The deposition temperature plays a critical role in determining the quality and properties of thin films. It influences key characteristics such as local state density, electron mobility, optical properties, and defect density. Higher deposition temperatures generally lead to denser films, improved surface reactions, and better film composition by compensating for dangling bonds and reducing defects. However, the application-specific requirements may impose limits on the temperature range that can be used during deposition. While deposition temperature has minimal impact on the deposition rate, it significantly affects the overall film quality, making it a crucial parameter in thin film fabrication processes.
Key Points Explained:
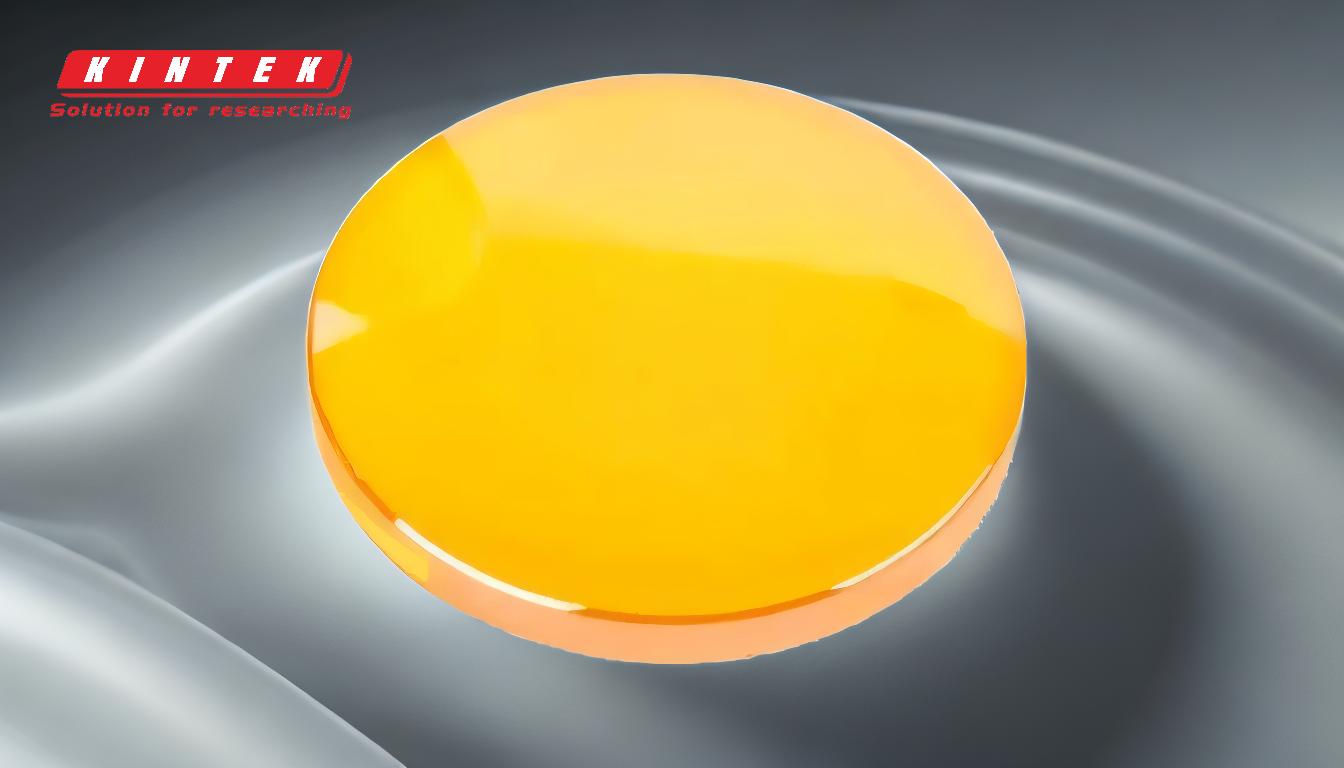
-
Impact on Film Quality:
- Deposition temperature directly affects the quality of the film by influencing properties such as local state density, electron mobility, and optical characteristics.
- Higher temperatures enhance the compensation of dangling bonds on the film surface, leading to a reduction in defect density and improved film integrity.
-
Film Density and Composition:
- Higher deposition temperatures result in denser films due to enhanced surface reactions and better atomic or molecular mobility during deposition.
- The improved mobility at elevated temperatures facilitates better film composition, ensuring uniformity and adherence to desired stoichiometry.
-
Defect Reduction:
- Elevated temperatures help reduce defects in the film by promoting the healing of structural imperfections and minimizing impurities.
- This leads to films with fewer voids, cracks, or other irregularities, which are critical for applications requiring high-performance materials.
-
Application-Specific Temperature Limits:
- While higher temperatures generally improve film quality, the specific application may impose constraints on the maximum allowable deposition temperature.
- For example, temperature-sensitive substrates or materials may require lower deposition temperatures to prevent damage or degradation.
-
Minimal Impact on Deposition Rate:
- Unlike other deposition parameters, such as pressure or gas flow rate, deposition temperature has little effect on the rate at which the film is deposited.
- This allows for fine-tuning of film quality without significantly altering the overall process time.
-
Optical and Electronic Properties:
- The optical properties of the film, such as transparency, reflectivity, and refractive index, are influenced by the deposition temperature.
- Similarly, electronic properties like conductivity and carrier mobility are enhanced at higher temperatures due to improved crystallinity and reduced defect density.
By carefully controlling the deposition temperature, manufacturers can optimize the quality and performance of thin films for specific applications, ensuring that the films meet the required standards for density, composition, and defect levels.
Summary Table:
Aspect | Effect of Higher Deposition Temperature |
---|---|
Film Quality | Improved local state density, electron mobility, and optical properties. |
Film Density | Denser films due to enhanced surface reactions and better atomic/molecular mobility. |
Defect Reduction | Reduced defect density, fewer voids, cracks, and irregularities. |
Temperature Limits | Application-specific constraints may limit maximum temperature. |
Deposition Rate | Minimal impact on deposition rate, allowing quality optimization without affecting process time. |
Optical/Electronic | Enhanced optical properties (transparency, reflectivity) and electronic properties (conductivity, mobility). |
Need help optimizing thin film deposition for your application? Contact our experts today to get started!