The difference between cold type and hot type primarily lies in their application contexts, such as in printing, manufacturing, or industrial processes. Cold type refers to methods or processes that operate at or near room temperature, often involving less energy consumption and reduced risk of thermal damage. Hot type, on the other hand, involves high-temperature processes, which can provide faster results or stronger bonds but may require more energy and pose safety risks. The choice between cold and hot type depends on the specific requirements of the task, including material compatibility, efficiency, and safety considerations.
Key Points Explained:
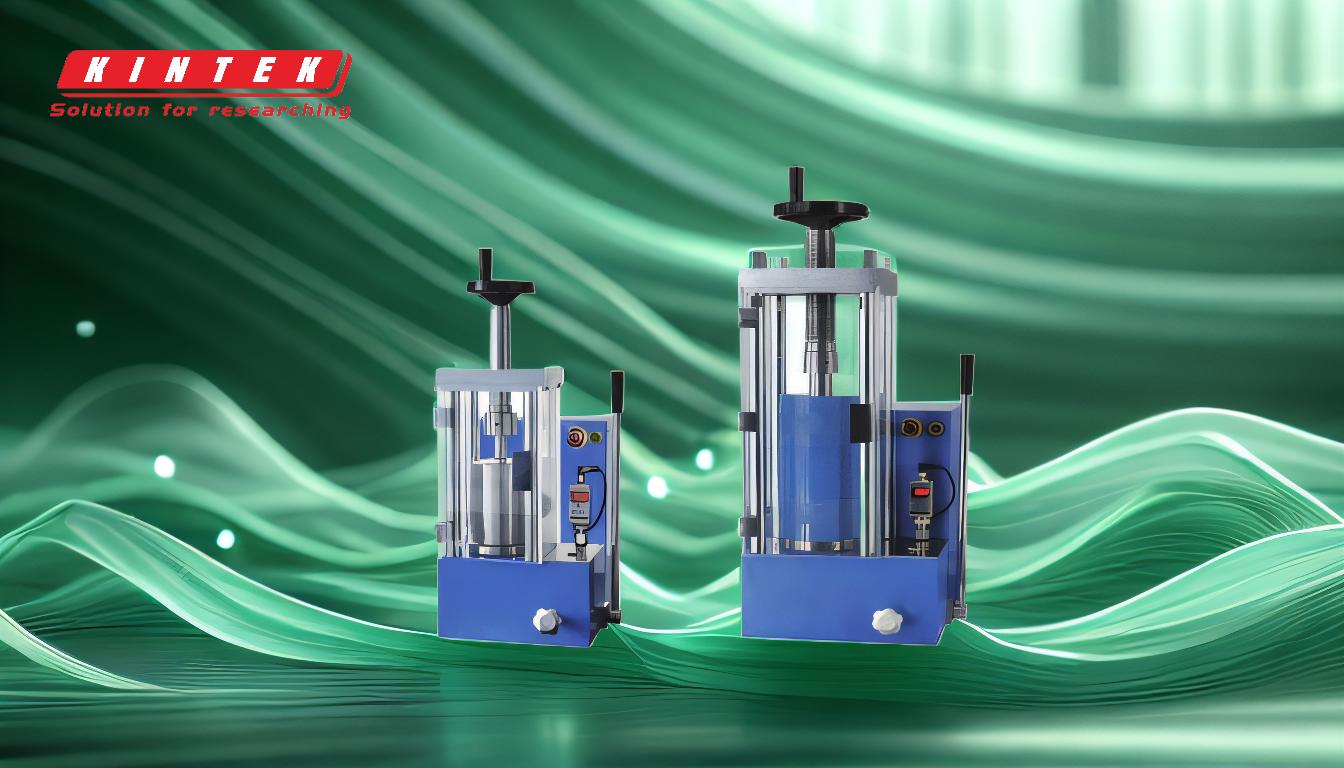
-
Temperature Requirements:
- Cold Type: Operates at or near room temperature, making it suitable for materials that are sensitive to heat. This method is often used in applications where thermal damage is a concern.
- Hot Type: Involves high-temperature processes, which can be necessary for tasks like melting, bonding, or curing materials that require heat to achieve the desired properties.
-
Energy Consumption:
- Cold Type: Generally consumes less energy since it does not require heating. This can lead to lower operational costs and a smaller environmental footprint.
- Hot Type: Typically requires more energy due to the need to generate and maintain high temperatures. This can result in higher operational costs and a larger environmental impact.
-
Safety Considerations:
- Cold Type: Safer to handle and operate, as there is no risk of burns or fire hazards associated with high temperatures. This makes it suitable for environments where safety is a priority.
- Hot Type: Poses greater safety risks, including the potential for burns, fire, and the release of harmful fumes. Proper safety measures and equipment are essential when working with hot type processes.
-
Material Compatibility:
- Cold Type: Ideal for materials that are sensitive to heat or prone to thermal degradation. It allows for the processing of delicate materials without compromising their integrity.
- Hot Type: Necessary for materials that require heat to achieve specific properties, such as strength, flexibility, or adhesion. It is often used in industries like metalworking, plastics, and ceramics.
-
Application Speed and Efficiency:
- Cold Type: May take longer to achieve the desired results, as it relies on chemical reactions or mechanical processes that occur at lower temperatures. However, it can be more precise and controlled.
- Hot Type: Generally faster, as heat accelerates chemical reactions and physical changes. This can lead to increased productivity, especially in high-volume manufacturing settings.
-
Cost Implications:
- Cold Type: Often more cost-effective in terms of energy consumption and equipment maintenance. It may also reduce the need for expensive safety measures.
- Hot Type: Can be more expensive due to higher energy requirements and the need for specialized equipment and safety protocols. However, the increased speed and efficiency may offset these costs in certain applications.
In summary, the choice between cold type and hot type depends on the specific needs of the application, including material properties, safety requirements, energy efficiency, and cost considerations. Each method has its advantages and limitations, and the decision should be based on a thorough evaluation of these factors.
Summary Table:
Aspect | Cold Type | Hot Type |
---|---|---|
Temperature | Operates at or near room temperature. | Involves high-temperature processes. |
Energy Consumption | Lower energy use, cost-effective, and eco-friendly. | Higher energy use due to heating requirements. |
Safety | Safer, with no risk of burns or fire hazards. | Poses safety risks like burns, fire, and harmful fumes. |
Material Compatibility | Ideal for heat-sensitive materials. | Necessary for materials requiring heat for strength or adhesion. |
Speed and Efficiency | Slower but precise and controlled. | Faster due to accelerated chemical reactions. |
Cost Implications | More cost-effective in energy and maintenance. | Higher costs due to energy and safety measures, but faster results. |
Need help choosing between cold type and hot type for your project? Contact our experts today!