The CVD (Chemical Vapor Deposition) coating technique is a process used to deposit thin-film coatings onto substrates through chemical reactions in a gas phase. It involves placing a substrate in a reaction chamber, introducing volatile precursors and inert gases, heating the substrate, and reducing the chamber pressure to activate reactions. The gas mixture decomposes or reacts with the substrate, forming a uniform and adherent coating. CVD coatings are known for their excellent adhesion, conformal coverage, and tailored properties, making them suitable for applications in semiconductors, dielectrics, and wear-resistant surfaces. However, the process can result in residual tensile stress, making coated equipment more fragile compared to PVD-coated alternatives.
Key Points Explained:
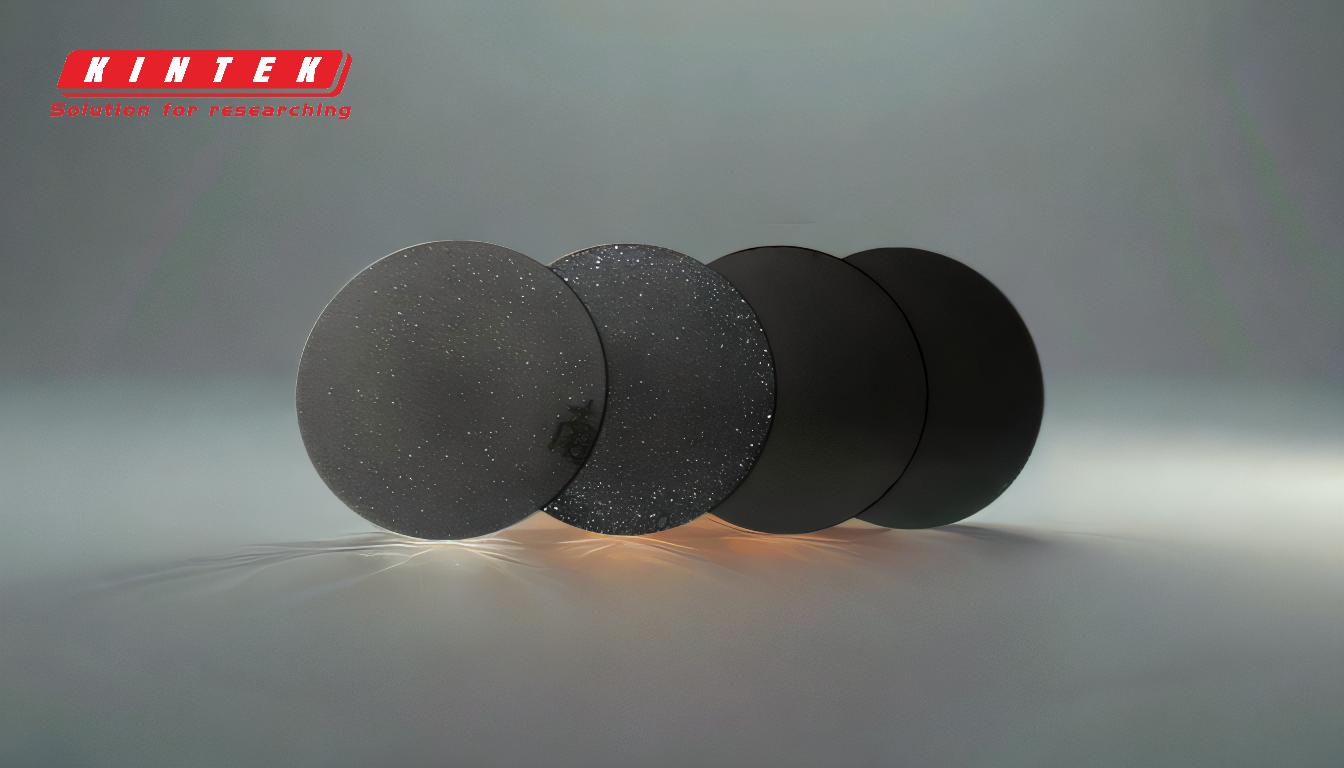
-
Definition of CVD Coating:
- CVD (Chemical Vapor Deposition) is a chemical process used to deposit thin-film coatings on substrates.
- It involves the reaction of gaseous precursors at high temperatures (around 1000 °C) to form hard, durable layers on the substrate surface.
-
Steps in the CVD Process:
-
Step 1: Substrate Placement and Gas Introduction:
- The substrate is placed inside a reaction chamber.
- A mixture of volatile precursors (reactive gases) and inert gases is introduced into the chamber.
-
Step 2: Heating and Pressure Reduction:
- The substrate is heated, and the chamber pressure is reduced to activate chemical reactions.
-
Step 3: Coating Deposition:
- The gas mixture decomposes or reacts with the substrate, depositing a thin-film coating.
-
Step 4: Byproduct Removal:
- Gaseous byproducts are removed and processed to prevent environmental pollution.
-
Step 1: Substrate Placement and Gas Introduction:
-
Applications of CVD Coatings:
- CVD is widely used in the semiconductor industry to deposit dielectric films (e.g., SiO2, Si3N4) and metal films (e.g., tungsten).
- It is also used for creating wear-resistant coatings on tools and components, especially for irregularly shaped surfaces.
-
Advantages of CVD Coatings:
- Excellent Adhesion: The coatings bond strongly to the substrate due to the chemical reaction process.
- Uniform and Conformal Coverage: CVD provides even coverage, even on complex geometries.
- Tailored Properties: Coatings can be engineered for specific properties like wear resistance, chemical resistance, or electrical conductivity.
- High Heat Resistance: Suitable for high-temperature applications.
- Versatility: Can deposit a wide range of materials, including semiconductors, metals, and dielectric films.
-
Limitations of CVD Coatings:
- Fragility: Coated equipment can be more fragile due to residual tensile stress during the process.
- High-Temperature Requirements: The process often requires temperatures around 1000 °C, which may not be suitable for all substrates.
- Environmental Concerns: Gaseous byproducts must be carefully managed to avoid pollution.
-
Comparison with PVD (Physical Vapor Deposition):
- CVD offers better step coverage and is more suitable for coating irregularly shaped surfaces.
- CVD coatings generally have higher resistance to abrasion and wear compared to PVD coatings.
- However, PVD coatings may result in less residual stress, making them less fragile than CVD-coated equipment.
-
Industrial Relevance:
- CVD is a critical technology in the production of semiconductors and electrical equipment.
- It is also used in industries requiring durable coatings for tools and components exposed to harsh conditions.
By understanding these key points, equipment and consumable purchasers can make informed decisions about when and where to use CVD coatings, balancing their advantages and limitations for specific applications.
Summary Table:
Aspect | Details |
---|---|
Definition | Chemical process for depositing thin-film coatings via gas-phase reactions. |
Process Steps | 1. Substrate placement & gas introduction. 2. Heating & pressure reduction. 3. Coating deposition. 4. Byproduct removal. |
Applications | Semiconductors, dielectric films, wear-resistant coatings. |
Advantages | Excellent adhesion, uniform coverage, tailored properties, high heat resistance. |
Limitations | Fragility, high-temperature requirements, environmental concerns. |
Comparison with PVD | Better step coverage, higher wear resistance, but more residual stress. |
Ready to explore how CVD coatings can enhance your applications? Contact us today for expert guidance!