Hot press sintering and Spark Plasma Sintering (SPS) are both advanced sintering techniques used to densify powdered materials into solid forms, but they differ significantly in their mechanisms, efficiency, and applications. Hot press sintering relies on external heating elements and pressure to achieve densification, while SPS employs a combination of Joule heating, pressure, and a pulsed DC voltage to enable faster sintering at lower temperatures. SPS is particularly notable for its rapid heating rates, ability to produce unique material characteristics, and versatility across a wide range of applications. Below, the key differences between these two methods are explored in detail.
Key Points Explained:
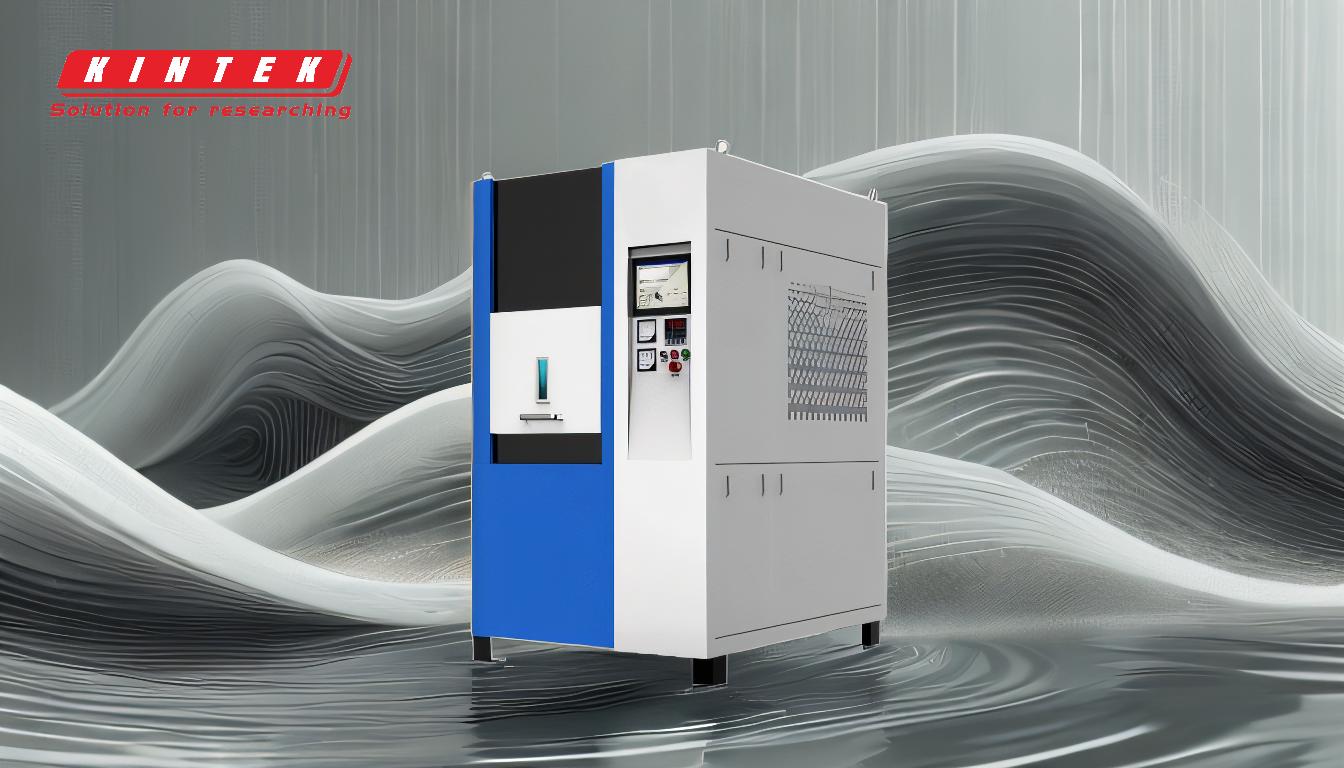
-
Heating Mechanism:
- Hot Press Sintering: Utilizes radiation from an external heating element to transfer heat to the powder compact. This process is slower and relies on thermal conduction through the material.
- SPS: Generates heat internally through Joule heating, where an electric current passes through the mold or the sample itself. This allows for extremely high heating rates, up to 1000°C/min, which is significantly faster than hot press sintering.
-
Energy Efficiency:
- Hot Press Sintering: Requires higher temperatures and longer sintering times, leading to greater energy consumption.
- SPS: Operates at lower temperatures and shorter times due to its rapid heating capabilities, making it more energy-efficient.
-
Pressure Application:
- Hot Press Sintering: Applies constant pressure throughout the sintering process, which can lead to uneven densification in some cases.
- SPS: Combines pressure with pulsed DC voltage, enhancing plastic deformation and promoting more uniform densification.
-
Sintering Speed:
- Hot Press Sintering: Typically has slower sintering rates, which can limit its application for materials requiring rapid processing.
- SPS: Achieves densification 10 to 100 times faster than conventional methods, making it ideal for materials that benefit from quick sintering.
-
Material Characteristics:
- Hot Press Sintering: Produces materials with standard properties, as the process is limited by slower heating and cooling rates.
- SPS: Enables the creation of materials with unique and potentially extraordinary characteristics due to its rapid heating and cooling, which can preserve fine microstructures and enhance material properties.
-
Versatility and Applications:
- Hot Press Sintering: Suitable for a wide range of materials but may not be as effective for advanced or complex materials.
- SPS: Has a broader application range, including nanomaterials, composites, and advanced ceramics, due to its ability to sinter at lower temperatures and shorter times.
-
Equipment Complexity:
- Hot Press Sintering: Uses relatively simpler equipment, making it more accessible for conventional sintering needs.
- SPS: Requires specialized equipment, including a pulsed DC power supply, which increases its complexity and cost but offers superior performance.
By understanding these key differences, equipment and consumable purchasers can make informed decisions about which sintering method best suits their material and production requirements. SPS, with its advanced capabilities, is particularly advantageous for cutting-edge applications requiring rapid processing and unique material properties.
Summary Table:
Aspect | Hot Press Sintering | Spark Plasma Sintering (SPS) |
---|---|---|
Heating Mechanism | External heating elements; slower, relies on thermal conduction | Internal Joule heating; rapid heating rates (up to 1000°C/min) |
Energy Efficiency | Higher temperatures and longer sintering times; greater energy consumption | Lower temperatures and shorter times; more energy-efficient |
Pressure Application | Constant pressure; may lead to uneven densification | Combines pressure with pulsed DC voltage; promotes uniform densification |
Sintering Speed | Slower sintering rates; limited for rapid processing | 10-100 times faster than conventional methods; ideal for quick sintering |
Material Characteristics | Standard properties due to slower heating/cooling rates | Unique and extraordinary characteristics; preserves fine microstructures |
Versatility | Suitable for a wide range of materials; less effective for advanced/complex materials | Broader application range, including nanomaterials, composites, and advanced ceramics |
Equipment Complexity | Simpler equipment; more accessible for conventional needs | Specialized equipment with pulsed DC power supply; higher complexity and cost |
Need help choosing the right sintering method for your materials? Contact our experts today!