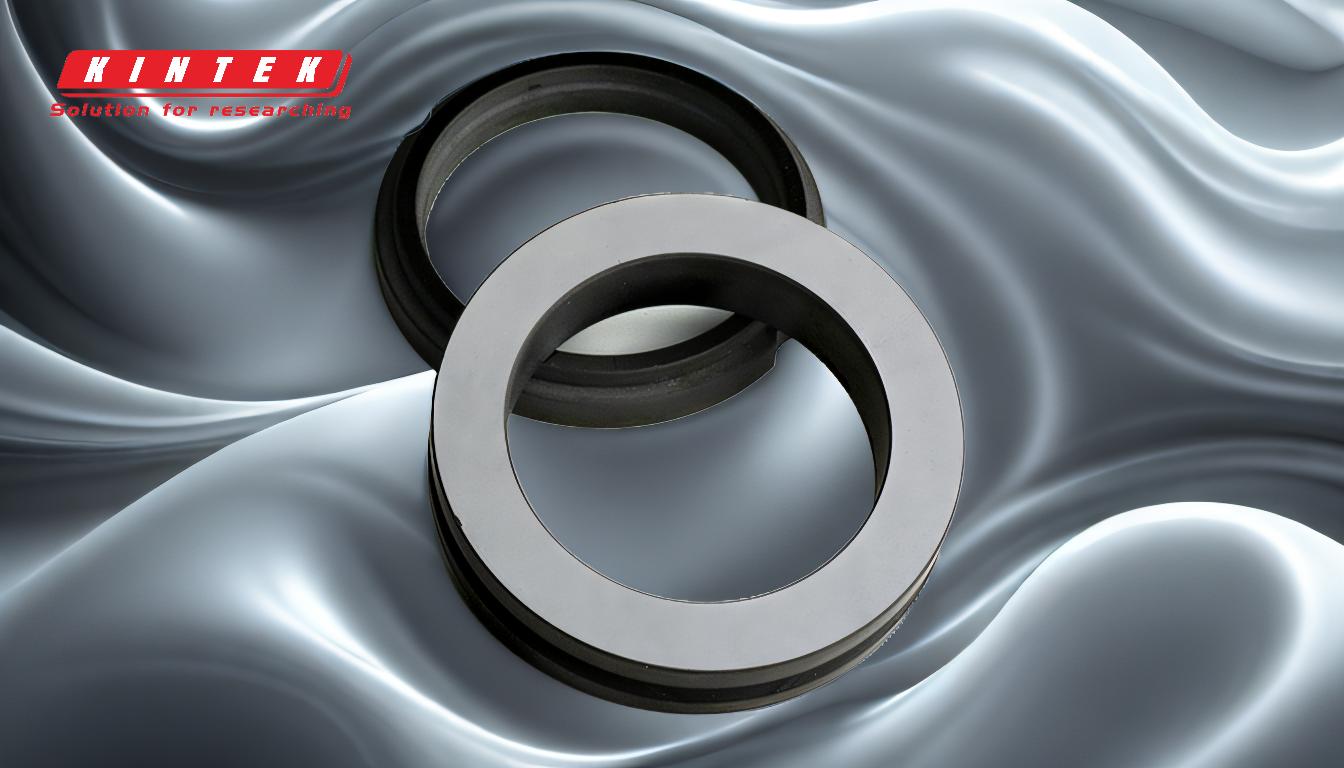
-
Primary Metals Used in PVD Coatings:
- Titanium (Ti): Commonly used to form titanium nitride (TiN), a hard, wear-resistant coating often used in tools, decorative applications, and industrial components.
- Chromium (Cr): Forms chromium nitride (CrN), which is known for its corrosion resistance and is used in applications like watch coatings and machine parts.
- Aluminum (Al): Often combined with chromium to form AlCr coatings, which are used to extend the life of tools and machine parts.
- Zirconium (Zr): Used in specialized coatings for its high-temperature stability and wear resistance.
- Tungsten (W): Typically used in high-performance applications due to its hardness and thermal stability.
-
Reactive Gases and Compounds:
- Nitrogen (N₂): Reacts with metals to form nitrides (e.g., TiN, CrN), which are hard, wear-resistant, and often used in cutting tools and decorative coatings.
- Oxygen (O₂): Used to create oxides (e.g., SiO₂), which are often used in optical and electronic applications.
- Carbon-based Gases (e.g., Acetylene): Reacts with metals to form carbides (e.g., TiC, WC) and diamond-like carbon (DLC) coatings, which are known for their low friction and high hardness.
- Hydrocarbons: Used to create carbonitrides, which combine the properties of carbides and nitrides for enhanced performance.
-
Common PVD Coating Materials:
- Titanium Nitride (TiN): A gold-colored coating widely used for decorative purposes, cutting tools, and wear-resistant surfaces.
- Chromium Nitride (CrN): A silver-colored coating known for its corrosion resistance and used in watch coatings and machine parts.
- Zinc Tin Oxide (ZnSn): An optical coating used in low-emissivity (low-e) windows and glass.
- Aluminum Chromium (AlCr): Used to extend the service life of tools and machine parts.
- Indium Tin Oxide (ITO): A transparent, conductive coating used in LCDs, plasma displays, and touch panels.
-
Substrates for PVD Coatings:
- PVD coatings can be applied to a wide range of substrates, including:
- Metals: Stainless steel, aluminum, and titanium.
- Plastics: Nylon and other polymers.
- Ceramics: Used in high-temperature and wear-resistant applications.
- Glass: Used in optical and decorative applications.
- PVD coatings can be applied to a wide range of substrates, including:
-
PVD Coating Process:
- The PVD process involves converting a solid material (the target) into vapor, which then condenses onto the substrate (the workpiece). This is typically done in a vacuum chamber at pressures between 10⁻² to 10⁻⁴ mbar.
- Common PVD techniques include:
- Evaporation: Using cathodic arc or electron beam sources to vaporize the target material.
- Sputtering: Using magnetrons or other sources to bombard the target with ions, causing it to eject atoms that then deposit onto the substrate.
- Reactive gases like nitrogen, oxygen, or acetylene can be introduced during the process to create compound coatings.
-
Applications of PVD Coatings:
- Decorative Coatings: TiN and CrN are widely used for decorative purposes in jewelry, watches, and consumer electronics.
- Industrial Tools: PVD coatings like TiN, AlCr, and DLC are used to enhance the durability and performance of cutting tools, molds, and machine parts.
- Aerospace and Automotive: Specialized coatings like carbides, nitrides, and silicides are used in components that require high wear resistance, thermal stability, and corrosion resistance.
- Electronics: ITO coatings are used in displays and touch panels, while other coatings are used in semiconductors and sensors.
-
Customization and Versatility:
- PVD coatings are highly customizable, allowing for the combination of different metals, gases, and elements to create coatings with specific properties such as hardness, wear resistance, corrosion resistance, and optical characteristics.
- This versatility makes PVD coatings suitable for a wide range of industries, from consumer goods to high-tech applications.
By understanding the composition and properties of PVD coatings, purchasers can select the most appropriate materials and processes for their specific applications, ensuring optimal performance and durability.
Summary Table:
Component | Examples | Applications |
---|---|---|
Primary Metals | Titanium, Chromium, Aluminum, Zirconium, Tungsten | Tools, decorative coatings, machine parts, high-temperature applications |
Reactive Gases | Nitrogen, Oxygen, Carbon-based gases (e.g., Acetylene) | Nitrides, oxides, carbides, and diamond-like carbon (DLC) coatings |
Common PVD Materials | TiN, CrN, AlCr, ZnSn, ITO | Decorative, industrial tools, optical coatings, electronics |
Substrates | Metals, plastics, ceramics, glass | Aerospace, automotive, electronics, decorative applications |
PVD Techniques | Evaporation, Sputtering | Customized coatings for wear resistance, corrosion resistance, and optical needs |
Interested in custom PVD coatings for your industry? Contact us today to learn more!