Graphite is a versatile material widely used in high-temperature applications and various industries due to its thermal stability, durability, and electrical conductivity. Two common types of graphite are extruded graphite and isostatic graphite, which differ significantly in their manufacturing processes, properties, and applications. Extruded graphite is formed by forcing graphite paste through a die, resulting in a material with anisotropic properties, meaning its characteristics vary depending on the direction of measurement. In contrast, isostatic graphite is produced using a high-pressure molding process that ensures uniform properties in all directions, making it isotropic. This difference in production methods leads to variations in strength, thermal conductivity, and suitability for specific applications. Isostatic graphite is particularly valued for its high strength, excellent thermal shock resistance, and uniform properties, making it ideal for advanced industrial applications such as graphite furnaces, semiconductors, and aerospace components.
Key Points Explained:
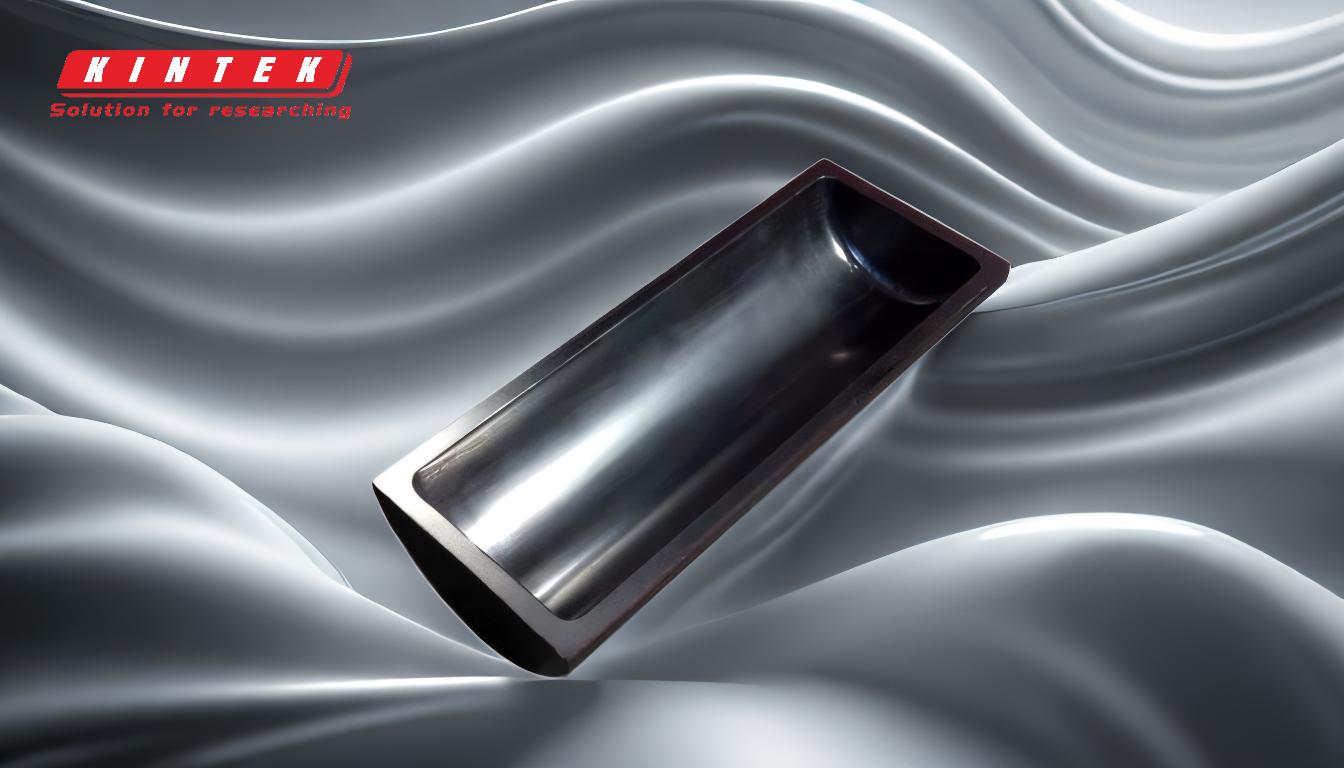
-
Manufacturing Process:
- Extruded Graphite: Produced by extruding graphite paste through a die, resulting in a material with anisotropic properties. This means its mechanical and thermal properties vary depending on the direction of measurement.
- Isostatic Graphite: Manufactured using a high-pressure isostatic molding process, which ensures uniform density and isotropic properties. This uniformity makes it highly reliable for applications requiring consistent performance in all directions.
-
Material Properties:
- Extruded Graphite: Exhibits directional properties, with higher strength and conductivity along the extrusion axis. However, it may have lower strength and thermal shock resistance perpendicular to the extrusion direction.
- Isostatic Graphite: Offers uniform properties in all directions, including high strength, excellent thermal shock resistance, and consistent electrical and thermal conductivity. It also has a low impurity content, making it suitable for high-purity applications.
-
Thermal and Electrical Conductivity:
- Extruded Graphite: Conductivity is higher along the extrusion axis but lower in other directions. This can limit its use in applications requiring uniform heat or electrical distribution.
- Isostatic Graphite: Provides consistent thermal and electrical conductivity in all directions, making it ideal for applications like graphite furnaces, where uniform heating is critical.
-
Applications:
- Extruded Graphite: Commonly used in applications where directional properties are acceptable, such as electrodes, crucibles, and structural components in less demanding environments.
- Isostatic Graphite: Preferred for advanced applications requiring high precision and uniformity, such as semiconductor manufacturing, aerospace components, and high-performance graphite furnaces.
-
Machinability and Purity:
- Extruded Graphite: Easier to machine due to its anisotropic structure, but may have higher impurity levels compared to isostatic graphite.
- Isostatic Graphite: Can be machined to very high precision and is often produced with extremely low impurity levels (< 5 ppm), making it suitable for high-tech industries.
-
Cost and Availability:
- Extruded Graphite: Generally more cost-effective and widely available, making it a popular choice for standard industrial applications.
- Isostatic Graphite: More expensive due to its advanced manufacturing process and superior properties, but essential for specialized applications requiring high performance and reliability.
In summary, while both extruded and isostatic graphite are valuable materials, their differences in manufacturing, properties, and applications make them suitable for distinct uses. Extruded graphite is ideal for cost-effective, less demanding applications, whereas isostatic graphite excels in high-performance, precision-driven industries such as those utilizing graphite furnaces.
Summary Table:
Aspect | Extruded Graphite | Isostatic Graphite |
---|---|---|
Manufacturing | Extruded through a die, anisotropic properties | High-pressure molding, isotropic properties |
Properties | Directional strength and conductivity, lower thermal shock resistance | Uniform strength, high thermal shock resistance, consistent conductivity |
Conductivity | Higher along extrusion axis, lower in other directions | Uniform in all directions |
Applications | Electrodes, crucibles, less demanding environments | Semiconductors, aerospace, high-performance graphite furnaces |
Machinability & Purity | Easier to machine, higher impurities | High precision machining, ultra-low impurities (< 5 ppm) |
Cost & Availability | Cost-effective, widely available | More expensive, specialized for high-performance applications |
Need help choosing the right graphite for your application? Contact our experts today!