Sintering and melting are two distinct processes used to combine or shape materials, particularly metals and ceramics. While both involve the application of heat, they differ fundamentally in terms of temperature, phase changes, and energy requirements. Sintering involves heating materials to just below their melting point, allowing particles to bond through diffusion without liquefying. This process is often aided by pressure and results in a solid structure with enhanced mechanical properties. Melting, on the other hand, requires heating a material to its melting point, causing it to transition from a solid to a liquid state. This phase change allows for the complete fusion of materials but often requires higher energy and can lead to imperfections. Sintering is particularly advantageous for materials with high melting points and offers better control over the final product's properties.
Key Points Explained:
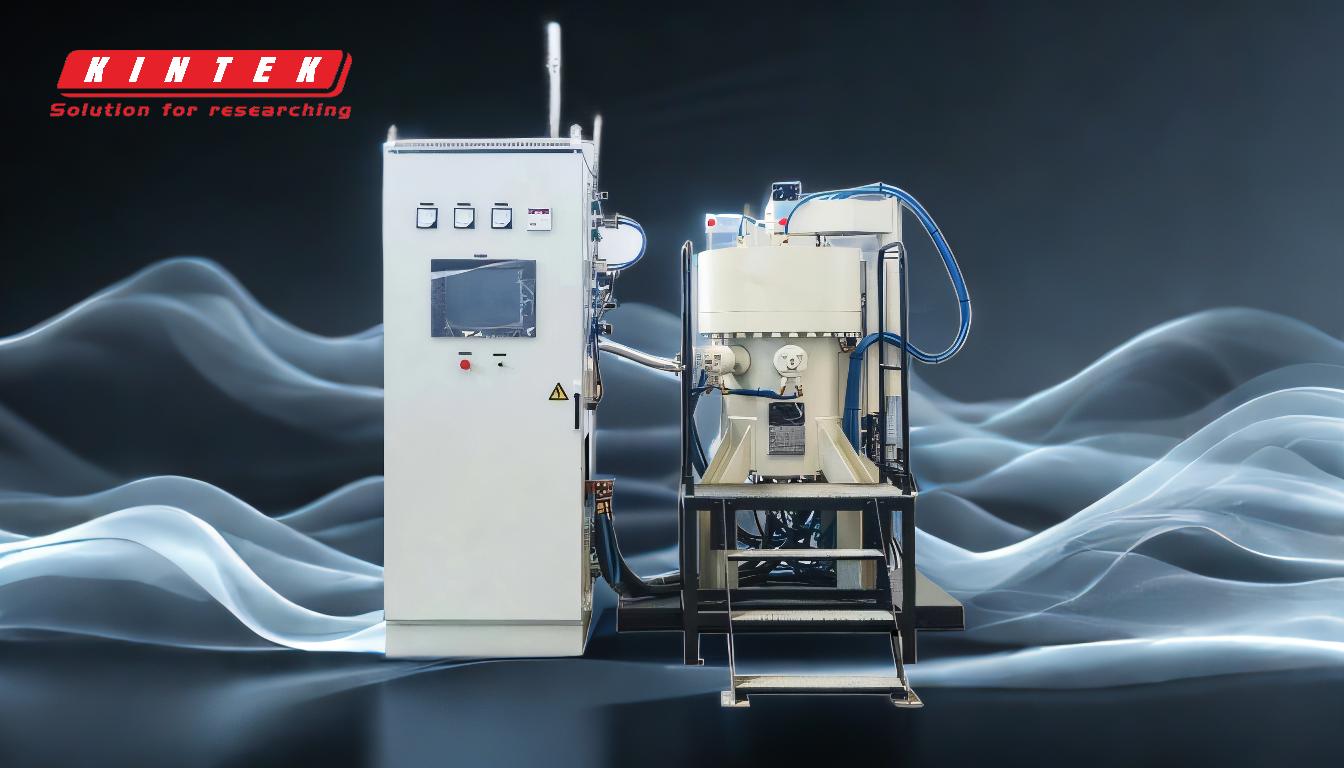
-
Temperature and Phase Change:
- Sintering: Occurs at temperatures just below the material's melting point. No phase change occurs; the material remains solid throughout the process.
- Melting: Requires heating the material to its melting point, causing it to transition from a solid to a liquid state.
-
Energy Requirements:
- Sintering: Requires less energy compared to melting because it operates at lower temperatures.
- Melting: Demands significantly more energy to achieve the high temperatures necessary for liquefaction.
-
Mechanism of Bonding:
- Sintering: Particles bond through diffusion, where atoms move across particle boundaries, leading to densification and bonding without melting.
- Melting: Particles combine by liquefying and fusing together, resulting in a homogeneous liquid that solidifies upon cooling.
-
Pressure Application:
- Sintering: Often involves the application of pressure to aid in the bonding process, enhancing the density and strength of the final product.
- Melting: Typically does not involve pressure, as the material is in a liquid state and can flow freely.
-
Material Properties:
- Sintering: Produces materials with improved mechanical properties such as strength and hardness. It is particularly useful for materials with high melting points.
- Melting: Can result in imperfections such as porosity or inclusions due to the high temperatures and phase changes involved.
-
Applications:
- Sintering: Commonly used in powder metallurgy, ceramics, and additive manufacturing to create complex shapes and components with controlled properties.
- Melting: Used in casting, welding, and other processes where complete fusion of materials is required.
-
Control and Consistency:
- Sintering: Offers greater control over the final product's properties, as the process occurs at lower temperatures and does not involve a phase change.
- Melting: Can be less predictable due to the high temperatures and potential for defects during the cooling and solidification process.
-
Suitability for High-Melting-Point Materials:
- Sintering: Ideal for materials with high melting points, as it avoids the need to reach those extreme temperatures.
- Melting: Less suitable for high-melting-point materials due to the high energy requirements and potential for material degradation.
In summary, sintering and melting are fundamentally different processes, each with its own set of advantages and applications. Sintering is a lower-energy process that bonds materials without melting, making it ideal for creating strong, complex parts from high-melting-point materials. Melting, on the other hand, involves complete liquefaction and is used in processes where full fusion of materials is necessary, albeit with higher energy costs and potential for imperfections.
Summary Table:
Aspect | Sintering | Melting |
---|---|---|
Temperature | Just below melting point | At or above melting point |
Phase Change | No phase change (remains solid) | Solid to liquid transition |
Energy Requirements | Lower energy due to lower temperatures | Higher energy due to high temperatures |
Bonding Mechanism | Diffusion bonding without melting | Liquefaction and fusion |
Pressure Application | Often used to enhance bonding | Typically not used |
Material Properties | Improved strength and hardness; ideal for high-melting-point materials | Potential for imperfections like porosity or inclusions |
Applications | Powder metallurgy, ceramics, additive manufacturing | Casting, welding, and full material fusion |
Control and Consistency | Greater control over final product properties | Less predictable due to high temperatures and defects |
Need help deciding between sintering and melting for your project? Contact our experts today for tailored advice!